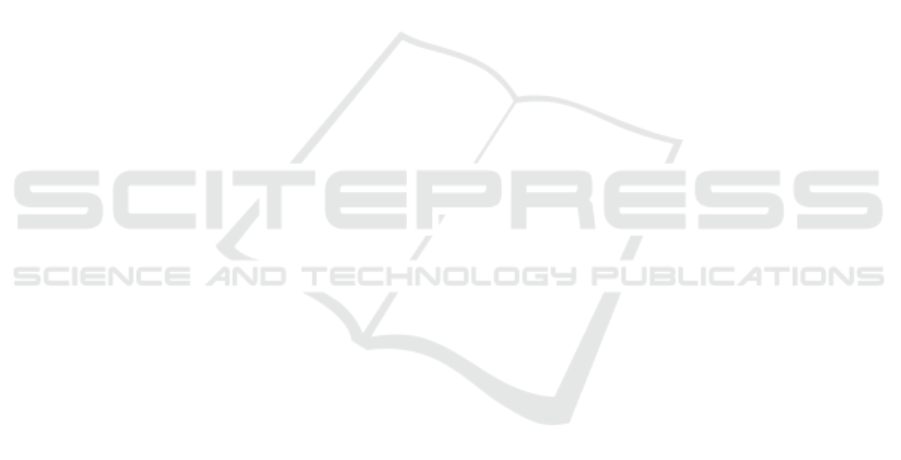
Saccharomyces cerevisiae. In: AIP Conference
Proceedings. In p. 20026. Available at:
http://aip.scitation.org/doi/abs/10.1063/1.4978099
[Accessed March 30, 2017].
Johnson, E. 2016. Integrated enzyme production lowers
the cost of cellulosic ethanol. Biofuels, Bioproducts
and Biorefining, 10(2), pp.164–174. Available at:
http://doi.wiley.com/10.1002/bbb.1634 [Accessed
March 30, 2017].
Klein-Marcuschamer, D., Simmons, B. A., Blanch, H.W.
2011. Techno-economic analysis of a lignocellulosic
ethanol biorefinery with ionic liquid pre-treatment.
Biofuels, Bioproducts and Biorefining, 5(5), pp.562–
569.
Kumar, R., Tabatabaei, M., Karimi, K., Horváth, I.S.
2016. Recent updates on lignocellulosic biomass
derived ethanol -A review. Biofuel Research Journal,
9(9), pp.347–356.
Lam, F.H., Ghaderi, A., Fink, G. R., Stephanopoulos, G.
2014. Engineering alcohol tolerance in yeast. Science,
346(6205), pp.71–5. Available at:
http://www.ncbi.nlm.nih.gov/pubmed/25278607
[Accessed March 28, 2017].
Lee, F. M., Pahl, R. H., 1985. Use of gasoline to extract
ethanol from aqueous solution for producing gasohol.
Industrial and Engineering Chemistry Process Design
and Development, 24(2), pp.250–255. Available at:
http://pubs.acs.org/doi/abs/10.1021/i200029a005
[Accessed November 30, 2017].
Leeper, S. A., Wankat, P. C., 1982. Gasohol production by
extraction of ethanol from water using gasoline as
solvent. Industrial and Engineering Chemistry
Process Design and Development, 21(2), pp.331–334.
Available at:
http://pubs.acs.org/doi/abs/10.1021/i200017a018
[Accessed November 30, 2017].
Li, Y. J., Lu, Y. Y., Zhang, Z. J., Mei, S., Tan, T. W., Fan
L. H. 2017. Co-fermentation of cellulose and
sucrose/xylose by engineered yeasts for bioethanol
production. Energy & Fuels,
p.acs.energyfuels.7b00032. Available at:
http://pubs.acs.org/doi/abs/10.1021/acs.energyfuels.7b
00032 [Accessed March 30, 2017].
Olofsson, J., Barta, Z., Börjesson, P. and Wallberg, O.
2017. Integrating enzyme fermentation in
lignocellulosic ethanol production: life-cycle
assessment and techno-economic analysis.
Biotechnology for Biofuels, 10(1), p.51. Available at:
http://biotechnologyforbiofuels.biomedcentral.com/art
icles/10.1186/s13068-017-0733-0.
Pertamina. 2017. Spesifikasi Pertamax, Available at:
http://www.pertamina.com/industrialfuel/media/24240
/pertamax.pdf [Accessed November 29, 2017].
Singh, N., Mathur, A.S., Tuli, D.K., Gupta, R.P., Barrow,
C.J., Puri, M. 2017. Cellulosic ethanol production via
consolidated bioprocessing by a novel thermophilic
anaerobic bacterium isolated from a Himalayan hot
spring. Biotechnology for Biofuels, 10(1), p.73.
Available at:
http://biotechnologyforbiofuels.biomedcentral.com/art
icles/10.1186/s13068-017-0756-6 [Accessed March
30, 2017].
U.S. EIA. 2016. International Energy Outlook 2016,
Available at: http://www.hm-
treasury.gov.uk/independent_reviews/stern_review_ec
onomics_climate_change/stern_review_report.cfm.
Vohra, M., Manwar, J., Manmode, R., Padgilwar, S. and
Patil, S. 2014. Bioethanol production: Feedstock and
current technologies. Journal of Environmental
Chemical Engineering, 2(1), pp.573–584.
Xu, Y. and Wang, D. 2017. Integrating starchy substrate
into cellulosic ethanol production to boost ethanol
titers and yields. Applied Energy, 195, pp.196–203.
Available at:
http://www.sciencedirect.com/science/article/pii/S030
6261917302593 [Accessed March 30, 2017].
Ziolkowska, J. R. 2014. Prospective technologies,
feedstocks and market innovations for ethanol and
biodiesel production in the US. Biotechnology
Reports, 4, pp.94–98.
Influence of Ions and Temperatures on Water-Ethanol-Gasoline Liquid-Liquid Equilibrium
103