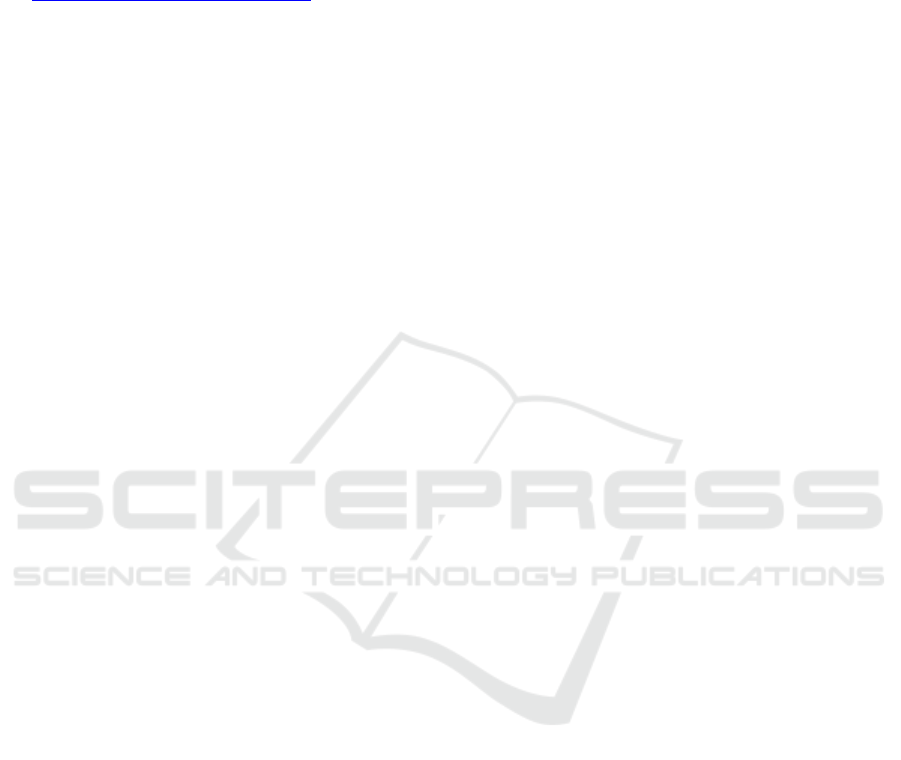
International Journal of Quality & Reliability
Management, 25(2), 173-200.
Boiral, O. (2003). ISO 9000, outside the iron cage.
Organization Science, 14(6), 720-737. !
ISO. (2014). ISO 9001 Survey. Retrieved from:
http://www.iso.org/iso/survey2012.pdf
Lin, C. I., & Jang, W. Y. (2008). Successful ISO 9000
implementation in Taiwan: How can we achieve it,
!and what does it mean?. International Journal of
Productivity and Performance Management, 57(8),
600- 622. !
Augustyn, M. M., & Pheby, J. D. (2000). ISO 9000 and
performance of small tourism enterprises: a focus !on
Westons Cider Company. Managing Service Quality,
10(6), 374-388. !
Cebeci, U., & Beskese, A. (2002). An approach to the
evaluation of quality performance of the companies
!in Turkey. Managerial Auditing Journal, 17(1/2), 92-
100. !
Dwyer, G. (2002). Business excellence versus ISO 9000 in
Irish context – which delivers? Managerial !Auditing
Journal, 17(4), 404-412. !
Heras, I., Casadeses, M., & Dick, G.M. (2002). ISO 9000
certification and the bottom line: a !comparative study
of the profitability of Basque region companies.
Managerial Auditing Journal, 17(1/2), 72-78. !
Arauz, R., & Suzuki, H. (2004). ISO 9000 performance in
Japanese industries. Total Quality !Management and
Business Excellence, 15(1), 3-33. !
Claver, E., & Molina, T. J. (2003). Critical factors and
results of quality management: an empirical !study.
Total Quality Management, 14, 91-118.
Gustafsson, R., Klefsjo, B., Berggren, E., & Granfors-
Wellemets, U. (2001). Experiences from
implementing ISO 9000 in small enterprises – a study
of Swedish organizations. The TQM Magazine, 13(4),
232-46.
Trust. (2016). Usaha Kecil Menengah dalam menerapkan
ISO 9001. Retrieved from: http://trustmandiri.com/iso-
9001-usaha-kecil-menengah-ukm/
Yuwono, B., Zakaria, F.R., & Panjaitan, N.K. (2012).
Faktor-faktor yang mempengaruhi penerapan cara
produksi yang baik dan standar prosedur operasi
sanitasi pengolahan fillet ikan di Jawa. Manajemen
IKM, 7(1), 10-19.
Nwankwo, S. (2000). Quality assurance in small business
organisations: myths and realities. International
Journal of Quality & Reliability Management, 17(1),
82-99.
Hudson, M., Smart, A., & Bourne, M. (2001). Theory and
practice in SME performance measurement system.
International Journal of Operations & Production
Management, 21(8), 1096-1115.
Garengo, P., Biazzo, S., & Bernardi, G. (2007). Design
and implementing a performance measurement system
in SMEs: a bottom up approach. International Annual
EurOMA Conference, 14(1).
Sekaran, U. (2006). Metode riset bisnis. Jakarta: Salemba
Empat.
DeVon, H. A., et al. (2007). Psychometric toolbox for
testing validity and reliability. Journal of Nursing
scholarship, 39(2), 155-164.
Kowsalya, D.N., et al. (2012). Development and
validation of a scale to assess self-concept in mild
intellectually disabled children. International J. Soc.
Sci. & Education, 2(4), 699-709.
Azwar, S. (2012). Reliabilitas and validity, 4.0 edition,
Pustaka Pelajar.
Napitupulu, D. (2015). Kajian Empiris Faktor Sukses
Implementasi e-Government Studi kasus: Pemerintah
Kota Bogor J. Sisfo, 5, 229-36.
Burns, N., & Grove, S. (1993). The practice of nursing
research: conduct, critique, and utilization (2nd ed).
W.B. Saunders: Philadelphia, Pennsylvania, USA.
Yaghmaie, F. (2003). Content validity and its estimation.
J. Med. Educ, 3, 25–27.
Yang, W. (2011). Applying content validity coefficient
and homogeneity reliability coefficient to investigate
the experiential marketing scale for leisure farms. J.
Global Business Management, 7.
Yu, N. (1993). The computation of content validity
coefficient and homogeneity reliability coefficient in
ordinal data. Psychological, 40, 199-214.
Lai, K., & Chang, M. (2007). The Application of aiken
content validity coefficient and homogeneity
reliability coefficient in enterprise business risks scale
for hot-spring hotel industries. Journal of Management
Practices and Principles, 1, 64-75.
Aiken, L. R. (1985). Three coefficients for analyzing the
reliability, and validity of ratings. Educational and
Psychological Measurement, 45, 131-142.
Aiken, L. R. (1980). Content Validity and Reliability of
Single Items or Questionnaires. Educational and
Psychological Measurement, 40, 55-59.
Cohen, J. (1960). A coefficient of agreement for nominal
scales. Educ. Psycol. Meas., 20, 37-46.
UNICEES 2018 - Unimed International Conference on Economics Education and Social Science
18