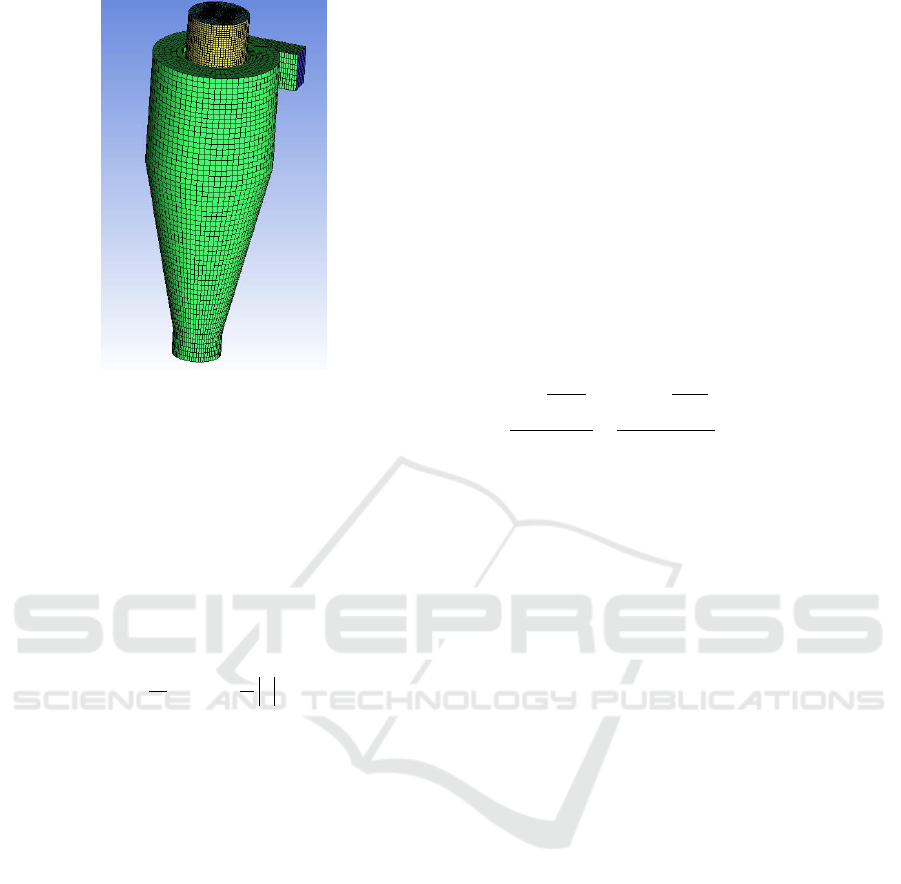
Figure 3: The hexahedral structured grid.
(1) The filter cartridge has much geometric
porosity, making meshing difficult to achieve. Thus,
the geometrical pores are simplified during
geometric meshing, and the filter cartridge is
considered a cylinder. The cylindrical region is set to
a porous medium fluid domain with a resistance
source during fluid analysis(Hu et al., 2017).
Generally, a velocity-dependent momentum is
provided in the porous region; the expression of this
momentum is as follows:
In the expression,
is the permeability; C2 is
the inertia drag coefficient. The first term on the
right side is the viscous loss term, and the second
term is the inertia loss term.
(2) When establishing the combination model,
the influence of the partial cleaning device above the
filter cartridge is not considered and is omitted
during meshing. The final structured hexahedral
mesh of the model is shown in Figure 3.
4 SIMULATION OF THE MODEL
IN FLUENT
4.1 The Model Calculation Method
Because hazardous materials rescue trucks use
vacuum negative pressure to collect hazardous
materials particles and the collection is two-phase
flow with a particle volume fraction less than ten
percent, in the FLUENT simulation analysis, the
continuous phase flow of the gas is simulated and
then the Lagrangian trajectory method is used to
track the particle trajectory(Hoffmann et al., 2002).
The flow in the cyclone and filter separator is a
complex two-phase flow with three-dimensional
strong rotational turbulence. According to the strong
rotating turbulent flow field of the cyclone and the
porous medium model of the filter cartridge, the
following can be concluded:
(1) The turbulence model selected is the
Reynolds stress model(RSM). It is suitable for high
rotational flow. The Reynolds stress model takes
into account the rapid changes in streamline bending,
vortex, rotation and tension. The Reynolds stress
model has a higher accuracy prediction potential for
complex flows. The transport equations(Zhou, 2001)
for the components of the Reynolds stress are as
follows:
jiji
k
jikji
PD
x
uuu
t
u
,,
''''
userjijijiji
SFBMG
,,,,
In the expression, Di,j is diffusion term, Pi,j is
stress generation term, Gi,j is buoyancy generation
term, Mi,j is pressure strain redistribution term, Bi,j
is discrete term, Fi,j is rotation system generation
term.
(2) For pressure and speed coupling, the
SIMPLE format is selected. Because PISO better
computes the non-steady state situation(Song,2011)
and COUPLED does not apply to porous media,
according to the complexity of the combined model,
the SIMPLE format is chosen for calculation.
(3) Pressure interpolation is based on the
PRESTO format. Because PRESTO is well suited
for high-speed rotary flow and porous media models,
it can better reflect the combined internal flow field
flow.
4.2 Simulation Results
The grid divided in the ICEM software is imported
into the FLUENT software for performing the
simulations used to analyze the problems involving
the new cyclone filter separator. The simulation
results are shown in Figure 4 to Figure 6.
Analysis of the Combined Cyclone and Filter Cartridge Separator for a Hazardous Materials Rescue Truck
239