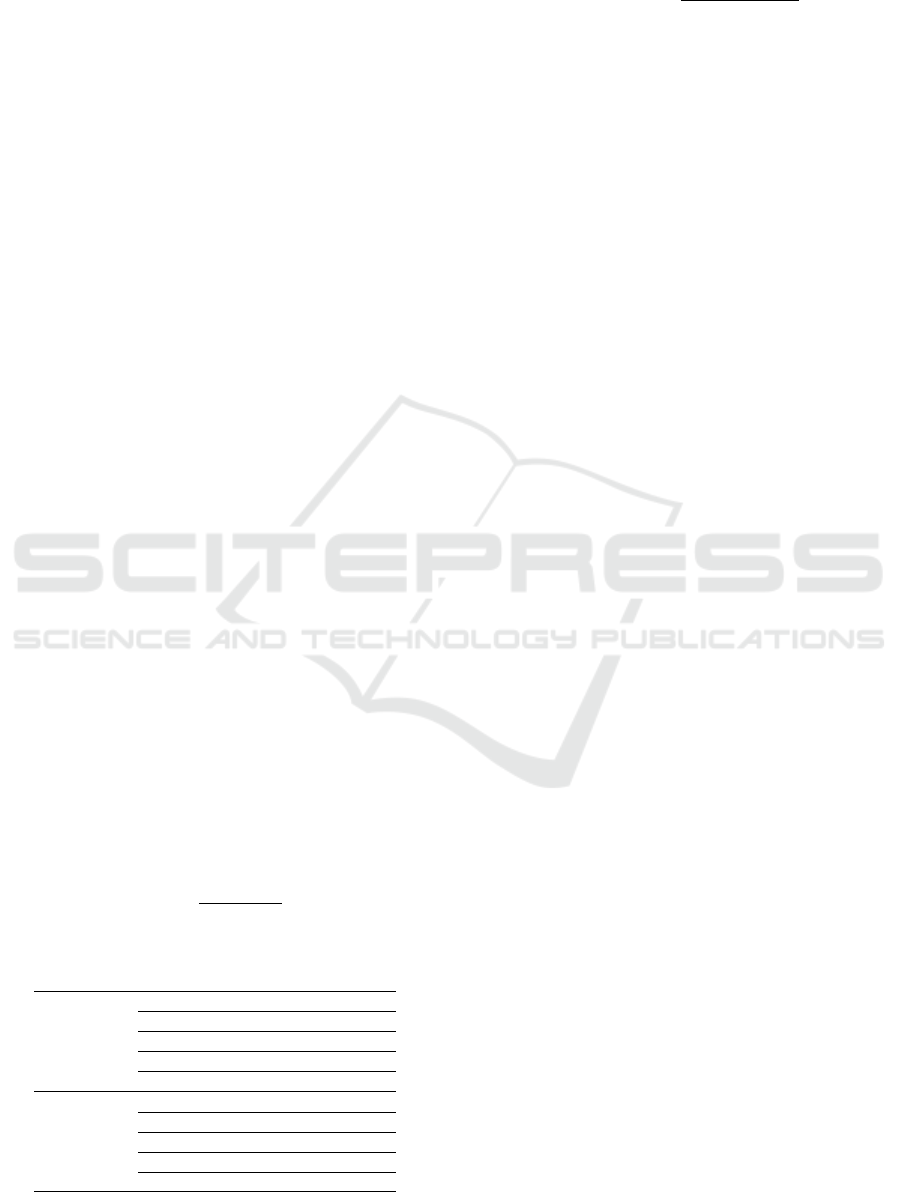
temperature at the addition of air temperature 200
◦
C
at 1004
◦
C in the oxidation zone (924
◦
C experimen-
tally).
2 BACKGROUND
2.1 Basic Gasification Theory
Biomass is a mixture of complex organic matter, such
as carbohydrates, fats, and proteins, which includes
a small amount of minerals, such as sodium, phos-
phorus, and iron (Basu, 2013). The characteristics
of biomass can be known by doing several analyzes,
namely ultimate and proximate analysis, density anal-
ysis, humidity analysis, and heat value analysis. The
proximate and ultimate MSW test results are shown
in Table 1.
