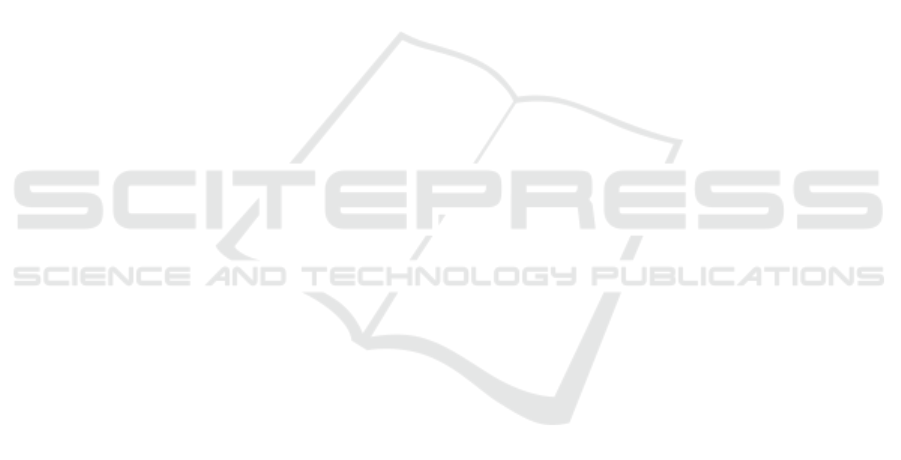
increase the temperature better than spritus and
kerosene but not compared to gasoline. In addition,
bioethanol has other advantages, which are odorless
and do not cause soot in process. The practical use
of bioethanol gel is directly burned, unlike other
fuels that use intermediaries such as axes (Nugroho,
2016).
4 CONCLUSIONS
Based on the results of the research it can be
concluded that bioethanol gel as an alternative fuel
can be produced from hydrolysis of bagasse pulp
and then fermented with Saccharomyces cerevisiae
for 4 days and adding carbopol as thickener. The
best results were obtained with variations of
carbopol 1.8 g and 1 mL NaOH with gel flowing
forms. The characteristics of the bioethanol gel
were: flame length 239 seconds (3 minutes 59
seconds), residue 0.03 g, heating value 33.064,25 kJ
/ kg, and 5 g bioethanol gel can raise the water
temperature to 50 °C.
ACKNOWLEDGEMENTS
The authors would like to send gratitude to Risekti
dikti for the financial support towards this research
in the PKM-PE Project 2019 and also for
Universitas Sumatera Utara which facilitated this
research.
REFERENCES
Bano, S., Negi, Y. S., 2017. Studies on cellulose
nanocrystals isolated from groundnut shells.
Carbohydr. Polym. 157, 1041–1049.
Dewi, R. K., Poespowati, T., Jimmy, 2018. Natrosol
sebagai Salah Satu Bahan Pengental (Thickener) pada
Produksi Bioetanol Gel dari Limbah Daun Tebu.
Indones. Chem. Appl. J. 2, 1–6.
Epriadi, R., 2017. Isolasi Nanoserat Selulosa dari Tandan
Kosong Sawit (Elais guinensis jack) dengan
menggunakan Tempo. Universitas Sumatera Utara.
Gea, S., 2019. The Preparation of All-Cellulose
Nanocomposite Film from Isolated Cellulose of
Corncobs as Food Packaging The Preparation of
Cellulose Nanocomposite Film from.
Hanun, V., Sutjahjo, D., 2018. Komparasi karakteristik
bioetanol gel dengan pengental karbopol dan
carboxylmethyl cellulase (CMC) sebagai bahan bakar
alternatif. Tek. Mesin.
Irvan, Prawati, P., Trisakti, B., 2015. Pembuatan Bioetanol
dari Tepung Ampas Tebu Melalui Proses Hidrolisis
Termal dan Fermentasi: Pengaruh pH, Jenis Ragi dan
Waktu Fermentasi. Tek. Kim. USU 4, 27–31.
Lloyd, P. J. D., Visagie, E. M., 2007. A comparison of gel
fuels with alternative cooking fuels 18, 26–31.
Merdjan, R., Matione, J., 2003. Fuel Gel [WWW
Document]. United State Patents Appl. Publ.
Nugroho, A., Restuhadi, F., Rossi, E., 2016. Pembuatan
Gel Etanol denganMenggunakan Bahan Pengental
Carboxymethycellulose (CMC). Jom Faperta 3.
Oktavia, T., Sumiyati, S., Sutrisno, E., 2013. Pemanfaatan
Limbah Cair Cucian Beras sebagai Bahan Baku
Pembuatan Bioetanol Padat Secara Fermentasi oleh
Saccharomyces cerevisiae. Universitas Diponegoro.
Robinson, J., 2006. Bioethanol as a household cooking
fuel: a mini pilot study of the superblu stove in peri-
urban Malawi. Loughborough University.
Tambunan, L., 2008. Bioetanol Anti Tumpah 39, 24–25.
Turns, S., 2000. An Introduction To Combustion :
Concept And Applications, 2nd ed. McGraw-Hill
Book Company Singapore, Singapore.
Wibowo, W. A., Mulyono, T. S., 2010. Pembuatan dan
Uji Pembakaran Ethanol Gel. Ekuilibrium 9, 67–71.
Xu, C., Zhu, S., Xing, C., Li, D., Zhu, N., 2015. Isolation
and Properties of Cellulose Nanofibrils from Coconut
Palm Petioles by Different Mechanical Process 1–11.
Yogesthinaga, Y., 2016. Optimasi Gelling Agent Carbopol
dan Humektan Propilen Glikol dalam Formulasi
Sediaan Gel Ekstrak Etanol Daun Binahong (Anredera
cordifolia (Ten.) Steenis). Universitas Sanata Dharma.
Production of Bioethanol Gel from Sugar Cane Waste with Carbopol as Alternative Fuel
129