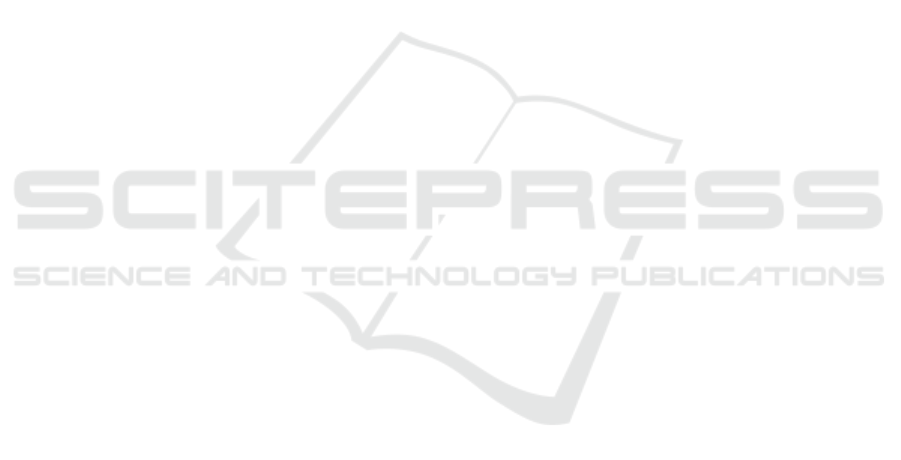
Mechanical Design of Knee and Ankle Exoskeleton to Help Patients
with Lower Limb Disabilities
Ignatius Deo Putranto
1
, Eka Budiarto
1
, Kidarsa, Lydia Anggraeni
2
1
Swiss German University, Alam Sutera, Indonesia
2
Bioteknik, Bandung, Indonesia
ideoputranto4@gmail.com, eka.budiarto@gmail.com, lydia@kidarsa.com
Keywords: Exoskeleton, Motorized, Knee, Ankle, Mechanical.
Abstract: In the medical world, exoskeleton in this project refers to an orthosis, which is applied externally to the
user’s body. This project aims to develop an exoskeleton with an affordable cost especially for assistance
and rehabilitation. This project mainly cover around the mechanical design of the product, covering of two
primary joints of the lower body part: knee and ankle. The overall size of the exoskeleton referring to limb
segments is limited to a select range of subject proportion. Each joint is to be motorized and equipped by
certain mechanism such as the application of linear actuator and four-bar linkage mechanism for the knee
and ankle joint, that enhances the efficiency with respect to speed and power transmission during actuations,
as well as the ability to deliver a smooth human locomotion. The types of body movement discussed is
around the sagittal plane which are flexion and extension for knee joint, including the dorsiflexion and
plantar flexion of the ankle joint. In order to help the patient regain the ability to move as mentioned, the
exoskeleton is made especially for external use with existing limbs for the lower body part to move, as well
as to endure the subject’s weight.
1 INTRODUCTION
The development of exoskeleton is one of the most
progressive topics in this decade, with each step that
aims to produce the most accurate lifelike motion
that makes the user feel as if it is part of their body
(Chen et al, 2015). Essentially, a human walk or
moves within the sagittal and frontal plane. The
application of exoskeleton is primarily utilized on
limbs which handles the person’s mobility and
stability. The means of an external actuations that
produce a movement on specific limbs, such as the
leg and arm, enhances the power of the
corresponding joints. Some of the applications are
widely used in the medicinal branch of orthotics that
aids people in moving their limbs as a form of
rehabilitation during their recovery. To be specific,
this project will prioritize on the support for the knee
and ankle joint.
In this current project, the main actuator to
simulate the knee and ankle joint will be using a
motor-powered linear actuator mechanism. To
achieve a more flexible and convenient design the
joint mechanism should mainly be considered, with
the fact that an actual knee joint has a slight
displacement that affects the shank (Wang et al,
2011). The hypothesis of this project is that the
mechanical design which includes linear actuator
and four-bar linkage could produce an efficient in
terms of strength and speed motion for the
exoskeleton to mimic human gait in terms of joint
angular motion.
16
Putranto, I., Budiarto, E. and Kidarsa, L.
Mechanical Design of Knee and Ankle Exoskeleton to Help Patients with Lower Limb Disabilities.
DOI: 10.5220/0009061600160027
In Proceedings of the 11th National Congress and the 18th Annual Scientific Meeting of Indonesian Physical Medicine and Rehabilitation Association (KONAS XI and PIT XVIII PERDOSRI
2019), pages 16-27
ISBN: 978-989-758-409-1
Copyright
c
2020 by SCITEPRESS – Science and Technology Publications, Lda. All rights reserved