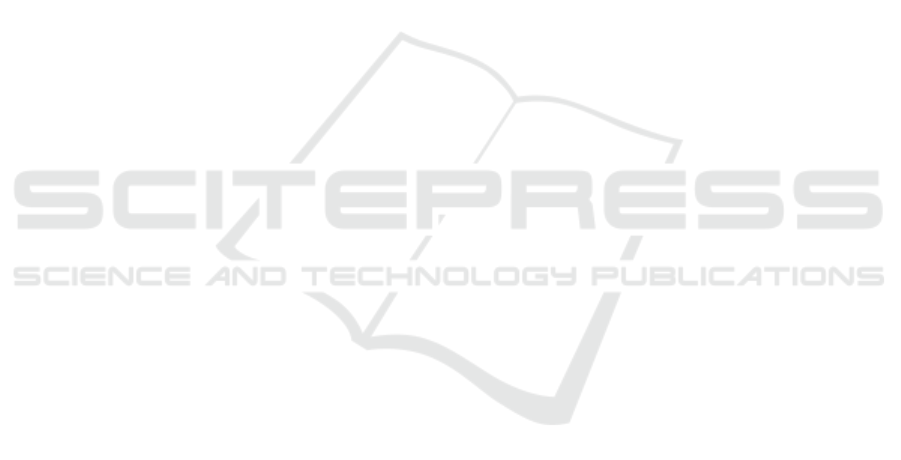
pp. 112.
Flight Dynamics and Automatic Flight Controls -
Jan Roskam-2686.
pp. 38.
Factors Affecting ISO 9001 Implementation in
International Review of Business and
Finance, 9(1), pp. 4144. Available at:
http://www.ripublication.com.
people with young-onset dementia: A meta-
Maturitas, 92, pp. 102109. doi:
10.1016/j.maturitas.2016.07.019.
Ismyrlis, V., Moschidis, O. and Tsiotras, G. (2015)
-
certified greek companies using multidimensional
International Journal of Quality and
Reliability Management, 32(2), pp. 114131. doi:
10.1108/IJQRM-07-2013-0117.
Factors to Motivate Small and Medium Enterprise
(SME) Construction Firms in the Philippines to
Procedia Engineering,
171, pp. 354361. doi:
10.1016/j.proeng.2017.01.344.
Kazili
Intelectual Economics,
2(8), pp. 3038.
Khanna, H. K., Sharma, D. D. and Laroiya, S. C. (2011)
implementation of total quality management in the
Asian Journal on Quality, 12(1), pp. 124138. doi:
10.1108/15982681111140598.
Lo, C. K. Y., Yeung, A. C. L. and Cheng, T. C. E. (2009)
evidence on inve
International Journal of Production Economics,
118(2), pp. 367374. doi:
10.1016/j.ijpe.2008.11.010.
-Organic
OrganizationsAn Axiomatic Theory: Authority
Based on Bureaucracy or Professi
International Journal of Scholarly Academic
Intellectual Diversity, 14(1), p. 7. Available at:
http://www.nationalforum.com/Electronic Journal
Volumes/Lunenburg, Fred C. Mechanistic &
Organic Organizations IJSAID V14 N1 2012.pdf.
Mardani, A. et al.
Multiple Criteria Decision-making Approach to
Procedia - Social and Behavioral
Sciences. Elsevier B.V., 172, pp. 786793. doi:
10.1109/BMAS.2005.1518180.
success factors towards the implementation of total
quality management in small medium enterprises: A
comparative study of franchise and manufacturing
Investment Management
and Financial Innovations, 12(3), pp. 163174. doi:
10.1007/s10956-007-9075-1.
successful implementation of ISO 9000 in small and
TQM Magazine, 9(2), pp.
135145. doi: 10.1108/09544789710165581.
Implementasi ISO 2008:9001 Serta Dampaknya
Jurnal
Dinamika Manajemen, 2(2), pp. 1725. doi:
http://dx.doi.org/10.1016/j.worlddev.2013.10.001.
-Government Maturity
Model Based on Systematic Review and Meta-
Jurnal Bina Praja, 8(2),
pp. 263275. doi: 10.21787/jbp.08.2016.263-275.
10th International QMOD Conference,
2007. Available at:
http://www.ep.liu.se/ecp/026/075/ecp0726075.pdf.
Poksinska, B., A.E. Eklund, J. and Dahlgaard, J. J. (2006)
IJQR, 23(5), pp. 490512. doi:
10.1108/02656710610664578.
state of ISO 9000 certification: A study of Swedish
TQM Magazine, 14(5), pp. 297306.
doi: 10.1108/09544780210439734.
Psomas, E.
ISO 9001 quality management system and its
influential critical factors in Greek manufacturing
International Journal of Production
Research, 53(7), pp. 20892099. doi:
10.1080/00207543.2014.965353.
Psomas, E. L., Fotopoulos, C. V. and Kafetzopoulos, D. P.
Managing
Service Quality, 20(5), pp. 440457. doi:
10.1108/09604521011073731.
arative study of TQM
practices and organizational performance of SMEs
International Journal of Quality and
Reliability Management, 18(1), pp. 3549. doi:
10.1108/02656710110364486.
orientation of SMEs, total quality management and
Journal of Manufacturing
Technology Management, 28(7), pp. 892912. doi:
10.1108/JMTM-04-2017-0064.
-synthesis of research on
Information
Research, 16(1). doi: http://InformationR.net/ir/...
system for small enterprises Zeszyty
Teoretyczne Rachunkowości, 93(0), pp. 00. doi:
Key Success Factors of ISO 9001 Implementation for Small Medium Enterprise: Systematic Literature Review
11