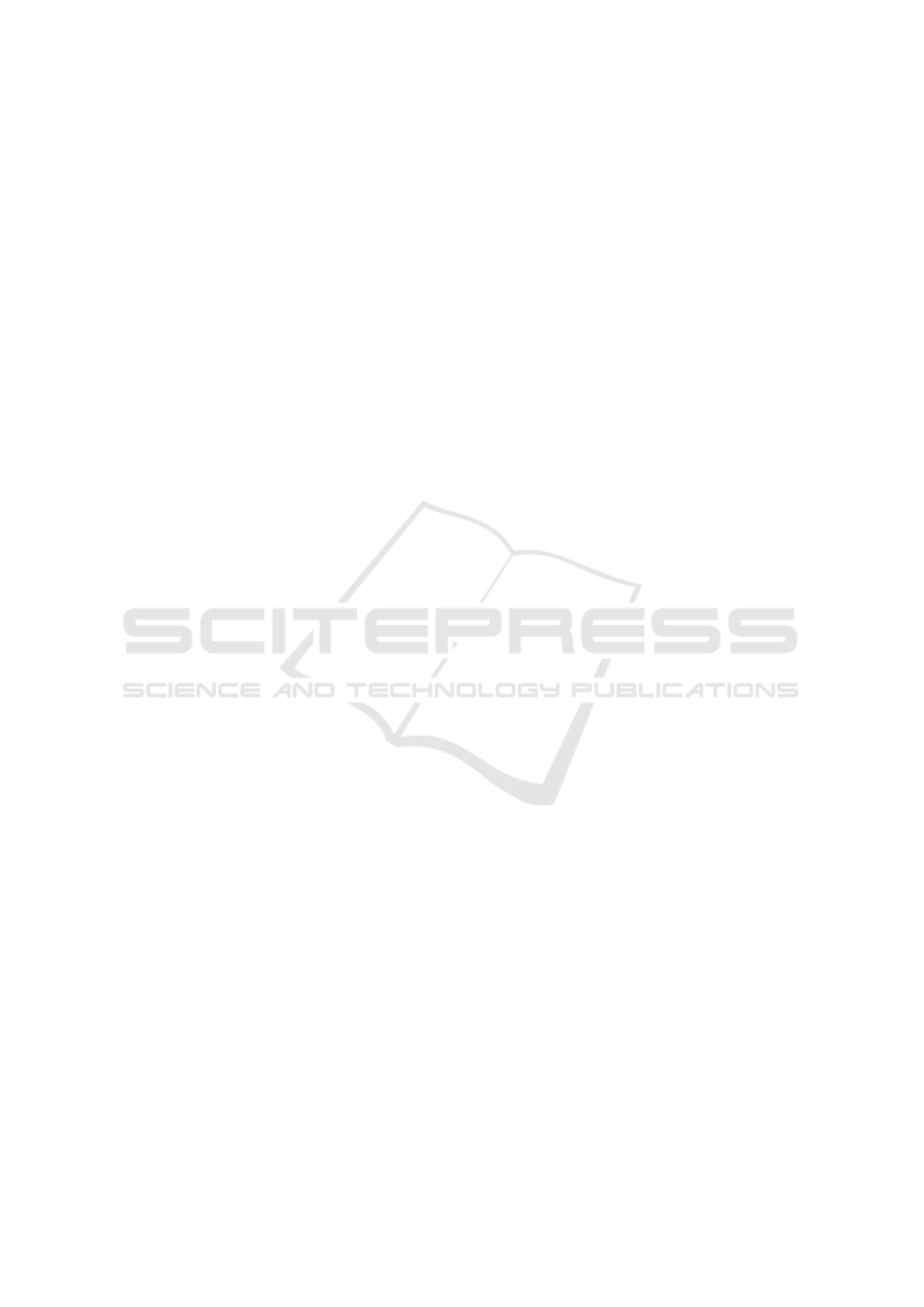
events demonstrates that the defects contribute to the
melting of SiO
2
materials.
Attribute to the presence of the void, there is a
higher potential energy for both of a-defect1 and
a-defect2. The glass transition temperature is
estimated to be 1812.6 K, 1846.4 K and 1587.8 K,
for a-intact, a-defect1 and a-defect2, respectively.
While the introduced of the defect concentration
1.47% makes the glass transition temperature reduce
by about 12.4%. From this calculated RMSD, we
can know that the vacancy cluster can reduce the
glass transition temperature of the material to a
certain extent.
ACKNOWLEDGEMENTS
We thank the financial support from the National
Natural Science Foundation of China (NSAF. Grant
No. 11176020 and NSFC. Grant No. 11374217).
REFERENCES
Afify, N.D., Mountjoy G., Haworth R., 2017. Comput.
Mater. Sci.128: 75.
An Q., Zheng L., Luo S. -N., 2006, J. Non-Cryst. Solids
352: 3320.
Assowe O., Politano O., Vignal V., Arnoux P., Diawara
B., Verners O., van Duin A. C. T., 2012. J. Phys.
Chem. A 116: 11796.
Bates, J. B., 1972. J. Chem. Phys. 57: 4042.
Berendsen, H. J. C., Postma, J. P. M., Van Gunsteren, W.
F., Dinola, A., Haak, J. R., 1984. J. Chem. Phys. 81:
3684.
