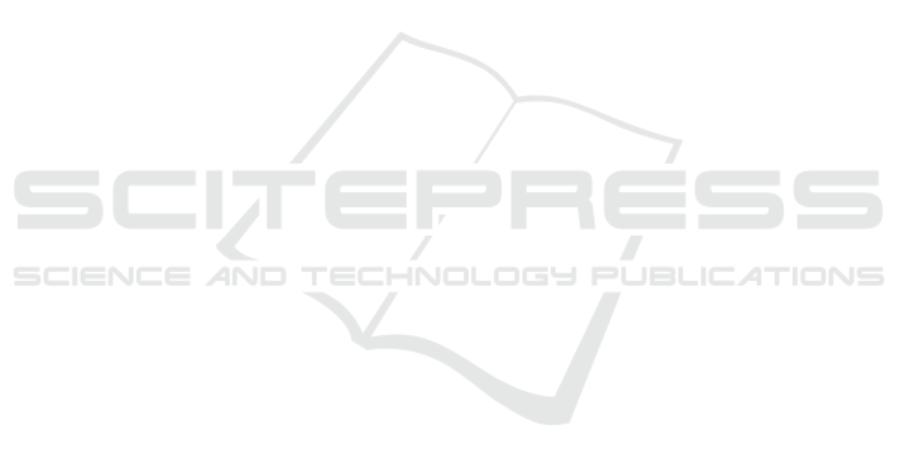
propeller produces a large thrust. The actual
application results are basically consistent with the
numerical simulation results, and the comparison
results are shown in Fig.17 and Fig.18. In summary,
the propeller has good hydrodynamic performance
and meets the needs.
5 CONCLUSIONS
According to the parameters of the reference (R. S.
Duelley, 2011), the propeller has not reached the
ideal efficiency value after the actual measurement.
In recent years, the research has not solved the
efficiency problem well. In this paper, the design
parameters are optimized based on the reference (R.
S. Duelley, 2011). The propeller produces a large
thrust while maintaining a high efficiency state.
Parametric modeling of propellers based on
OpenProp and SolidWorks, from theoretical analysis,
parameter research to data import and complete
three-dimensional modeling, saving a lot of time
spend on data calculation, making propeller design
and processing more convenient and faster. This test
verifies the reliability of this design method by
testing the actual application effect of the propeller
and comparing it with the theoretical design. The
test proves that the parametric modeling method by
using OpenProp are reliable. The results of the thrust
theoretical analysis are not much different from
those of the actual application.
This experiment tests the actual hydrodynamic
performance of the four propellers and draws the
following conclusions. Under the premise that other
parameters are consistent, the efficiency of the three-
bladed propeller is higher than the four-bladed
propeller. The efficiency of the narrow blade
propeller is higher than the wide blade propeller.
The efficiency of the small diameter propeller at
high rotating speed is greater than that at low
rotating speed. The efficiency of the large diameter
propeller at low rotating speed is greater than that at
high rotating speed. The change in back rake angle
has little effect on the hydrodynamic performance of
the propeller. For MAU type propeller tested in this
paper, the efficiency of correct installation and
reverse installation is very different. The correct
installation efficiency is much higher than the
reverse installation efficiency. However, the
efficiency of airfoil propeller correct or reverse
installation is not much different. And the
hydrodynamic performance in the reverse
installation is better than the MAU type propeller.
That is, the map propeller is suitable for single way
propulsion and the airfoil propeller is suitable for
double way propulsion.
ACKNOWLEDGEMENTS
This work was financially supported by the National
Key Research and Development Program of China
(Grant No. 2016YFC0301404) and the National
Natural Science Foundation of China (Grant No.
51379198).
REFERENCES
A. Bhattacharyya, V. Krasilnikov, S. Steen. A CFD-based
scaling approach for ducted propellers. Ocean
Engineering, 2016, 123, 116-130.
A. Dubois, Z. Q. Leong, H. D. Nguyen, J. R. Binns.
Uncertainty estimation of a CFD-methodology for the
performance analysis of a collective and cyclic pitch
propeller. Applied Ocean Research, 2019, 85, 73-87.
B. An, H. H. Zhu, S. D. Fan. Three-dimensional modeling
and performance analysis of an AU propeller. China
Ship Repair, 2017, 30(3), 48-52.
C. Y. Liu, K. Luo, Q. Guo. Performance prediction of
contra-rotating propellers for undersea vehicle.
Journal of Unmanned Undersea System, 2017, 25(5),
437-442.
D. Owen, Y. K. Demirel, E. Oguz, T. Tezdogan, A.
Incecik. Investigating the effect of biofouling on
propeller characteristics using CFD. Ocean
Engineering, 2018, 159, 505-516.
F. D. Gao, C. Y. Pan. Parameterized design and analysis
of the complicated curved-surface propeller in solid
modeling. Mechanical Science and Technology for
Aerospace Engineering, 2011, 30(1), 1-5.
H. P. Pei, R. Liu. Three-dimensional modeling and
hydrodynamic performance analysis of different pitch
angle propeller. Journal of Hangzhou Dianzi
University (Natural Sciences), 2018, 38(2), 78-83.
J. M. Wu, E. W. Zhang, L. Zhong. Thrust characteristics
of ducted propeller under the influence of cavitation.
Journal of South China University of Technology
(Natural Science Edition), 2018, 46(1), 41-49.
J. M. Wu, L. Zhong, E. W. Zhang. Simulation of
hydrodynamics of underwater robot in reverse
propeller and negative speed. Ship Engineering, 2017,
39(S1), 225-229,292.
J. M. Wu, Y. F. Lai, J. W. Li. Distribution characteristics
of thrust, advanced and induced velocity on ducted
propeller disk. Ship Engineering, 2016, 38(12), 23-26,
36.
L. Huang, L. Chen. Propeller modeling method and
open water performance study. Ship Electronic
Engineering, 2014, 34(8), 78-80.
M. M. Helal, T. M. Ahmed, A. A. Banawan, M. A. Kotb.
Numerical prediction of sheet cavitation on marine
Parametric Modeling and Hydrodynamic Analysis of Underwater High Performance Propeller
153