The gasification process occurs in four stages,
namely drying (T ¡150
◦
C), pyrolysis / devolatilization
(150
◦
C ¡T ¡700
◦
C), reduction (800 ¡T ¡1000
◦
C), and
oxidation (700
◦
C ¡T ¡1500
◦
C). The gasification pro-
cess consists of a flammable gas, H
2
, CO, CO
2
; non-
flammable gas, namely N
2
and CH
4
, as well as other
compounds, such as sulfur, alkali and tar. Product gas
quality can be viewed from several aspects, namely
gas composition, LHV gas, cold gas efficiency, and
tar content. The composition of gas CO, H
2
, CH
4
is
seen from the results of testing using Gas Crematog-
raphy. The LHV value is calculated by:
LHV
syngas
=
n
∑
i=1
(Yi · LHVi) (1)
Cold Gas Efficiency is the amount of energy that
enters as long as potential energy exits. If M
f
is the
mass of solid fuel processed in the gasifier (kg) to pro-
duce M
g
mass of product gas with a LHV value from
Q
g
, then this efficiency can be stated as follows:
η
cg
=
LHV
g
· M
g
LHV
f
· M
f
(2)
Table 1: Proximate and Ultimate Data of MSW
PROXIMAT
Moisture Content % wt 9,82
Fixed carbon % wt 9,69
Volatile matter % wt 65,78
Ash % wt 14,71
HHV kJ/kg 13843
ULTIMAT
C % wt 39,83
H % wt 6,7
O % wt 38,11
N % wt 0,35
S % wt 0,14
The tar content is calculated using the following equa-
tion:
tar content =
m
tar
syngas volume
(3)
where m
tar
= mass of tar (kg) and volume of syn gas
(m
3
)
Based on its fluidization mode, gasifier is divided
into 3 types, namely: fixed bed gasifier, fluidized bed
gasifier, and entrained flow gasifier. In general, small-
scale gasification uses a fixed bed gasifier (Reed et al.,
1988). Based on the direction of feedstock and gas
flow in the gasifier, fixed bed gasifier can be cate-
gorized into three types, namely, updraft, downdraft,
and cross draft (Gai and Dong, 2012). In the updraft
gasifier, the direction of feedstock flow down while
the direction of gas flow up. In the downdraft gasi-
fier, the direction of the gas and feedstock flow are
both downward. Whereas in the cross draft gasifier,
the direction of gas flow is kept flowing horizontally
with feedstock flow down. Downdraft type gasifiers
have advantages including, suitable to be applied on a
small scale ((Sheth and Babu, 2009; Vyarawalla et al.,
1984)), construction and operation are easy, and pro-
duce low tar.
Tar is classified into three, namely secondary and
tertiary primary tar. Primary tar is formed at pyroly-
sis temperature. Secondary tar is formed at oxidation
temperature (above 500
◦
C) due to oxidants (oxygen,
air or steam). Tertiary tar is formed at a reduction
temperature (more than 800
◦
C). In gasification with
multilevel air input, the addition of air in the pyrol-
ysis zone can increase the temperature in the pyroly-
sis zone itself (auto-thermal) and subsequent zones so
that it is expected to increase the composition of the
gas. The composition of gas products obtained in the
oxidative pyrolysis process is more because it reacts
with O
2
and in the oxidative process of pyrolysis pro-
duces N
2
. In the composition of tar, pyrolysis usually
produces primary tar, whereas in oxidative pyrolysis
it has succeeded in reducing primary tar, and only be-
gins the formation of secondary tar.
2.2 Basic Theory of Numerical Model
Ahmed et al. (2012) classify biomass gasification
modeling into two broad categories, namely mathe-
matical models and simulation models. Mathematical
models include Equilibrium Models, Kinetic Model-
ing, and ANNs Models, while the simulation mod-
els include CFD Models and ASPEN Plus Models.
Computational Fluid Dynamics (CFD) involves mass
conservation equations, momentum, energy flow, hy-
drodynamics, and turbulence in the specified area.
In general, there are three stages that must be done
in CFD simulations according to Tuakia (Tuakia,
SENTA 2018 - The 3rd International Conference on Marine Technology
202