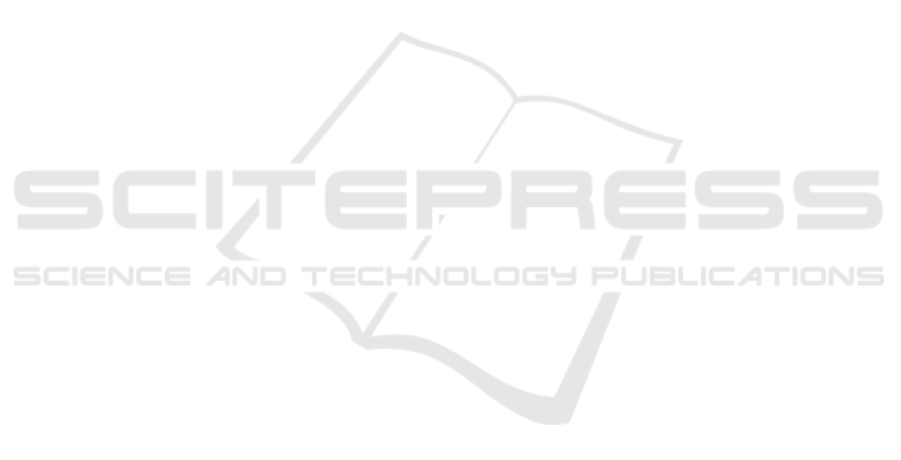
(2) MC in transverse cross-section of Anhui fir
shows polynomial distribution at any time, and
changes exponentially with time in drying
environment.
(3) MC gradient has a great influence in MC
changing speed, the larger the MC gradient is, the
quicker the speed will be.
(4) The method of substituting corresponding
variables in heat transfer in Abaqus to simulate
moisture transfer is valid.
Further research related to moisture transfer of
timber members in changing climate is still required.
Different initial MC distribution should also be
taken into consideration. Moreover, moisture-
induced stress and shrinkage cracks of timber
members are also essential research aspects for
timber buildings.
ACKNOWLEDGEMENTS
The authors would like to express their gratitude to
the whole staff in Key laboratory of concrete and
pre-stressed concrete structure of Ministry of
Education, Southeast University and Laboratory of
Modern Wood Structure, Nanjing University of
Technology for their technical support. And this
study was funded by the Thirteenth Five-Year
National Key Research and Development Program
(2017YFC0703503).
REFERENCES
Bonarski, J. T., Kifetew, G. & Olek, W. 2015, "Effects of
cell wall ultrastructure on the transverse shrinkage
anisotropy of Scots pine wood", Holzforschung, Vol.
69 No. 4, pp. 501-507.
Dietsch, P., Gamper, A., Merk, M. & Winter, S. 2015a,
"Monitoring building climate and timber moisture
gradient in large-span timber structures", Journal of
Civil Structural Health Monitoring, Vol. 5 No. 2, pp.
153-165.
Dietsch, P., Franke, S., Franke, B., Gamper, A. & Winter,
S. 2015b, "Methods to determine wood moisture
content and their applicability in monitoring
concepts", Journal of Civil Structural Health
Monitoring, Vol. 5 No. 2, pp. 115-127.
Fragiacomo, M., Fortino, S., Tononi, D., Usardi, I. &
Toratti, T. 2011, "Moisture-induced stresses
perpendicular to grain in cross-sections of timber
members exposed to different climates", Engineering
Structures, Vol. 33 No. 11, pp. 3071-3078.
Fortino, S., Mirianon, F. & Toratti, T. 2009, "A 3D
moisture-stress FEM analysis for time dependent
problems in timber structures", Mechanics of time-
dependent materials, Vol. 13 No. 4, pp. 333.
Hoyle Jr, R. J., Itani, R. Y. & Eckard, J. J. 2007, "Creep of
Douglas Fir Beams Due to Cyclic Humidity
Fluctuations", Wood and Fiber Science, Vol. 18 No. 3,
pp. 490-497.
Hoffmeyer, P. & Davidson, R. W. 1989, "Mechano-
sorptive creep mechanism of wood in compression and
bending", Wood Science and Technology, Vol. 23 No.
3, pp. 215-227.
Jia, D. & Afzal, M. T. 2007, "Modeling of moisture
diffusion in microwave drying of hardwood", Drying
technology, Vol. 25 No. 3, pp. 449-454.
Jönsson, J. 2005, "Moisture induced stresses in timber
structures". Lund, Lund Institute of Technology.
Kadem, S., Lachemet, A., Younsi, R. & Kocaefe, D. 2011,
"3d-Transient modeling of heat and mass transfer
during heat treatment of wood", International
Communications in Heat and Mass Transfer, Vol. 38
No. 6, pp. 717-722.
Konopka, D., Gebhardt, C. & Kaliske, M. 2017,
"Numerical modelling of wooden structures", Journal
of Cultural Heritage, Vol. 27, pp. 93-S102.
Mirianon, F., Fortino, S. & Toratti, T. 2008, "A method to
model wood by using ABAQUS finite element
software", Fire Safety Journal, Vol. 43.
Obe, J. D. 2002, Timber: its nature and behaviour, CRC
Press.
Qiu, L. 2015, "Performance of curved glulam beams under
load and moisture variations". Harbin, Harbin Institute
of Technology.
Ranta-Maunus, A. 2003, "Effects of climate and climate
variations on strength", Timber engineering, 153-167.
Skaar, C. 1958, "Moisture movement in beech below the
fiber saturation point", Forest Products Journal, No. 8,
pp. 352-357.
Siau, J. F. 1995, Wood: Influence of moisture on physical
properties, Dept. of Wood Science and Forest
Products, Virginia Polytechnic Institute and State
University.
Toratti, T. 1994, "Creep of timber beams in a variable
environment". Espoo, Teknillinen korkeakoulu.
Time, B. 2002, "Studies on hygroscopic moisture transport
in Norway spruce (Picea abies) Part 1: Sorption
measurements of spruce exposed to cyclic step
changes in relative humidity", Holz als Roh-und
Werkstoff, Vol. 60 No. 4, pp. 271-276.
Younsi, R., Kocaefe, D., Poncsak, S. & Kocaefe, Y. 2007,
"Computational modelling of heat and mass transfer
during the high-temperature heat treatment of wood",
Applied Thermal Engineering, Vol. 27 No. 8-9, pp.
1424-1431.
Zítek, P., Vyhlídal, T., Fišer, J., Tornari, V., Bernikola, E.
& Tsigarida, N. 2015, "Diffusion-model-based risk
assessment of moisture originated wood deterioration
in historic buildings", Building and Environment, Vol.
94, 218-230.
MEEP 2018 - The Second International Conference on Materials Chemistry and Environmental Protection
150