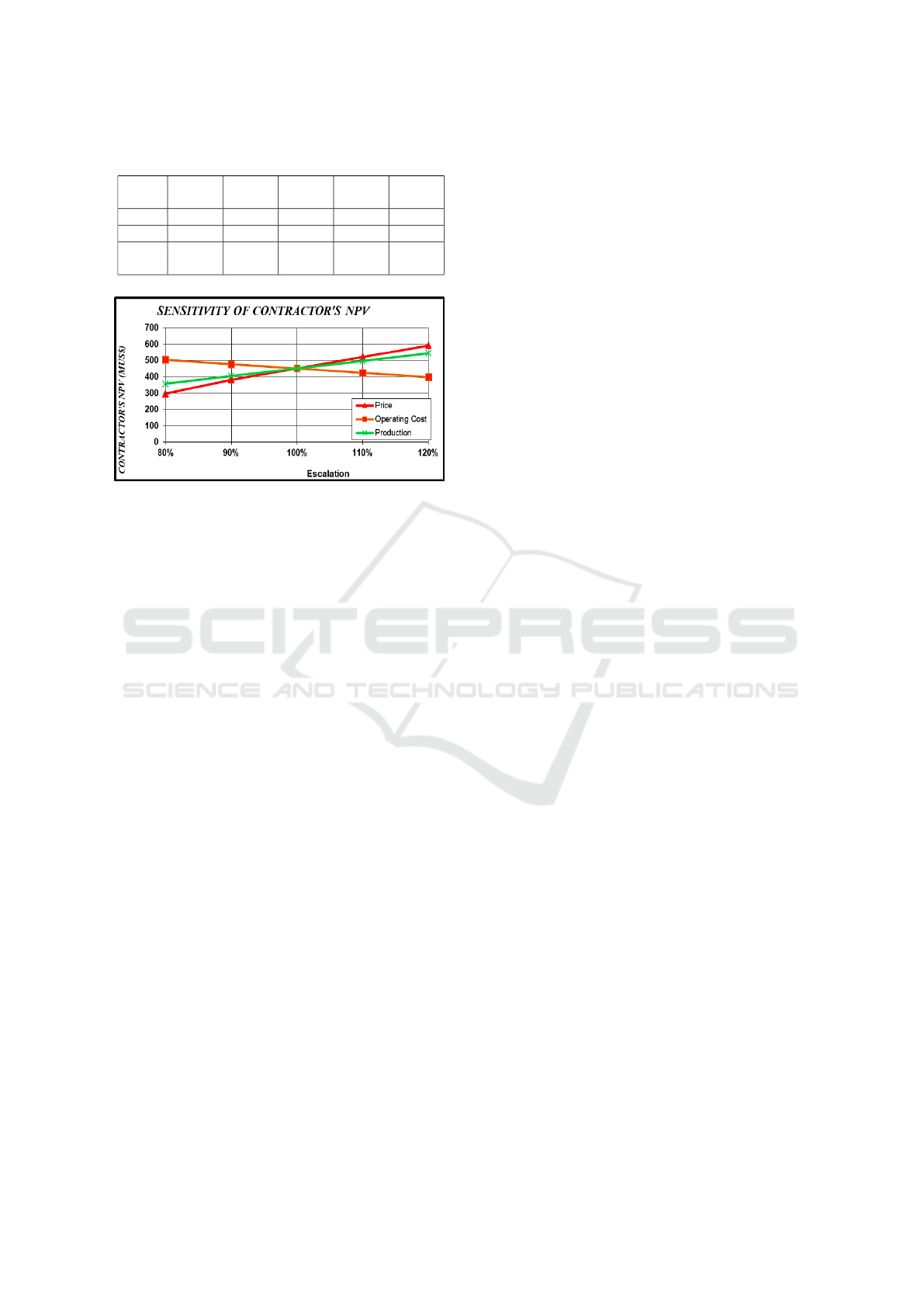
Table 12: Sensitivity analysis to production.
