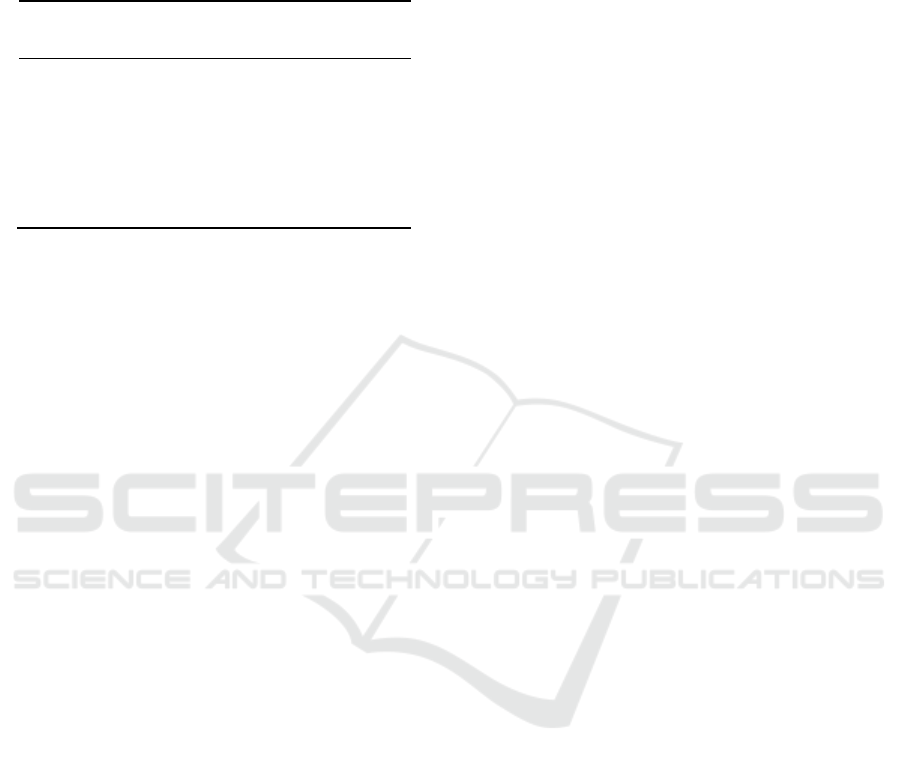
models. The results are compared as shown in Table
5.
Table 5. The contact forces calculated with different
models.
Error with exhaustive
method
Model proposed
in this paper
Optimized ZMC
Contact Model
Iida exhaustive
contact model
According to the calculation result, the fitting
model proposed in this paper is basically consistent
with the exhaustive model. Meanwhile, it can be
found that the model without considering the
interaction will produce great errors.
4 CONCLUSION
In this paper, the traditional micro-contact model of
rough surfaces is optimized in order to consider the
accuracy and efficiency of calculation compre-
hensively. The deformation distribution law of
asperities considering interaction is studied by using
Iida exhaustive model. Fitting function is established
to describe the distribution of asperities under micro-
interaction through data analysis. Therefore, a new
contact model of rough surfaces is proposed.
Compared with the optimized ZMC model and Iida
exhaustive model, the correctness of the proposed
model and the non-negligibility of the interaction are
verified.
ACKNOWLEDGEMENTS
The work was supported by 2017 Science and
Technology Support Plan of Nanjing Jiangsu China
(Grant No. 201701213) and 2018 Science and
Technology Support Plan of Yunnan China (Grant
No. 2018IC30).
REFERENCES
Abbott E., Firestone F., et al. 1995, Specifying surface
quality: a method based on accurate measurement and
comparison. Spie Milestone Series MS, 107: 63-63.
Chang W., Etsion I., et al. 1987, An elastic-plastic model
for the contact of rough surfaces. Journal of tribology,
109(2): 257-263.
Ciavarella M., Delfine V., et al. 2006, A “re-vitalized”
Greenwood and Williamson model of elastic contact
between fractal surfaces. Journal of the Mechanics
and Physics of Solids, 54(12): 2569-2591.
Francis H., 1976, Phenomenological analysis of plastic
spherical indentation. Journal of Engineering
Materials and technology, 98(3): 272-281.
Greenwood J., Williamson J., 1966. Contact of nominally
flat surfaces. Mathematical and physical sciences,
295(1442): 300-319.
Iida K., Ono K. 2003, Design consideration of
contact/near-contact sliders based on a rough surface
contact model. Journal of tribology, 125(3): 562-570.
Johnson K., Johnson K., et al. 1987, Contact mechanics.
Cambridge university press.
Kogut L., Etsion I., 2002, Elastic-plastic contact analysis
of a sphere and a rigid flat. Journal of applied
Mechanics, 69(5): 657-662.
Li L, Cai A., Cai L., et al. 2016, Micro-contact Model of
Bolted-joint Interface. Chinese Journal of Mechanical
Engineering, 52(07): 205-212.
Lin L., Lin J., 2005, An elastoplastic microasperity contact
model for metallic materials. Journal of Tribology,
127(3): 666-672.
Liou J., Tsai C., et al. 2010, A microcontact model
developed for sphere-and cylinder-based fractal bodies
in contact with a rigid flat surface. Wear, 268(3-4):
431-442.
Timoshenko S., Goodier J.N. 1990, Theory of Elasticity.
Translated by Xu Zhilun. Beijing, China: Higher
Education Press, 481-489.
Xiao H., Sun Y., et al. 2019, Fractal modeling of normal
contact stiffness for rough surface contact considering
the elastic–plastic deformation. Journal of the
Brazilian Society of Mechanical Sciences
and Engineering, 41(1): 11.
Zhao Y., Lu Y., et al. 2007, New elastic-plastic model for
the contact of rough surfaces. Chinese Journal
of Mechanical Engineering, 43(3): 95-101.
ICVMEE 2019 - 5th International Conference on Vehicle, Mechanical and Electrical Engineering
202