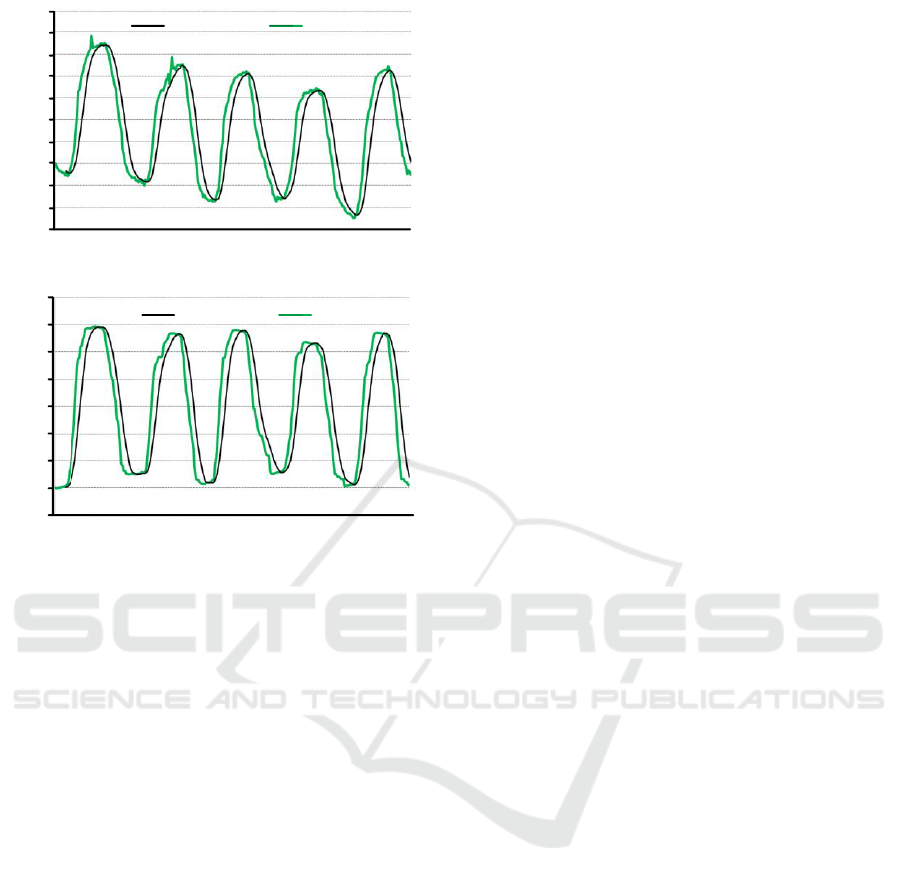
Moving average Data point
-10
-5
-15
5
10
0
20
25
15
35
30
Y Displacement variable quantity(mm)
Cycle(%)
(e)
Cycle(%)
Z Displacement variable quantity(mm)
Moving average Data point
-10
0
10
20
30
40
50
60
70
(f)
Figure 7. Diagrams of the GH joint motion information
relative to the sternum during humeral natural flexion and
extension rotation in five cycles: (a) humeral adduction
and abduction rotation angle, (b) humeral flexion and
extension rotation angle, (c) humeral internal and external
rotation angle, (d) X of the GH joint displacement variable,
(e) Y of the GH joint displacement variable, (f) Z of the
GH joint center displacement variable.
Fig. 7 shows the green curves (black lines is the
moving average) for the tester performing humerus
flexion/extension nature movement in five cycles
and the angle range is about 120°. The movements
of the GH joint in three dimensionsin
(adduction/abduction, flexion/extension, and
internal/external) and the GH joint center
displacement variable in the X, Y, and Z directions
are observed, which are presented in (a), (b), (c), (d),
(e), and (f), respectively. During the nature
flexion/extension movement of the humerus, a small
amount of adduction as well as abduction and
internal as well as external movement occurs with
the lifting process. This phenomenon is normal
during the natural flexion/extension movement of
the humerus, because it is impossible for the
humerus lifting process to completely guarantee in
the sagittal plane. However, the GH joint center
displacement variable large and regular in the X, Y,
and Z directions confirmed the coupled motion of
the shoulder complex. Subsequently, a great deal of
tests and analyses were performed, the above similar
results are also presented.
4 CONCLUSIONS
In this paper, a kinematic model of the shoulder
complex (3-DOF GH joint with floating center) was
proposed. Then, a detection system was designed.
Real-time GH joint motion information was
obtained, which confirmed the rationality of the
shoulder complex model and detection system.
It provides a method to obtain the movement
information of the GH joint and the detection system
can obtain the fundamental motion data of human
shoulder motion. Which has practical significance
for shoulder function simulation and ergonomics.
ACKNOWLEDGEMENTS
This work was supported by the National Natural
Science Foundation of China under Grants No.
51675008 and No. 51705007, the Beijing Natural
Science Foundation under Grants No. 3171001 and
No. 17L20019.
REFERENCES
B. Tondu, “Modelling of the shoulder complex and
application the design of upper extremities for
humanoid robots”, in Proc. 2005 5th IEEE-RAS Int.
Conf. Humanoid Robots., Tsukuba, Japan, 2006, pp.
313-320.
J. Lenarčič et al, “Positional kinematics of humanoid
arms”, Robotica. vol. 24, no. 1,January, 2006.
J. Yang et al, “Reach envelope of a 9-degree-of-freedom
model,” Int J Rob Autom., vol. 20, no. 4, pp. 240-259,
2005.
K. Kiguchi et al, “Design of a 7DOF upper-limb power-
assist exoskeleton robot with moving shoulder joint
mechanism,” in IEEE Int. Conf. Rob. Biomimetics,
Phuket, Thailand, 2011, pp. 2937-2942.
N. Klopčar and J. Lenarčič, “Bilateral and unilateral
shoulder girdle kinematics during humeral elevation,”
Clin. Biomech. vol. 21, no. supp-S1, pp. 20-26, 2006.
N. Tobias, et al. ARMin III ‒ Arm Therapy Exoskeleton
with an Ergonomic Shoulder Actuation. Appl. Bionics.
Vol. 6 (2009) No. 2, p. 127-142.
R. F. Kirsch et al, “Model-based development of
neuroprostheses for restoring proximal arm function”,
J. Rehabil. Res. Dev, vol. 38, no. 6, pp. 619-626, 2001.
W. Maurel, et al, “Human shoulder modeling including
scapulo-thoracic constraint and joint sinus cones,”
Comput. Graph-uk., vol. 24,no. 2, pp. 203-218, 2000.
ICVMEE 2019 - 5th International Conference on Vehicle, Mechanical and Electrical Engineering
226