Years
80% 90% 100% 110% 120%
(Bbl/Y) (Bbl/Y) (Bbl/Y) (Bbl/Y) (Bbl/Y)
2017 58830 66190 73540 80890 88250
2018 52130 58650 65170 71680 78200
NPV
357.97 404.52 451.07 497.62 544.17
@15%
Figure 7: Sensitivity analysis.
and SL = 110 the production rate increased from
284 BFPD to 583 BFPD with EV = 90%. Based
on the results of production optimization for the next
2 years according to the time of HPU leasing, oil
production is 0.139 MMBBL, if it is assumed that
oil prices of US 52/BblareMMUS 7,213. Based
on the revenue sharing using the PSC system with
non-capital investments of MUS $ 0.150, the NPV
contractor MUS $ 451.07, IRR¿ MARR, POT <1
year and DPI 4.00 are obtained. From these results,
it can be seen for the next 2 years BM 1 and BM 2
wells are still economical to produce.
ACKNOWLEDGEMENTS
Thank you very much for supported by Universitas
Islam Riau and BOB PT. BSP Pertamina Hulu.
REFERENCES
Babbitt, J. A. and Vincent, K. (2012). Hydraulic Pumping
Units Proving Very Successful in Deliquifying Gas
Wells in East Texas. SPE Annual Technical
Conference and Exhibition.
Beard, D. (2013). Hydraulic pumping units proving
very successful in deliquifying gas wells in East
Texas. Society of Petroleum Engineers - North Africa
Technical Conference and Exhibition 2013, NATC
2013, 2.
Brown, K. E. (1984). The technology of artificial lift
methods, volume 4.
Chase, R. W. and Shaver, C. A. (2009). Optimal use of
vogel’s dimensionless ipr curve to predict current and
future inflow performance of oil wells. SPE Eastern
Regional Meeting, 295(5).
Cui, J., Xiao, W., Feng, H., Dong, W., Zhang, Y., and Wang,
Z. (2014). Long Stroke Pumping Unit Driven by
Low-Speed Permanent Magnet Synchronous Motor.
SPE Middle East Artificial Lift Conference and
Exhibition.
Hong, A., Bratvold, R. B., Lake, L. W., Maraggi,
R., and M., L. (2018). Integrating model
uncertainty in probabilistic decline curve analysis
for unconventional oil production forecasting.
SPE/AAPG/SEG Unconventional Resources
Technology Conference 2018, URTC 2018, (October
2018), 23–25.
Jennings, J. W. et al. (1989). The design of sucker rod
pump systems. In SPE Centennial Symposium at New
Mexico Tech. Society of Petroleum Engineers.
John, L. (1996). Decline Curve Analysis for Gas Wells.
Texas A&M University, College Station Texas.
Lubiantara, B. (2012). Ekonomi Migas Tinjauan Aspek
Komersial Kontrak Migas. Grasindo.
Ogunleye, A. O. (2012). Development of a Vogel type Inflow
Performance Relationship (IPR) for Horizontal wells.
SPE Annual Technical Conference and Exhibition.
Pickford, K. H. and Morris, B. J. (1989). Hydraulic rod
pumping units in offshore artificial lift applications.
SPE Production Engineering.
Wang, D. F., Cui, X. M., Gao, G. Y., Huang, Z. Z., and Hu,
B. Z. (1995). A New Long Stroke Pumping Unit with
High Speed. SPE Production Operations Symposium.
Wiggins, M. L., Russell, J. E., Jennings, J. W., et al.
(1996). Analytical development of vogel-type
inflow performance relationships. SPE Journal,
1(04):355–362.
Ye, Q., Wang, F., Wang, Y., Zhu, Y., Xu, J., Li, X.,
and Yang, G. (2017). Development and application
of pulley-free directly-connected hydraulic pumping
unit. Society of Petroleum Engineers - SPE/IATMI
Asia Pacific Oil and Gas Conference and Exhibition
2017.
ICoSET 2019 - The Second International Conference on Science, Engineering and Technology
108