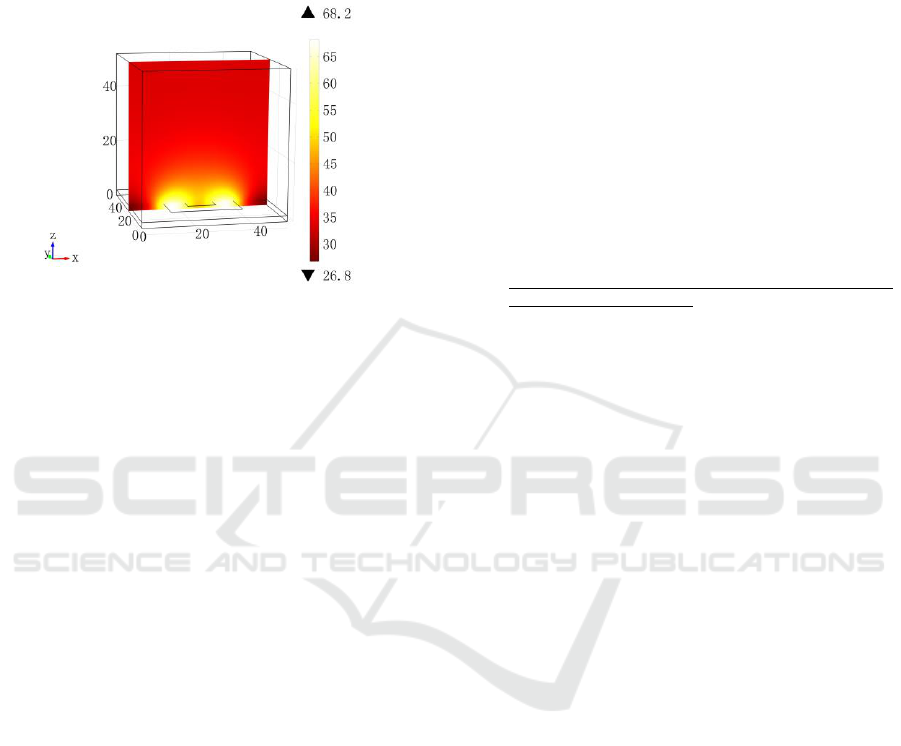
The temperature distribution on the middle cut
plane of the simulation when ε
r
=4.2 is shown in
Figure 5. The maximum temperature is 68.2℃,
48.2℃ higher than the ambient temperature due to a
microwave power density of 400W/m
2
and heating
duration of 300s.
Figure 5: Temperature(deg) distribution on x-z cutting
section of the MA unit model (simulation duration: 300s).
This simulation is preliminary for only FR-4 is
taken into consideration in the calculation. But the
power conversion and heating figure are presented.
The overall efficiency is low in current simulation
and further investigation on improving absorbing
rate will be carried out to improve the overall EM-
thermal conversion efficiency.
4 CONCLUSIONS
In this paper, we present the idea of the wind turbine
blades de-icing with MA under microwave heating.
The design of electromagnetic absorbing property of
MA is presented. Multi-physical simulation is
carried out to analyse the heat generation, thermal
distribution and temperature rise of the MA under
microwave heating. The energy conversion
efficiency is given based on the multi physical
simulation. This preliminary simulation show that
MA is possible to be used in microwave de-icing of
wind turbine blades as a wire-less, rapid and flexible
means.
ACKNOWLEDGEMENTS
The author wants to express his gratitude to Dr. Prof.
Jelonnek for his valuable suggestions.
This work is supported partially by the National
Natural Science Foundation of China [Grant number
51706242]; and partially by Natural Science
Foundation of National University of Defense
Technology [Grant number ZK16-03-05].
REFERENCES
Ansoft Inc, 2009. HFSS online Help,Version 12.
Battistil, BrighentiA., DalSavio, S. DellAnna. 2005. Evaluation of
anti-icing energy and power require- ment for wind turbine
rotors in cold climates. BOREAS, VII, FMI, Saariselka,
Findland, p13.
Comsol Multiphysics uers’s guide. 2012. Version.4.3.
Feher, L., Seitz, T. and Nuss, V., 2009. Microwave De-/Anti-
Icing Using the Midas-Technology. Journal of Microwave
Power & Electromagnetic Energy ONLINE. Vol. 43, No. 1.
Hochart, C., Fortin, G., Perron, J. et al., 2010. Wind turbine
performance under icing conditions[J]. Wind Energy,
11(4):319-333.
http://windren.se/WW2015/WW2015_12_311_Karthauser_
ReTurn._Deicing_Micro.pdf
Johansson, K. et al., 2015. Deicing of Wind Turbines using
Microwave Technology.
Landy, N. I., Sajuyigbe, S., Mock, J. J., Smith, D. R. and Padilla,
W. J., 2008. Perfect Metamaterial Absorber. Physics
Review Letter, 100(207402).
Mu, S., Wu, R., Chen, C., Yan, S. Y., 2014. RESEARCH ON
THE THERMAL HEATING DE-ICING PROPERTIES OF
WIND TURBINE BLADE COMPOSITE PLATES BASED
ON POLYMER ELECTRIC HEATING FILM. Fiber
Reinforced Plastics/Composites (FRP/CM).(in Chinese)
Pang, Y., 2013. The Theory and Design of Metamaterial
Absorbers. Changsha: National University of Defense
Technology.
Parent, O., Ilinca, A., 2011. Anti-icing and de-icing techniques for
wind turbines: Critical review. Cold Regions Science and
Technology 65 88–96.
Pitchai, K., 2011a. Electromagnetic and Heat Transfer Modeling
of Microwave Heating in Domestic Ovens. University of
Nebraska at Lincoln. P30.
Pitchai, K., 2011b. Electromagnetic and Heat Transfer Modeling
of Microwave Heating in Domestic Ovens. University of
Nebraska at Lincoln. P13.
Seifert, H., Westerhellweg, A., Kröning, J., 2003. Risk Analysis
of Ice Throw from Wind Turbines[J]. Boreas.
Shu, L., Qi, J., Hu, Q. et al., 2017. Anti-icing Model and
Sectionalized Anti-icing Method by Electrical Heating for
Wind Turbine Blades[J]. Proceedings of the Csee,
37(5):1448-1454.( in Chinese)
Technical Research Centre of Finland (VTT), 2013. Cold climate
wind energy showing huge potential. ScienceDaily.
ScienceDaily.
Xu, B., Lu F., Song, G., 2018. Experimental Study on Anti-Icing
and Deicing for Model Wind Turbine Blades with
Continuous Carbon Fiber Sheets[J]. Journal of Cold
Regions Engineering, 32(1).
Zhao, J., Yang, W., Peng, C. et al., 2016. ANTI-ICING AND
DEICING METHOD AND DEVICE FOR HIGH-POWER
WIND TURBINE BLADES, WO/2016/037476[P].
A Metamaterial Absorber for Microwave De-icing of Wind Turbine blades and its Electromagnetic and Thermal properties
221