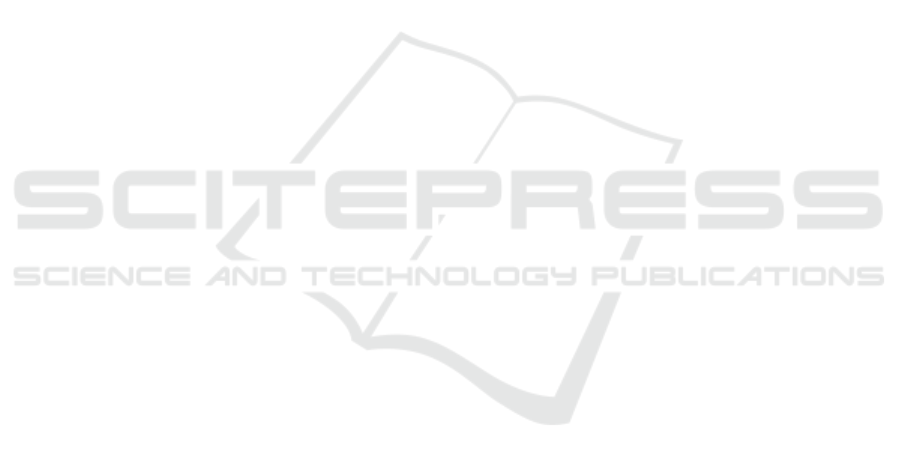
4 CONCLUSIONS
Sandwich plate has advantages and potential
applications to replace conventional steel stiffened
plate on ships structure. To ensure the structure’s
health and prevent sudden structural failure, it is
important to develop a damage identification method
for sandwich ships structure. In this research,
laboratory testing on sandwich plate was conducted
before testing on larger ship structures could be
performed
The experiment results showed that damage
caused decrease in the natural frequency of sandwich
with core made from 10% and 15% rice husk powder
by 0.39% and 5.39% respectively. The damping ratio
was changed due to damage; there were 0.16% and
0.13% changes observed for sandwich having core
made form 10% and 15% rice husk powder
respectively. Therefore, natural frequency and
damping ratio can be used as damage identification
parameters.
Sensitivity analysis in the size of damage needs to
be performed. In addition, better FEM model is
needed so the model can simulate damage in the core
and response of sandwich plate due to damage. The
identification of the damage location will be the main
concern for the next step of our research.
ACKNOWLEDGMENTS
This research was funded by Directorate of Research
and Community Services, Ministry of Research,
Technology and Higher Education, Republic of
Indonesia through PUPTN research scheme. Abdi
Ismail, the first author, gratefully thanks for the
support given by the Ministry through The Master’s
Degree Program Leading to Doctoral Degree for
Excellent Bachelor Graduates (PMDSU) fund.
REFERENCES
Abdo, M. A. B. & Hori, M., 2002. A Numerical Study of
Structural Damage Detection Using Changes in the
Rotation of Mode Shapes. Journal of Sound and
Vibration, Volume 2, no. 251, p. 227–239.
Al-Waily, M., 2013. Experimental and Numerical
Vibration Study of Woven Reinforcement Composite
Laminated Plate with Delamination Effect.
International Journal of Mechanical Engineering,
Volume 2, no. 5, pp. 1-18.
Borsellino, C., Calabrese, L. & Valenza, A., 2004.
Experimental and Numerical Evaluation of Sandwich
Composite Structures. Composites Science and
Technology, Volume 64 No. 64, pp. 1709-1715.
Cao, M. S., Sha, G. G., Gao, Y. F. & Ostachowic, W., 2017.
Structural Damage Identification Using Damping: a
Compendium of Uses and Features. Smart Materials
and Structures, Volume 26, no. 043001.
Chinchalkar, S., 2001. Determination of Crack Location in
Beams Using Natural Frequencies. Journal of Sound
and Vibration, Volume 247, no. 3, p. 417–429.
Dai, X. X. & Liew, J. Y. R., 2006. Steel-Concrete-Steel
Sandwich System for Ship Hull Construction. s.l.,
International Colloquium on Stability and Ductility of
Steel Structures, pp. 877-884.
Fan, W. & Qiao, P., 2011. Vibration-based Damage
Identification Methods: A Review and Comparative
Study. Structural Health Monitoring, Volume 10, no
83.
Gawronski, W. & Sawicki, J. T., 2000. Structural Damage
Detection using Modal Norms. Journal of Sound and
Vibration, Volume 229, no. 1, p. 194–198.
He, J. & Fu, Z. F., 2001. Modal Analysis. Butterworth
Heinemann. Great Britain.
Huang, X., Dyke, S., Sun, Z. & Xu , Z., 2016. Simultaneous
Identification of Stiffness, Mass, and Damping Using
an On‐line Model Updating Approach. Structural
Control Health Monitoring, Volume 24, no. 4.
Kawiecki, G., 2001. Modal Damping Measurement for
Damage Detection. Smart Materials and Structures,
Volume 10, no. 3, p. 466–471.
Kyriazoglou, C., Le Page, B. H. & Guild, F. J., 2004.
Vibration Damping for Crack Detection in Composite
Laminates. Composites Part A—Applied Science and
Manufacturing, Volume 35, p. 945–953.
Liang, R. Y., Choy, F. K. & Hu, J., 1991. Detection of
Cracks in Beam Structures Using Measurements of
Natural Frequencies. Engineering and Applied
Mathematics, Volume 328, p. 505–518.
Liew, J. Y. R. & Sohel, K. M. A., 2009. Lightweght steel-
Concrete-Steel Sandwich System with J-hook
Connectors. Engineering Structures, Volume 31, pp.
1166-1178.
Momčilović, N. & Motok, M., 2009. Estimation of Ship
Lightweight Reduction by Means of Application of
Sandwich Plate System. FME Transactions, Volume
37, pp. 123-128.
Panteliou, S. D., Chondros, T. G., Argyrakis, V. C. &
Dimarogonas, A. D., 2001. Damping Factor as an
Indicator of Crack Severity. Journal of Sound and
Vibration, Volume 241, p. 235–245.
Ramakrishnan, K. V. & Kumar, P. G. S., 2016.
Applications of Sandwich Plate System for Ship
Structures. Journal of Mechanical and Civil
Engineering, pp. 83-90.
Reis, E. M. & Rizkalla, S. H., 2008. Material
Characteristics of 3-D FRP Sandwich Panels. Journal
of Construction and Building Materials, Volume 22, p.
1009–1018.
Sampaio, R. P. C., Maia, N. M. M. & Silva, J. M. M., 2003.
The Frequency Domain Assurance Criterion as a Tool
Damage Identification of the Sandwich Plate Having Core from Rice Husk-Epoxy for Ship Deck Structure
117