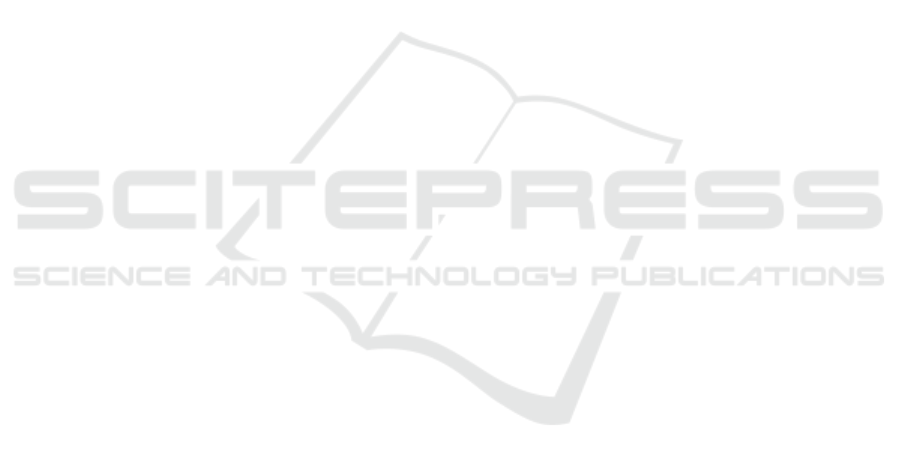
4 CONCLUSIONS
Computational Fluid Dynamics approach to estimate
the drag reduction by air lubrication using Winged Air
Induction Pipe (WAIP) is performed in the present
study and reasonably validated with experimental
works. By using nine configurations to achieve the
effect of hydrofoil clearance towards the drag reduc-
tion it is concluded that: the magnitude of drag reduc-
tion can be achieved when the contributing parameter
which are the angle of attack and hydrofoil clearance
chose at their optimum range. The optimum range
is achieved by modification of the parameter using
trial and error method. The modification of hydro-
foil clearance of the WAIP does not give a data trend
to a certain way. The application of WAIP gives result
of net drag reduction up to 10%. Figure 10 shows the
value of the drag reduction for each configuration of
the model. The clearance of the hydrofoil gives a sig-
nificant influence for the drag reduction. However, the
value of the drag reduction has no particular tendency
towards certain point. Therefore, the appropriate de-
sign is obtained by using trial and error method. This
is due to the unique flow characteristic produce by the
hydrofoil interacts with the plate in part C in different
ways depend on the clearance between hydrofoil
ACKNOWLEDGEMENTS
Authors are thanks to Department of Mechanical En-
gineering, Faculty of Engineering, Universitas In-
donesia for making facility available and also grant
PITTA No. 2561/UN2.R3.1/HKP05.00/2018
REFERENCES
Cui, Z., Fan, J. M., and Park, A. H. (2003). Drag coeffi-
cients for a settling sphere with microbubble drag reduc-
tion effects. Powder Technology, pages 132–134.
Duncan, J. H. (1981). An Experimental Investigation of
Breaking Waves Produced by a Towed Hydrofoil. Pro-
ceedings of the Royal Society of London. Series A, Math-
ematical and Physical Sciences, 377(1770):331–348.
Evans, G. M., Jameson, G. J., and Atkinson, B. W. (1992).
Prediction of the bubble size generated by a plunging liq-
uid jet bubble column. Chemical Engineering Science,
47:3265–3272.
Kodama, Y., Kakugawa, A., Takahashi, T., and Kawashima,
H. (2000). Experimental study on microbubbles and their
applicability to ships for skin friction reduction. In In-
ternational Journal of Heat and Fluid Flow, pages 582–
588.
Kumagai, I., Kushida, T., Oyabu, K., Tasaka, Y., and Murai,
Y. (2011). FLOW BEHAVIOR AROUND A HYDRO-
FOIL CLOSE TO A FREE SURFACE. Vis Mech Proc
Visualization of Mechanical Processes, 1(4).
Kumagai, I., Nakamura, N., Murai, Y., Tasaka, Y., Takeda,
Y., and Takahashi, Y. (2010). A New Power-saving De-
vice for Air Bubble Generation: Hydrofoil Air Pump for
Ship Drag Reduction. Proceedings of International Con-
ference on Ship Drag Reduction (SMOOTH-SHIPS).
Kumagai, I., Takahashi, Y., and Murai, Y. (2015). Power-
saving device for air bubble generation using a hydrofoil
to reduce ship drag: Theory, experiments, and applica-
tion to ships. Ocean Engineering, 95:183–195.
Menter, F. R. (1994). Two-equation eddy-viscosity turbu-
lence models for engineering applications. AIAA Jour-
nal, 32:1598–1605.
Mittnik, S., Rachev, S. T., and Samorodnitsky, G. (2001).
The distribution of test statistics for outlier detection
in heavy-tailed samples. Mathematical and Computer
Modelling, 34:1171–1183.
Mohanarangam, K., Cheung, S. C., Tu, J. Y., and Chen,
L. (2009). Numerical simulation of micro-bubble drag
reduction using population balance model. Ocean Engi-
neering, 36:863–872.
Muratoglu, A. and Yuce, M. I. (2015). Performance Anal-
ysis of Hydrokinetic Turbine Blade Sections. Technical
report.
Muste, M., Yu, K., Fujita, I., and Ettema, R. (2009). Two-
phase flow insights into open-channel flows with sus-
pended particles of different densities. Environmental
Fluid Mechanics, pages 161–186.
Ockfen, A. E. and Matveev, K. I. (2009). Aerodynamic
characteristics of NACA 4412 airfoil section with flap in
extreme ground effect. International Journal of Naval
Architecture and Ocean Engineering, 1:1–12.
Pang, M. J., Wei, J. J., and Yu, B. (2014). Numerical study
on modulation of microbubbles on turbulence frictional
drag in a horizontal channel. Ocean Engineering, 81:58–
68.
Shereena, S. G., Vengadesan, S., Idichandyxs, V. G., and
Bhattacharyya, S. K. (2013). CFD study of drag reduc-
tion in axisymmetric underwater vehicles using air jets.
Engineering Applications of Computational Fluid Me-
chanics, 7:193–209.
Toffoli, A., Babanin, A., Onorato, M., and Waseda, T.
(2010). Maximum steepness of oceanic waves: field
and laboratory experiments. Geophysics Research Let-
ters, 37.
Wang, H. and Zhai, Z. J. (2012). Analyzing grid indepen-
dency and numerical viscosity of computational fluid dy-
namics for indoor environment applications. Building
and Environment, 52:107–118.
Yanuar, Gunawan, Sunaryo, and Jamaluddin, A. (2012).
Micro-bubble drag reduction on a high speed vessel
model. Journal of Marine Science and Application,
11:301–304.
Numerical Study on Influence of Hydrofoil Clearance towards Total Drag Reduction on Winged Air Induction Pipe for Air Lubrication
169