Blöchl, P.E., 2000. Phys. Rev. B 62: 6158.
Chan, S. L., Elliott, S. R., 1991. Phys. Rev. B 43: 4423.
Chenoweth, K., Van Duin, A. C. T., Persson, P., Cheng,
M. J., Oxgaard, J., Goddard, W. A., III, 2008. J.
Chem. Phys. C 112: 14645.
Cowen, B. J., Ei-Genk, M. S., 2016. Comput. Mater. Sci.
111: 269.
El-Sayed, A., Watkins, M. B., Shluger, A. L., Afanas’ev
V. V., 2013. Microelectron. Eng. 109: 68.
Fowler, W. B., Edwards, A. H., 1997. J. Non-Cryst. Solids
222: 33.
Gilvarry, J. J., 1956. Phys. Rev. 102: 308; Voronel A.,
Rabinovitch S., Kisliuk A., Steinberg V., Sverbilova
T., 1988. Phys. Rev. Lett., 60: 2402.
Gubbels-Elzas, A., Thijsse, B. J., 2014. Comput. Mater.
Sci. 90: 196.
Gusev, E.P., 2000. in: G. Pacchioni, L. Skuja, D. Griscom
(Eds.), NATO Science Series, Kluwer Academic Press,
Dordrecht 557.
Hattori, S., Kalia, R. K., Nakano, A., Nomura, K.,
Vashishta, P., 2012. Appl. Phys. Lett. 101: 063106.
Hoang, V. V., 2007. J. Phys. Chem. B 111: 12649–12656.
Huff , N. T., Demiralp, E., Cagin, T., Goddard III, W. A.,
1999. J. Non-Cryst. Solids 253: 133.
Jin, Z. H., Gumbsch, P., Lu, K., Ma, E., 2001. Phys. Rev.
B 87: 055703-1.Kang J., Kim Y. -H., Bang J., Chang
K. J., 2008. Phys. Rev. B 77: 195321.
Kuo, C. -L., Hwang, G. S., 2006. Phys. Rev. Lett. 97:
066101.
Kurkjian, C. R., Krol, D. M., 2000. in: R.B. Devine, J.-P.
Duraud, E. Dooryheé (Eds.), John Wiley and Sons,
New York 449.
Lindemann, F. A., Phys Z., 1910. Physikalische Zeitschrift
der Sowjetunion 11: 609−612.
Luo, S. -N., Zheng, L., An, Q., Wu, H. -A., Xia, K., Ni, S.,
2007. Proc. SPIE 6403: 64030C-1.
Malavasi, G., Menziani, M. C., Pedone, A., Segre, U.,
2006. J. Non-Cryst. Solids 352: 285.
Mitra, S. K., Hockney, R. W., 1980. J. Phys. C: Sol. Stat.
Phys. 13: L739.
Mota, F., Molla, J., Caturla, M. -J., Ibarra, A., Perlado, J.
M., 2008. J. Phys.: Conf. Ser. 112: 032032.
Mukhopadhyay, S., Sushko, P. V., Stoneham, A. M.,
Shluger, A. L., 2004. Phys. Rev. B 70: 195203.
Newsome, D. A., Sengupta, D., Foroutan, H., Russo, M.
F., van Duin, A. C. T., 2012. J. Phys. Chem. C 116:
16111.
Peek, N.M., Jeffcoat, D.B., et al., 2018. J. Phys. Chem. C
122: 4349.
Plimpton, S., 1995. J. Comput. Phys. 117: 1.
Rimsza, J. M., Jones, R. E., Criscenti, L. J., 2018. J.
Colloid. Interface Sci. 516: 128.
Roder, A., Kob, W., Binder, K., 2001. J. Chem. Phys. 114:
7602.
Takada, A., Richet, P., Catlow, C.R.A., Price, G.D., 2004.
J. Non-Cryst. Solids 345−346: 224.
Ubbelohda, A. R., 1978. Wiley, Chichester.
van Duin, A. C. T., 2009.
http://www.wag.caltech.edu/home/duin/reax_um.pdf.
van Duin, A. C. T., Dasgupta, S., Lorant, F., Goddard, W.
A., III, 2001. J. Phys. Chem. A 105: 9396.
Vollmayr, K., Kob, W., Binder, K., 1996. Phys. Rev. B 54:
15808.
Weber, W. J. et al., 1998. J. Mater. Res. 13: 1434.
Wood, M. A., van Duin, A. C. T., Strachan, A., 2014. J.
Phys. Chem. A 118: 885.
Yu, Y., Wang, B., et al., 2016. J. Non-Cryst. Solids 443:
148.
Zachariasen, W.H., 1932. J. Am. Chem. Soc. 54: 3841.
Zhang, G., Li, X., Tung, C. -H., Pey, K. -L., Lo, G. -Q.,
2008. Appl. Phys. Lett. 93: 022901.
Zhang, J., Liebermann, R. C., Gasparik T., et al., 1993. J.
Geophys. Res. Solid Earth 98: 19785.
Zheng, L., An, Q., Fu, R., Ni, S., Luo, S. -N., 2006. J.
Chem. Phys. 125: 154511.
MEEP 2018 - The Second International Conference on Materials Chemistry and Environmental Protection
198