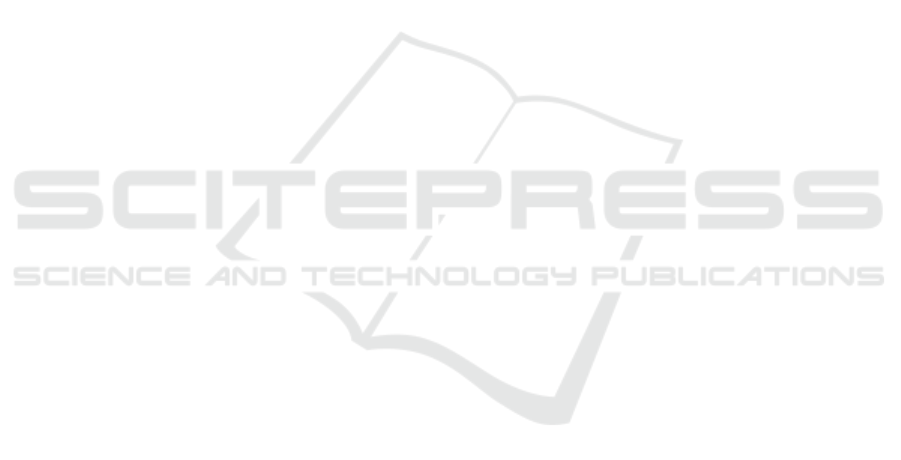
Study on Optimization of Fatigue Test of Nanosilver Solder
Hui Yang
1
, Yang Zhang
1
and Ji hui Wu
1
1
School of mechanical and control engineering, Guilin University of Technology
Keywords: Nano silver paste, sintering, mechanical fatigue test, cycle life.
Abstract: Nanosilver solder paste due to its high melting point, low sintering temperature and good electrical/thermal
conductivity and mechanical reliability Sex, more and more attention by the electronic packaging industry.
And, as a new type of lead-free thermal interface Materials, nano-silver solder paste has the potential to
gradually replace traditional solder and conductive silver paste, used in high-temperature power electronics
In the device packaging, according to the isothermal mechanical fatigue test, a temperature-dependent
fatigue life prediction model is proposed, and the cycle life of the nanosilver solder paste lap joint at
different temperatures is accurately predicted.
1.NANO-SILVERSOLDER PASTE
SINTERING
At present, due to the low-temperature sintering
characteristics of nano-silver particles, nano-silver
has been widely used in the electronic field, such as
low-temperature connection process, inkjet printing
technology, metal-metal bonding, etc. . CP Wong et
al. applied the low-temperature sintering
characteristics of nanosilver to ECAS[1,2]. It was
found that the surface chemistry of nanosilver
particles played an important role in the low-
temperature sintering of nanosilver. The low-
temperature pyrolysis of surface organics can
achieve the nanosilver particles in the conductive
paste. Sintered below 200°C . Fuller et al. introduced
an ink-jet technology based on nano-silver and gold
solder pastes for the production of conductive metal
lines on a substrate. The solder paste has good flow
ability and low viscosity. The results of the study
show that when the sintering temperature is as low
as 300°C, a metal line with high conductivity can be
obtained In addition, nanosilver paste can also be
printed on flexible substrates Bell et al. prepared a
silver paste containing nano-scale and micro-scale
mixed silver particles, and evaluated the sintering
process with an operating temperature lower than
250°C by measuring the conductivity .
2. FAILURE FORM
Reliability of Solder Joints in Electronic Packaging
The failure of semiconductors and microelectronic
devices is often the result of factors such as thermal,
mechanical, electrical, and chemical, either alone or
in combination. Therefore, failures of electronic
devices can be classified into thermal/mechanical
failures, electro-failures, and electrochemical effects.
Since most of the failures in the package structure
are caused by the mechanical failure of the
connection material, the reliability of the electronic
package is mostly focused on the thermal
mechanical properties of the solder joints [3,4]
3.STUDY AND EXPERIENCCE
3.1 Experimental Method
The nano-silver solder paste lap joint structure
used was tested on a miniature uniaxial fatigue tester.
The test ambient temperature was provided by an
external heating furnace. The isothermal mechanical
fatigue study uses a symmetric cyclic displacement
control method to apply load to the joint. The
waveform uses triangular waves[5,6].The loading
conditions for isothermal fatigue test of sintered
nano-silver joints are shown in Table 1. The
displacement rate control in the test was 2.07×