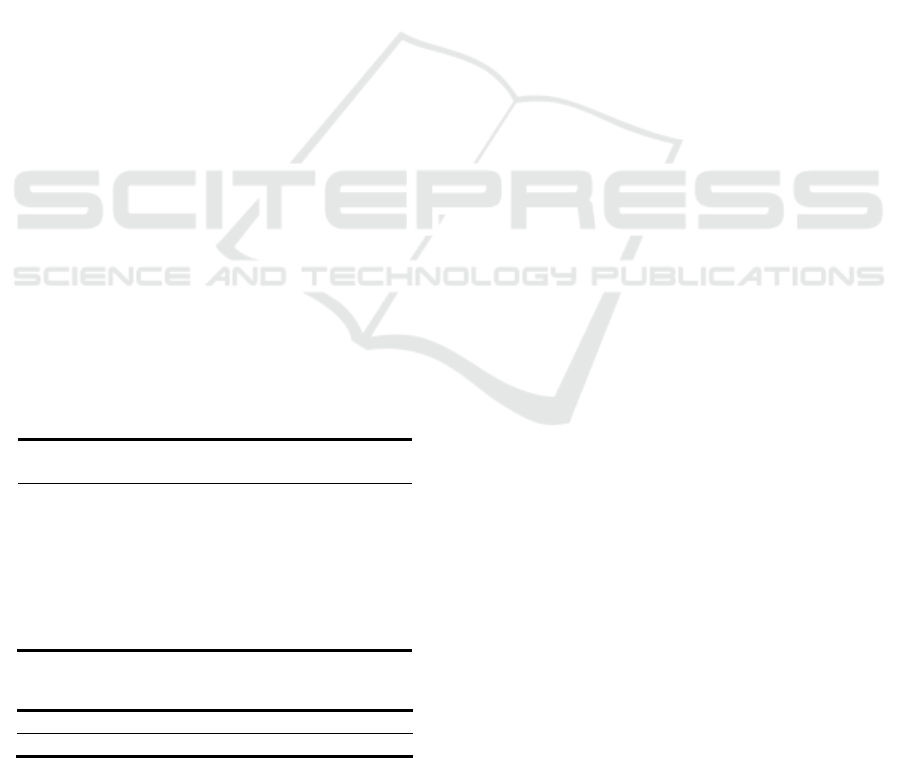
2.3 Red Rubber Reflow Soldering Step
Checking
The so-called reflow soldering is to melt the solder
paste (solder paste) so that the surface-assembled
components and PCB boards are firmly bonded
together (Qi cheng, 2011). The equipment used is a
reflow soldering furnace located behind the mounter
in the production line. For example, table 5 is the
reference temperature of common red adhesive
reflow welding process, and the reference
temperature of three kinds of solder paste commonly
used in the table is at different temperature zones.
Table 6 is the equipment parameters of the
manufacturer. The solder paste used is SN63PB37.
You can see, the equipment parameters and
reference parameters are consistent basically,
because considering the time cost, this will be a
thing or two, three or four low temperature region
merging, and slightly increased the welding
temperature, but these smaller factor changes will
not affect the process to produce waste, therefore
rule out the possibility that this process has a
problem.
In addition, it is necessary to consider whether
the quality of the patch is affecting the overall effect
of the photoelectric sensor. So first check the patch
model, found no error. After the replacement of the
normal pieces of the patch, the products are OK.
Then check whether the patch position of the fault
parts is correct, and find that there is no part beyond
the welding pad at both ends, so there is no problem
with the patch. Therefore, there is no problem with
the process.
Table 5. Three solder paste reflow soldering temperature
Settings at 8 temperature zone.
Table 6. Equipment parameters of manufacturers
2.4 Wave Crest Welding Procedure
Inspection
First consider whether the parameters for this
process are set correctly. First, consider preheating.
The tin furnace temperature of this process is kept at
250°C , which is consistent with the reference value.
Therefore, there is no problem with the process.
Then consider the transport speed (stripping speed).
Generally speaking, too fast stripping speed will
lead to PCB preheating not reaching the ideal
temperature, and too slow will lead to too high
temperature, which may damage PCB board.
Therefore, the speed is usually set at 1100mm-
1200mm, which is consistent with the
manufacturer's production parameters. Finally, the
quality of flux was considered. The flux model was
RF800, and the manufacturer was found to have the
production qualification, so there was no problem
with the model. However, it was observed that the
surface of the fault parts could help with flux
residue, and it was considered that poor contact of
the circuit was caused by flux residue. Therefore, the
surface of the fault parts was cleaned with washing
board water, and then assembled and tested. It was
found that the product could work normally, so we
considered that the intermittent failure of the
ambient light sensor was caused by the quality of
flux. In order to further confirm this idea, we applied
for trial production of 500 pieces of GOLF nh-4 flux
and put them into the refrigerator for moisture
regain. The final test results showed that no such
phenomenon occurred in all products. Therefore, it
can be concluded that the quality of flux causes
intermittent failure of ambient light sensor.
2.5 Wire Harness Welding Inspection
No broken skin or core leakage was found in the
wiring harness inspection. Therefore, the quality
problem of the two hardware is excluded. The
welding method is manual welding, and the
temperature is 350°C, which conforms to the
specified temperature.
Based on the above tests, it can be concluded that
the intermittent failure of ambient light sensor is
caused by short circuit due to poor flux quality. In
order to verify that the fundamental factor is the
quality of flux, make the following test again: clean
the flux residue of the failed parts with washing
board water, and then dry the test, and find that
100% of the failed parts can be used normally. Then
a control group was made again. Another part of the
defective parts were cleaned with plate washing
ICVMEE 2019 - 5th International Conference on Vehicle, Mechanical and Electrical Engineering
12