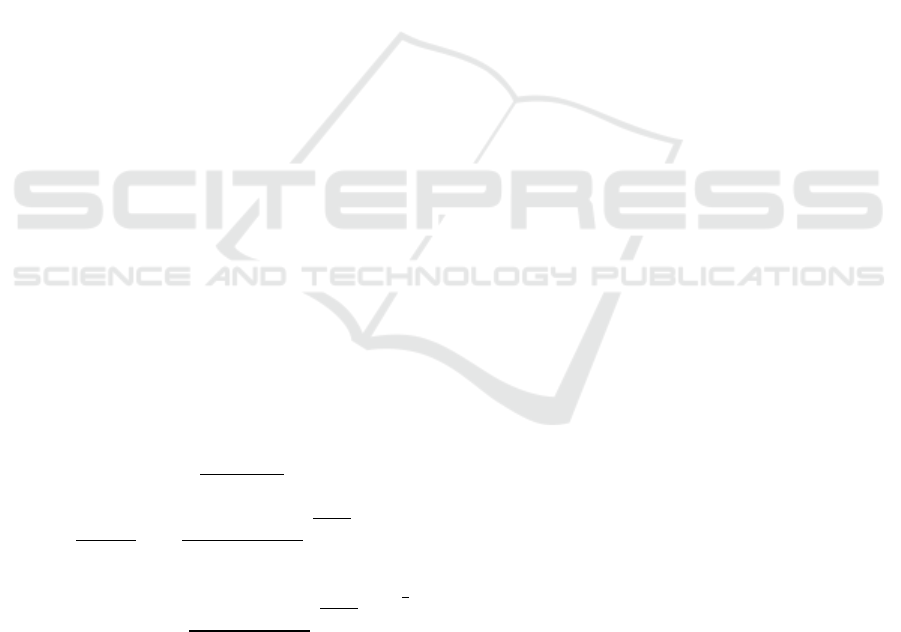
c
= 0.91
p
(23)
c
= 0.35
p
(24)
The ratio of
c
to
p
has been reported to be 0.43
for austenitic stainless steel, the general range
reported for steels is between 0.3 and 0.9, (Chen et
al., 2016) the ratio of
c
to
p
often takes values
between 0.83 (Wang et al., 2013) and 0.90 (Zhao et
al., 2014). So the values 0.35 and 0.91 are in
reasonable.
4 CONCLUSIONS
In this paper, the compression recrystallization
softening behaviour of 23Cr-2.1Ni-10Mn-1.3Mo
economical duplex stainless steel was investigated.
The main results can be summarized as follow:
(1) The austenite phase changes from dynamic
recrystallization to dynamic recovery with the
increasing of strain rate at the same
deformation temperature.
(2) The relationship between peak stress (strain)
and critical stress (strain) is:
c
=0.91
p
and
c
=0.35
p
. The critical strain in the low
temperature zone increases with the
increasing of deformation temperature and
strain rate, which increases first and then
decreases in the high temperature zone.
Combing with the Z parameter, DRX was
prone to occur under low Z conditions and
DRV occurred easily under high Z conditions.
(3) The thermal deformation and constitutive
equation of tested steel are shown as follow
respectively :
(4) The relationship between characteristic points
and flow stress on Z was obtained as ln
p
=
0.06253 lnZ-3.80363, ln
c
= 0.04641 lnZ-
3.91084, ln
p
= 0.14562 lnZ-0.06626 and
ln
c
= 0.14074 lnZ-0.05046.
ACKNOWLEDGEMENTS
This study was financially supported by the National
Natural Science Foundation of China (NSFC Project
no. 51461024).
REFERENCES
Charles, J., Chemelle, P., 2012. The history of duplex
developments, nowadays DSS properties and duplex
market future trends [J]. World. Iron. Steel., 144(2):
477.
Chen, L., Zhang, Y., Li, F. et al., 2016. Modeling of
dynamic recrystallization behavior of 21Cr-11Ni-N-
RE lean austenitic heat-resistant steel during hot
deformation [J]. Mater. Sci. Eng., A, 663: 141-150.
Chen, X. M., Lin, Y. C., Wen, D. X. et al., 2014. Dynamic
recrystallization behavior of a typical nickel-based
superalloy during hot deformation [J]. Mater. Des.,
2014, 57(5): 568-577.
Du, C. F., Zhan, F., Yang, Y. H. et al., 2010. Research
progress and application of double phase stainless
steel [J]. Met. Funct. Mater., 17(05): 63.
Frommert, M., Gottstein, G., 2009. Mechanical behavior
and microstructure evolution during steady-state
dynamic recrystallization in the austenitic steel 800H
[J]. Mater. Sci. Eng. A., 506(1): 101-110
Haghdadi, N., Martin, D., Hodgson, P., 2016. Physically-
based constitutive modelling of hot deformation
behavior in a LDX 2101 duplex stainless steel ☆ [J].
Mater. Des., 106: 420 - 427.
Imbert, C. A. C., Mcqueen, H. J., 2001. Peak strength,
strain hardening and dynamic restoration of A2 and
M2 tool steels in hot deformation [J]. Mater. Sci. Eng.
A., 313(1): 88-103.
Iza-Mendia, A., Piñol-Juez, A., Urcola, J. J. et al., 1998.
Microstructural and mechanical behavior of a duplex
stainless steel under hot working conditions [J].
Metall. Mater. Trans. A., 29(12): 2975-2986.
Meysami, M., Mousavi, S. A. A. A., 2011. Study on the
behavior of medium carbon vanadium microalloyed
steel by hot compression test [J]. Mater. Sci. Eng.
A., 528(7): 3049-3055.
Mishra, M. K., Balasundar, I., Rao, A. G. et al., 2017. On
the High Temperature Deformation Behaviour of 2507
Super Duplex Stainless Steel [J]. J. Mater. Eng.
Perform., 26(2): 1- 11.
Siegmund, T., Werner, E., Fischer, F. D., 1995. On the
thermomechanical deformation behavior of duplex-
type materials [J]. J. Mech. Phys. Solids., 43(4): 495-
532.
Wan, J., Ran, Q., Li, J. et al., 2014. A new resource-
saving, low chromium and low nickel duplex stainless
steel 15Cr– x Al–2Ni– y Mn [J]. Mater. Des., 53(1):
43-50.
Wang, M. H., Li, Y. F., Wang, W. H. et al., 2013.
Quantitative analysis of work hardening and dynamic
Study on Recrystallization Softening Behaviour of 23Cr-2.1Ni-10Mn-1.3Mo Economical Duplex Stainless Steels
191