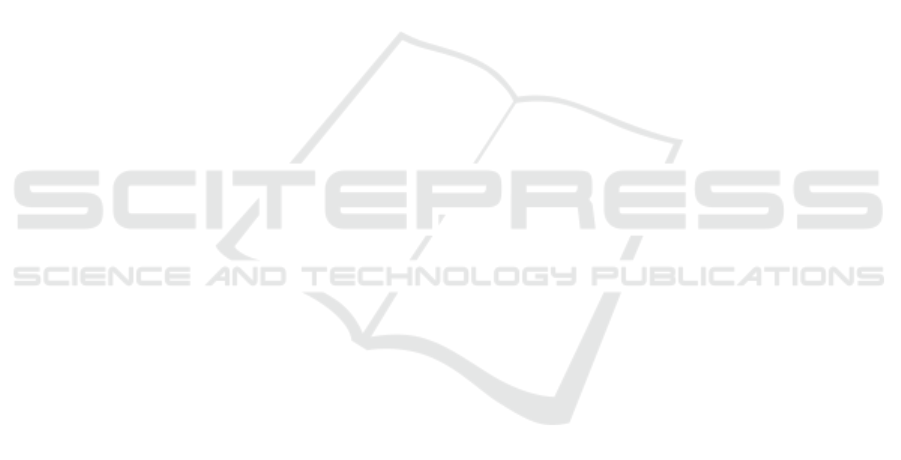
has pharmacological effects, such as accelerate
blood circulation and vital energy, eliminates
menstrual blockage, anti-inflammation, facilitates
labor, high antibacterial activity, facilitates the
release of bile (cholagogum), unleash fart and
mousturizier (astringen) (Melin and Soleha 2016).
Composite is a very interesting material because
it combines materials with different properties to
produce new materials with better properties.
Polymer nanocomposites are defined as polymers
containing materials smaller than 100 nm.
Nanocomposites are categorized in nanotechnology
if the resulting composite reflects the superiority of
nanomaterials, which is a significantly improved
performance. (Rudin and Choi, 2013).
2 MATERIALS AND METHODS
2.1 Materials
Acetobacter xylinum, Escherichia coli and
Staphylococcus aureus were purchased from
Microbiological Resources Centre, Thailand
Institute of Scientific and Technological Research
Nutrient broth (Approximate formula*per liter: Beef
extract 3.0 g and Peptone 5.0 g) was purchased from
Difco. Analytical grade D-glucose anhydrous was
purchased from Ajax Fine-chem. Yeast extract
powder and agar powder were bacteriological grade
and purchased from HiMedia. Laboratory grade
calcium carbonate and analytical grade silver nitrate
were purchased from Fisher Scientific. Laboratory
grade sodium borohydride was purchased from
CARLO ERBA. Analytical grade sodium hydroxide
anhydrate pellet and sodium chloride were
purchased from Aldrich Chemical. Analytical grade
glacial acetic acid was purchased from CSL
Chemical. Ethanol was commercial grade and used
without further purification.
2.2 Synthesize of Turmeric Extract
Turmeric used waa a fresh turmeric. The process of
making turmeric extract methanol is carried out
based on Yacob et al. (2010) using maceration and
evaporation methods. First, fresh turmeric washed,
drained, and dried for 3 days until the turmeric is
completely dry. After turmeric has completely dried,
dried turmeric was mashed until it become powder.
Turmeric powder soaked with ethanol until
homogeneous and then turmeric macerated for 3 x
24 hours. Maseration of turmeric powder was
filtered using whatman filter paper No.42. Fractions
containing volatile solvents, were concentrated with
the help of rotary evaporator. The concentrated
extract was unloaded to sterilized collecting tube
2.3 Production of Bacterial Cellulose
2.3.1 Culture-Medium
Culture medium used for the fermentation of A.
xylinum to produce bacterial cellulose consisted of
5 % glucose, 0.5 % bacto-peptone, 0.2 % disodium
phosphate, 0.1 % monocalium phosphate and the
addition of glacial acetic acid until the pH of the
culture medium reached 4. The solution was stirred
for 1 hour at 90⁰ C and followed by autoclave at
121⁰ C for 30 minutes.
2.3.2 Culture Condition
Pre-inoculum for all experiments was prepared by
transferring a single A. xylinum colony grown on
liquid culture medium into a 100 mL beaker glass
filled with liquid culture medium, then inoculated in
an incubator at 28 for 7 days with a rotational speed
of 100 rpm.
2.3.3 Purification of Bacterial Cellulose
After incubation, bacterial cellulose pellicles
produced on the surface of each liquid culture
medium were harvested and purified by soaking
them in 2.5 % NaOH for 24 h, then soaking them in
2.5% NaOCl for 24 h and finally thoroughly washed
in tap water until bacterial cellulose pellicles became
neutral and then immersed in the distilled water
prior to use.
2.3.4 Impregnation of Turmeric Extract
Into Bacterial Cellulose
The impregnation of turmeric extract into bacterial
cellulose using ex-situ method. Turmeric extract
were impregnated into bacterial cellulose fiber by
immersing bacterial cellulose pellicles in turmeric
extract until all the surface of bacterial cellulose
pellicles covered with turmeric extract. After then
bacterial cellulose pellicles impregnated for 24 h,
and then the nanocomposite rinsed with water to
remove turmeric sludge, the obtained nanocomposite
were frozen at and dried in a vacuum at -52⁰ C.
2.4 Characterization
The morphology of bacterial cellulose was observed
by using JEOL JSM-5200 scanning electron
microscope (SEM) operating at 20 kV at a
magnification of 10000.
ICOCSTI 2019 - International Conference on Chemical Science and Technology Innovation
298