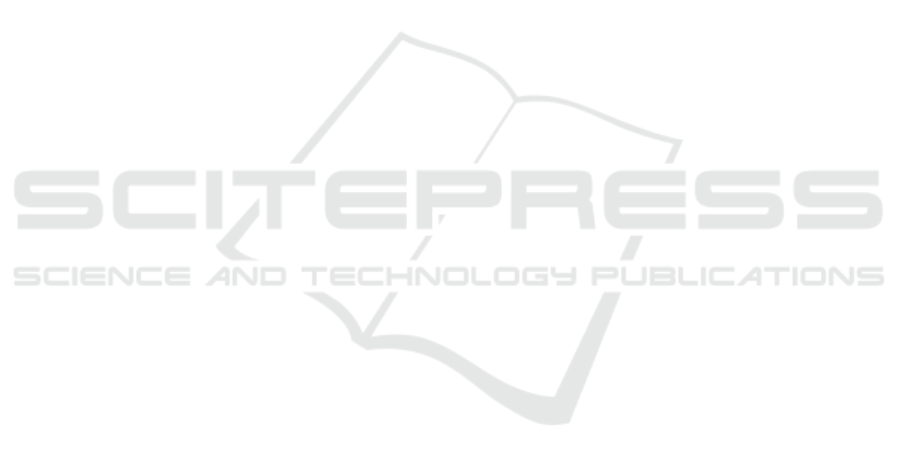
wing and with variations of winglet at angles of α =
0
◦
, 4
◦
, 8
◦
, 12
◦
, 19
◦
at Re = 2.3 × 10
4
. In general
these plots illustrate the development of the boundary
layer as the pressure slowly increases after peak suc-
tion from the leading-edge to the trailing-edge. Figure
10a shows at the plain wing (without winglet) that the
effective midspan better than tip span area. This can
be known that the resulting plot pressure coefficient
magnitude at midspan is wider than tip-span area at
all condition of angle of attack. This indicates that tip
vortex affecting characteristics air flow at the wingtip
area, while midspan area not affected because it was
longer distance from the wingtip.
Figures 10c and 10e are airfoil with adding rear-
ward wingtip fence cant angle 90
◦
, and forward
wingtip fence cant angle 90
◦
, respectively. It can
be seen that forward wingtip fence has a bigger
area pressure coefficient distribution than rearward
wingtip fence. This condition is caused by tip on
rearward wingtip fence model not completely cover
by the endplate. So, there is still an air spill from
lower side disrupts effective air flow on upper side
especially in the leading edge wingtip area. Conse-
quently, wing performance at rearward wingtip fence
types worse than forward wingtip fence ones.
3.5 Oil Flow Visualization Results
In Figures 11 and 12, it is describes the concept
boundary layer separation process, oil flow visualiza-
tion was applied to the upper surface of the airfoil at
angles of attack of 0
◦
, 4
◦
, 8
◦
, and 12
◦
. The dense
area of pigment describes the flow has decelerated, it
means the point at which the pressure gradient repeal
causing separation.
As the angle of attack increases the separation
point moves towards the leading edge at all four an-
gle of attack that the vorticity magnitude of the vortex
will increase as the angle of attack increases. At an-
gle of attack 0
◦
(Fig. 11a) this occurs at 10% chord,
4
◦
(Figure 12d) at 8% chord, 8
◦
(Figure 13a) at 3%
chord and for 12
◦
(Figure 12d) at 1% chord. Further-
more, the separation point (X
s
) vs x/c obtained from
the results of the oil-flow visualization and pressure
coefficient experiments can be seen in Table 1. It
also seen tip vortex get in interference at upper side
wingtip has an impact to coefficient of lift. The higher
the angle of attack the vortex is formed the wider. As
the vortex formation area increase the lift coefficient
will be decrease. In Fig. 12 shows vortex formation
of the tip where plain wing produces widest vortex
contour.
The forward wingtip fence produces smallest vor-
tex contour than other types. It was occurs due to
the vortex formation of the tip is obstructed by the tip
of the winglet. Therefore, design endplate cover tip
from front until rear of the tip causes tendency of air-
flow from the lower surface near the end of the wing
to ”jump” to the upper surface can be effectively re-
duced. As the disruption of airflow from lower sur-
face decrease the vortex formation area will decrease.
It follow the rising of lift coefficient.
4 CONCLUSIONS
The results of this experimental investigation show
that the use of winglet can improve the performance
on airfoils Eppler 562 using variations of wingtip
fence will increase drag along with increasing angle
of attack. However, with the addition of winglet, lift
force can be improved better than plain wing. Winglet
causes the formation of vortex tip can be reduced sig-
nificantly.
From the experimental study it was concluded that
the use of winglet can produce some flow characteris-
tics, namely:
• Increased angle of attack will increase wingtip
vortices and drag coefficient.
• Wing with the addition of forward wingtip fence
cant angel 90
◦
produces C
L
/C
D
higher than plain
wing and rearward wingtip fence cant angel 90
◦
.
• To produce a high C
L
/C
D
then the pressure re-
quired on the lower surface is much higher than
the upper surface. Forward wingtip fence cant
angel 90
◦
produces better C
L
/C
D
than rearward
wingtip fence cant angel 90
◦
because forward
wingtip fence enlarges the formation of effective
area so that the lift can be increased. It is gen-
erally found that the addition of forward wingtip
fence reduces the induced drag than plain wing.
• On forward wingtip fence cant angel 90
◦
produce
higher performance than other wing start at α
= 6
◦
while rearward wingtip fence cant angel
90
◦
produce better performance start at α = 8
◦
.
• In the oil-flow visualization and pressure distribu-
tion experiments, it was concluded that as the an-
gle of attack increased the separation point moves
towards the leading edge at wing airfoil Eppler
562 without and with winglet.
• Forward wingtip fence cant angle produce small-
est vortex formation area at tip than other types
that performed by oil-flow visualization.
SENTA 2018 - The 3rd International Conference on Marine Technology
212