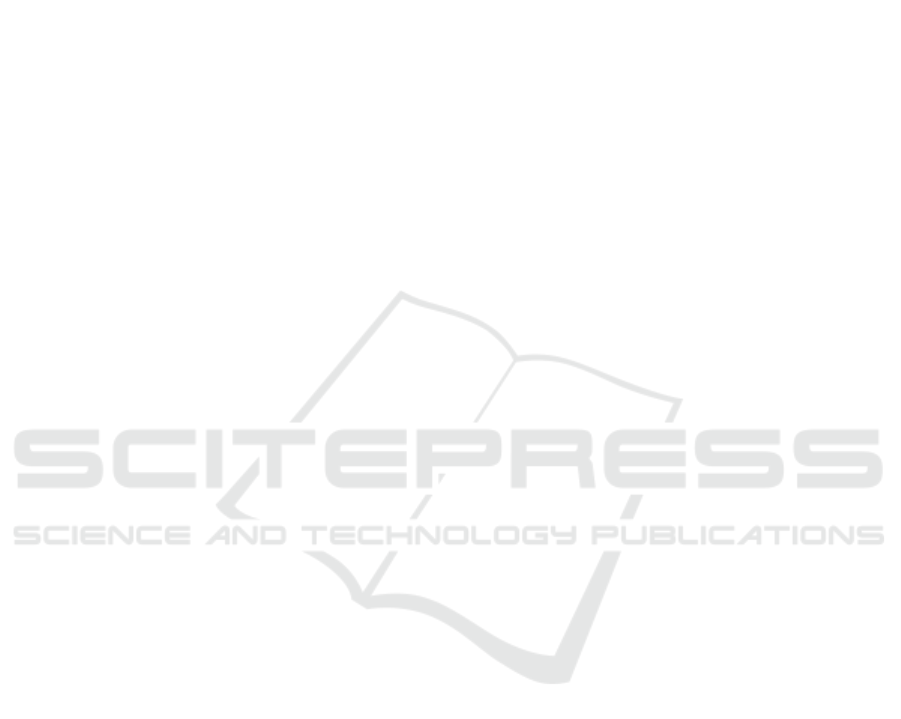
Research on Fault Diagnosis of Hydraulic Oil Leakage in the ABS
System of Automobile
Yue Liang
1, a, *
, Zhixiao Wang
1, b
, Zhichun Wang
1, c
1
Hunan Defense Industry Polytechnic, Xiangtan, Hunan, China
Keywords: Oil leakage, ABS failure, dynamic signal, car safety.
Abstract: At present, the self-test of ABS system cannot detect faults in mechanical parts, such as solenoid
valve clamping and hydraulic oil leakage. In an indoor environment, a dynamic monitoring
system is built that uses sound signals, vibration signals and pressure signals to detect mechanical
parts of the ABS system. The hydraulic oil leakage failure will cause the oil pressure to decrease,
fail to meet the working conditions of the hydraulic system, and reduce the working efficiency.
In severe cases, the hydraulic system may even fail, which may cause the ABS system to
malfunction and cause a traffic accident. The mechanical fault diagnosis of the automotive ABS
system is an important way to ensure the safe operation of the vehicle and the good performance
of the ABS system.
1 INTRODUCTION
At present, the self-test of the ABS system can only
detect electrical faults such as open circuit and short
circuit, while typical faults of the mechanical part,
such as hydraulic oil leakage faults, are not within
the scope of its self-test. Independently build a
dynamic monitoring system built in an indoor
environment, using sound signals, vibration signals
and pressure signals to detect mechanical parts of
the ABS system. The mechanical fault diagnosis is
an important way to ensure the safe operation of the
vehicle and the good performance of the ABS
system.
In addition to the in-depth research conducted by
manufacturers of ABS systems, scholars currently
studying in universities and research institutes in
China have studied the fault diagnosis technology of
ABS systems, they have proposed many simulation
analysis of the faults diagnostic methods, these
studies have laid the foundation for further in-depth
research, which greatly stimulated the research
interest in the field of ABS system fault research and
urged efforts to solve the faults. (Struss P, 1997) The
ABS system and its failures have been studied very
early in the world, such as Peter Struss of the
Technical University of Munich, and Martin
Sachenbacher of BOSCH, who use the automation
and intelligent inference techniques to troubleshoot
the ABS system. A team of Professor Harald Straky
from Darmstadt University of Technology built a
real-time observation system for hydraulic brakes
based on the residual method, they used hydraulic
control models to detect hydraulic system air mixing
and brake fluid leakage.
2 THE FAULT OF HYDRAULIC
OIL LEAKAGE
During the operation of the hydraulic system, due to
the high pressure value in the hydraulic pipe or the
gap between the installation components of the
hydraulic system. (Sachenbacher M, Struss P, Carl,
et al, 2000) When the pressure reaches a certain
value, a small amount of hydraulic oil leakage will
occur in the gap between the systems or components.
This leakage will result in a reduction in oil pressure
in the hydraulic system and will not meet the
operating conditions of the hydraulic system. It will
also reduce the working efficiency of the hydraulic
system. When a hydraulic oil leak occurs in the
hydraulic system of the ABS system, the pressure in
the hydraulic cylinder and the amount of leakage in
the cylinder
determine the value of a leak. The
pressure
is a linear relationship with the brake
50
Liang, Y., Wang, Z. and Wang, Z.
Research on Fault Diagnosis of Hydraulic Oil Leakage in the ABS System of Automobile.
DOI: 10.5220/0008865400500053
In Proceedings of 5th Inter national Conference on Vehicle, Mechanical and Electrical Engineering (ICVMEE 2019), pages 50-53
ISBN: 978-989-758-412-1
Copyright
c
2020 by SCITEPRESS – Science and Technology Publications, Lda. All rights reserved