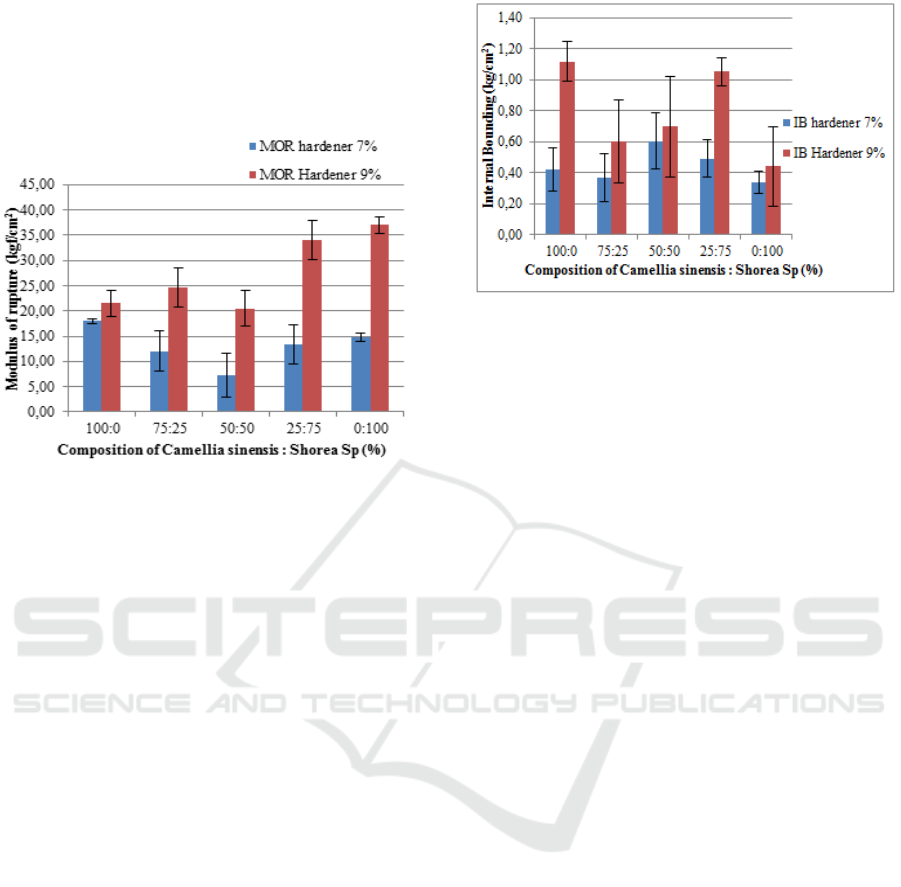
addition of the hardener decreases the tensile
strength. This is because there are many small cavities
in the material which reduce the mechanical strength
of the material. The modulus of elasticity also
increases when the tensile strength increases.
Figure 5: Modulus of rupture of particleboards.
Modulus of rupture values of particleboards
ranged from 7.28-41.03 kg/cm2. Figure 5 shows that
the highest modulus of rupture is found on
particleboards made of 100% meranti wood using an
adhesive hardener content of 9%. While the lowest
modulus of rupture value is found on the
particleboard using adhesive with hardener content of
7%.
The modulus of rupture on the particleboard
affected by the particleboard density. The lower the
density of the particleboard, the lower the modulus of
rupture produced. According to Haygreen and
Bowyer (1996) that the factors that affect the low or
high of modulus of rupture are influenced by the
density of the board, so that the bond between the
boards becomes less tight so due to reduce on the
modulus of rupture value. Addition of tea leaf waste
to the particleboard causes a decrease in the value of
modulus of rupture of particleboard (Batiancela et al.,
2014). This is due to the low content of chemical
compounds in tea leaves in the form of cellulose and
hemicellulose so that the mechanical strength
produced by particleboards from tea leaf waste
powder is also very low (Shi et al., 2006).
Figure 6: Internal bonding of rupture of particleboards.
Figure 6 shows the average value internal bonding
of particleboard ranged from 0.33-1.12 kg/cm
2
. The
highest value of internal bonding on particleboard
from 100% tea leaf waste with hardener content 9%
which is 1.12 kg/cm
2
while the lowest on meranti
wood particle board 100% at hardener content 7%
which is 0.33 kg/cm
2
. High content of adhesive with
high hardener content can increase the internal
bonding value of particleboard. The hardener used in
making this particleboard is NH
4
CL which can make
the acidic condition so that UF adhesives become
curing or mature (Nuryawan, 2016).
Internal bonding value of the particleboard from
tea leaf waste is higher than the meranti wood
particleboard. In accordance with the research of
Batiancela et al., (2014) which states that adhesive
firmness increased from 148 to 346 kPa with an
increase in the proportion of tea leaf waste. Increasing
the adherence of adhesion can be attributed to good
pressure on the particle board pressing process and
the bonding between particles that occurs due to the
content of chemical compounds in tea leaf waste. Tea
leaf waste contains 4-7% cellulose, 5-6%
hemicellulose, and 5-6% lignin.
Table 1 shows the value of formaldehyde
emissions on particle boards from tea leaf waste and
meranti wood waste ranging from 0.95mg / L-
6.045mg / L. The particle board formaldehyde
emission using adhesive with a hardener content of
7% higher than the particle board with 9% hardener
content. This is because of the variation in density on
each board. The average particle board density used
for formaldehyde emission testing is in the range of
0.73-0.84g / cm3. The higher the density of the
particle board, the lower the formaldehyde emissions
released. This is due to the lack of cavities or pores
on the particle board so that the emissions released
will be smaller (Sutigno and Santoso, 1995). Based
on the emission value, it can be seen that the addition
Characterization of Particleboard from Waste Tea Leaves (Camellia Sinensis L) and Meranti Wood (Shorea Sp) using Urea-Formaldehyde
Adhesive and It’s Formaldehyde Emission
263