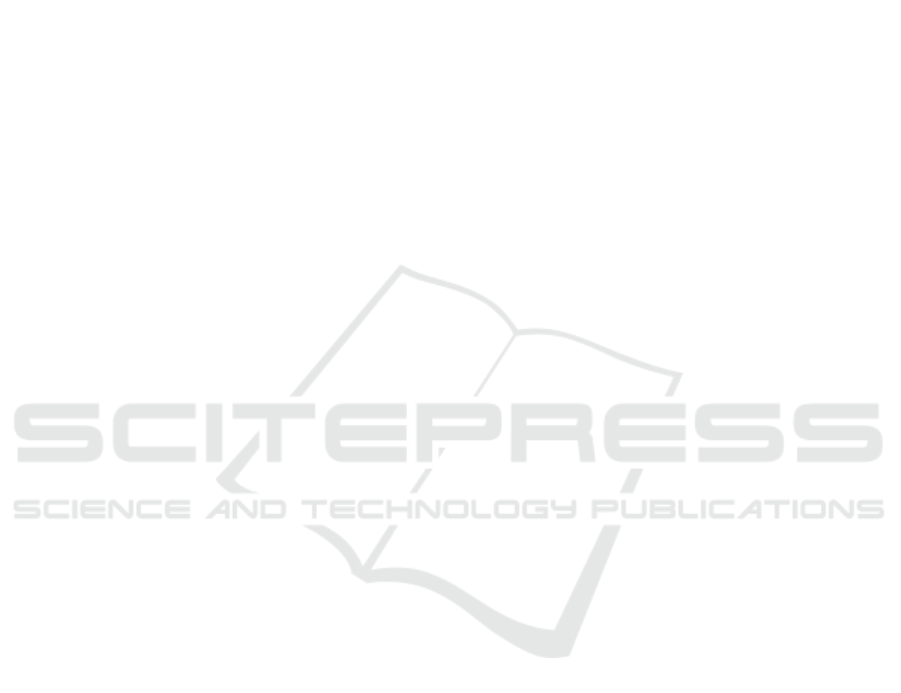
The Influence of the Level of the Flow Path Blockage at the Inlet on
the Fan Characteristics
Grigorii Popov, Oleg Baturin, Andrei Volkov, Daria Kolmakova, Vasilii Zubanov,
Anastasia Korneeva and Yulia Novikova
Samara National Research University, Samara, Russia
Keywords: Nonuniformity, Fan, Turbofan Engine, Low Pressure Spool.
Abstract: The paper presents the results of numerical simulation of the effect of flow nonuniformities at the engine inlet
on the working process of the engine fan. Flow nonuniformities is created by pushing the interceptor into the
flow part of inlet device like as it is often done during field tests. The authors have created a numerical model
capable of considering non-stationary processes in the fan using nonlinear harmonic analysis. As a result,
qualitative and quantitative estimates were obtained of the influence of overlapping of the inlet duct by the
interceptor on the main parameters of the fan workflow. It is shown that the more the duct is blocked, the
more its parameters are deteriorated. Moreover, the deterioration is not linear, but according to the dependence
of the 2nd order.
NOMENCLATURE
G mass flow rate of the working fluid, kg/s;
p* total pressure, Pa;
Т* total temperature, K;
n rotor speed, %;
m bypass ratio;
efficiency;
Y+ non-dimensional wall distance;
flow angle, degree;
LPC low pressure compressor;
RW rotor wheel;
GV guide vane;
NLH nonlinear harmonic analysis.
Note. The flow angles in this research are measured
from the aerofoil cascade front.
1 INTRODUCTION
Inlet devices of bypass turbofan engines (characterized
by a high degree of bypass ratio) of modern passenger
aircraft have a large flow area and are relatively short
(their length is less than the diameter). It would seem
that losses in such conditions should be minimal in all
typical flight conditions. However, in some cases (for
example, with a strong side wind, flying sideways, etc.)
a separation flow occurs at the inlet edge of the air
intake, which causes the flow at the fan inlet to become
uneven. This, in turn, causes a significant reduction in
the efficiency of the low-pressure compressor and the
engine. In addition, the inlet nonuniformity causes
oscillations of the fan blades, which can lead to their
destruction.
For a long time, the study of the influence of inlet
nonuniformity on the GTE workflow was carried out
during field tests with an aircraft air intake or its
simulator (Figure 1). The latter is a complex of
resistances (grids, plates, struts), located between the
lemniscate attachment and the engine, creating the
same uneven velocity field at the fan inlet, as the
aircraft air intake on the flight mode of interest
(Grigor'ev, 2009).
At present, in connection with the development of
numerical methods for modelling gas-dynamic
processes and strength calculations, it has become
possible to model the influence of the inlet
nonuniformity on the workflow of the fan and the
engine. This will allow an assessment of the influence
of nonuniformity at the stage of calculations, without
manufacturing many prototypes. As a result, at the
initial design stage, the design variants that do not
work satisfactorily under the specified conditions will
be eliminated, which will significantly reduce the
time and cost of engine development.
In this paper, the authors aim to test the possibility
Popov, G., Baturin, O., Volkov, A., Kolmakova, D., Zubanov, V., Korneeva, A. and Novikova, Y.
The Influence of the Level of the Flow Path Blockage at the Inlet on the Fan Characteristics.
DOI: 10.5220/0007836502470254
In Proceedings of the 9th International Conference on Simulation and Modeling Methodologies, Technologies and Applications (SIMULTECH 2019), pages 247-254
ISBN: 978-989-758-381-0
Copyright
c
2019 by SCITEPRESS – Science and Technology Publications, Lda. All rights reserved
247