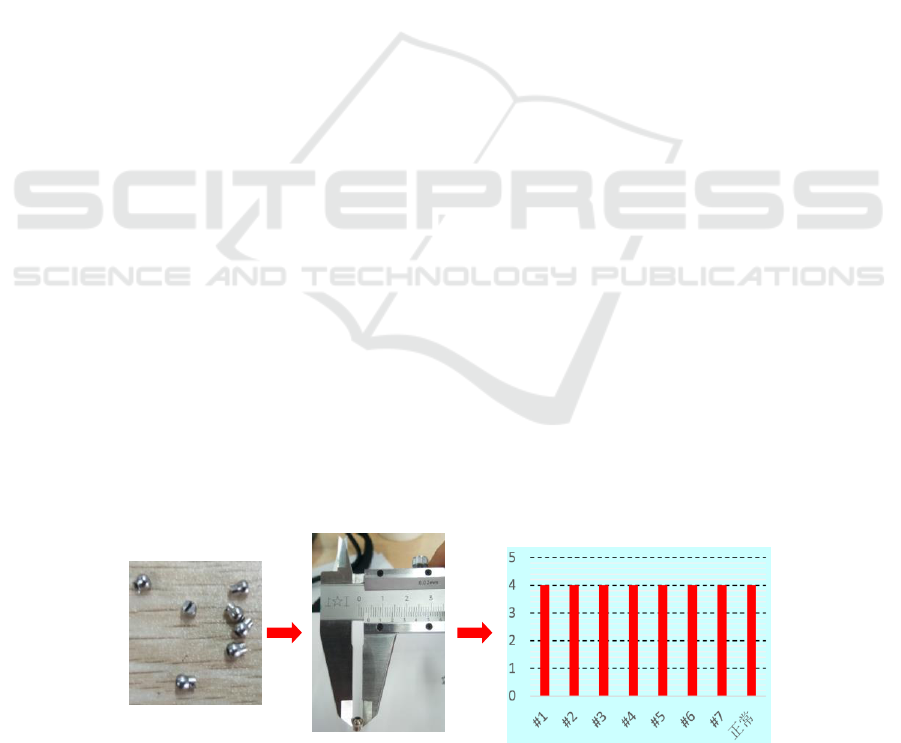
After dismantling of the old parts and test
analysis, confirm the main failure reasons might be:
ball core fracture basic appear in the winter, the
temperature decrease after the plastic parts of a
contraction, the matching of the nozzle and the spool
too tight, the user without the use of special
debugging tools debug copper ball, caused the ball
core fracture, this problem has become a problem to
be solved in practical production, it has a strong
production of practical significance.
2 FAILURE ANALYSIS OF
AUTOMOBILE WASHING
NOZZLE
2.1 Present Situation Investigation and
Cause Analysis
After the dismantling and test analysis of the old
parts, it is confirmed that the main failure reasons
are as follows:
(1) The core fracture basically occurs in winter,
and the plastic parts shrink after the temperature
decreases in winter, which leads to the over-tight
cooperation between the core and the nozzle.
(2) The root of the nozzle center groove is
designed to be at right angles, and the strength is
insufficient. Besides, users do not use special tooling
for debugging, which results in the fracture of the
ball core.
(3) The spraying Angle of the nozzle has been
fully adjusted in the factory inspection, and our
company used special tooling for debugging,
without considering the possibility of some users
adjusting the Angle of the nozzle.
The diameter of the ball head of the nozzle of the
fault part is 4mm, which meets the design
requirement of 4.1mm. Therefore, the root cause of
the non-ball head fracture problem is the ball head
size. Shrinkage rate of nozzle body material PA6
and nozzle ball head material POM varies with
temperature, and the actual shrinkage of plastic parts
is related to material thickness, so it is difficult to
control the interference amount of 0.05mm by
adjusting injection molding parameters such as
injection pressure, pressure holding time and
temperature.
The shrinkage rate of nozzle body and ball head
material varies with the temperature. When the
temperature changes, the shrinkage rate of nozzle
body PA6 is larger than that of ball head bronze,
leading to the increase of interference amount and
the increase of regulating power. In view of the
above situation, according to the requirements of the
nozzle and the adjustment process of the nozzle
Angle, it is proposed to calibrate the initial injection
Angle of the former nozzle according to the laws
and regulations, and make adjustment tools
according to the calibration samples. The nozzle
Angle is adjusted before the nozzle leaves the
factory, so as to avoid the ball head breaking when
the assembly factory adjusts the nozzle Angle.
2.2 Automobile Front Washing Nozzle
Improvement Program
The demand for automobiles is very high, and the
output of automobile enterprises keeps climbing, and
the quality requirements of products are very high
(M. Unno, A, 2017). Improving the structure and
strength of washing nozzle is an effective method to
improve the quality of nozzle (Shao wei, 2016). The
improvement of the nozzle must meet the service
conditions and meet the requirements of contact
surface injection. According to the characteristics of
the nozzle model, the main improved parts focus on
the size and shape of the nozzle, so as to achieve the
improvement aimed at improving the nozzle strength.
Figure 3. Nozzle ball head diameter measurement data.
ICVMEE 2019 - 5th International Conference on Vehicle, Mechanical and Electrical Engineering
60