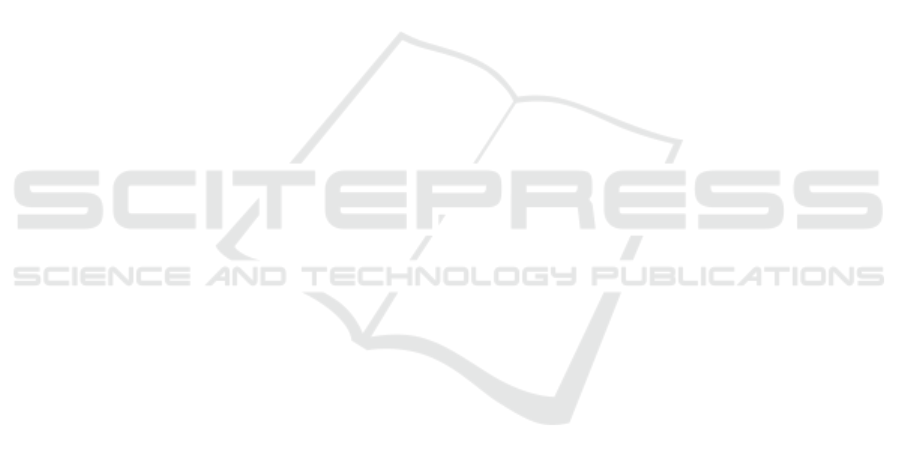
been classified based on ABC analysis. The budget
allocation for drug supplies is not too calculated, so
there is a lot of empty stock and then making
additional orders, which can actually increase the
cost for the company. The existence of a 'retail last
bite' program also sometimes causes the number of
orders to jump suddenly to suppliers and causes
excess stock and warehouse capacity to overload /
insufficient.
3.2 Solutions From Fishbone Analysis
There are several reasons of stockout in PT. XYZ.
Here are some solutions to help PT. XYZ for
improving their supply management.
3.2.1 Solution to System Problems
To overcome system problems, PT. XYZ can
upgrade the system so that it has a program as a
'reminder' of what stock is left, and when is the right
time to reorder. So the system does not only function
as a note taker and see what the final stock is, then it
is checked manually, but it can also be used as a
reminder of the remaining existing stock. The
electronic system will be able to solve the problem
of shortages and excess stock, and also the wrong
ordering process.
3.2.2 Solution to Process Problems
To reduce and resolve process problems, PT. XYZ
can supply contracts with suppliers, so there are
clear agreement terms and commitments that must
be fulfilled between PT. XYZ and suppliers. The
supply of the contract can determine the lead time
agreement that must be maintained, so that long lead
time problems can be prevented by ordering earlier.
With an earlier booking, the stock will arrive on
time and there will be no stockout and backordering.
Backordering can trigger customer disappointment
and potential loss of sales / sales.
Estimates of fewer stock requirements than
demand can be prevented by coordinating in
advance between warehouses, marketing, and
planning, so that better forecast results are obtained,
not just on intuition. Another method that can be
used is using the forecast method selection that is in
accordance with the pattern of PT. XYZ.
3.2.3 Solution to the Procedure Problem
Procedure problems are the main key
problem in management. The wrong initial
procedure will make the whole series not smooth,
and need to be resolved immediately. The procedure
where the goods must go through the central
distributor first, even though it should be closer if
from the factory directly to PT. XYZ should only be
done administratively, so that the achievement of
lead time is shorter and the cost estimation is lower,
because there does not have to be a factory cost to
the central distributor PT. XYZ first, then the
Distribution Center sends to PT. XYZ. Also, there is
no safety stock at PT. XYZ. So when the stock is out
of stock, then planner make an additional orders, so
in this study provides a design of inventory
management for the management of PT. XYZ for
optimal inventory.
3.2.4 Solution to Human Resource Problems
Human resource is the blood of business life
and it is very important to motivate and maintain it
so they are on the right track. To solve employee
problems, PT. XYZ can conduct comprehensive
training in the right way. Good comunication and
coordination between the marketing, warehouse, and
purchasing also need to be done to determine about
each other's responsibilities. Every time planner will
make a purchase plan there should be good
communication and coordination so that there is a
clear estimation of sales requirements in the amount
and how much stock is currently in the warehouse.
3.2.5 Solution to Product Problems and Prices
Based on information from informants, PT.
XYZ has never done inventory classification based
on ABC analysis. ABC analysis can be used to
classify which products are more important and have
a greater investment value so that they do not sit
quietly in a warehouse and make a high Days of
Inventory.
PT. XYZ also has many products that check it
manually, so that proper forecasting is needed so
that stockouts don't occur frequently. Better
forecasting means lower safety stocks and higher
levels of availability. It also means a reduced
exposure to excess and obsolete stock risk (a large
contributor to holding cost of stock).
3.2.6 Solution to Supplier Problems
PT. XYZ there should be a supply contract with the
supplier, so that there are clear agreements regarding
lead time, supplier response, and other agreements.
A close relationship with supplier is crucial. When
supplier lead times are reduced below the required
lead time, it’ll help remove the requirement to hold
Medicine and Consumer Goods Supply Management Design to Reduce Stockout and Days of Inventory in PT. XYZ
733