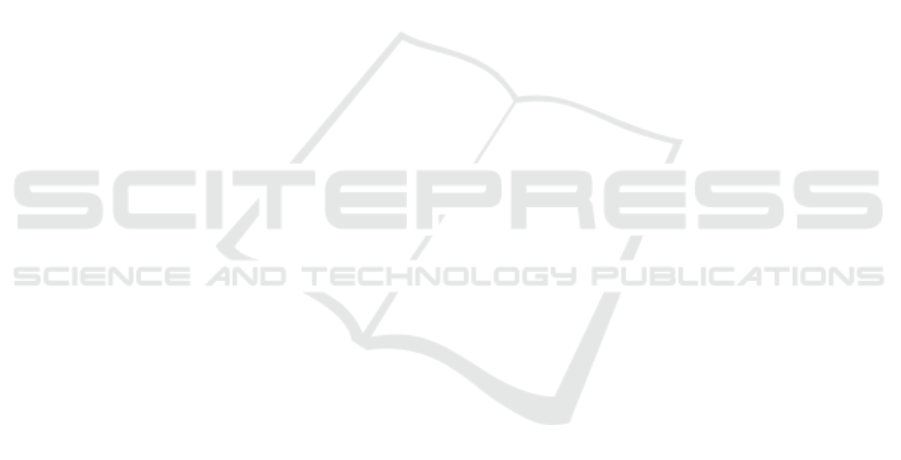
Analysis of Bolts’ Axial Corrosion Using Guided Waves
Based on FEM
P Ding
1,2, *
C Lu
3
, G F Ma
1
, T Li
1
, G F Yue
1
and X L Huang
1
1
Standard & Quality Control Research Institute Ministry of Water Resources. P.R.C,
Hangzhou, China
2
Key Laboratory of Research on Hydraulic and Hydro-Power Equipment Surface
Engineering Technology of Zhejiang Province, Hangzhou, China
3
Key Lab of Nondestructive Testing, Ministry of Education, Nanchang Hangkong
University, Nanchang, China
Corresponding author and e-mail: P Ding, qddp2008@126.com
Abstract. Bolts are widely used in water conservancy and hydropower engineering. There are
no good methods to test the corrosion defect of the bolts. Guided wave was used in this paper
to test the simulation axial defect in bolt based on FEM. The trend of the axial corrosion
coefficient and reflection coefficient of the guided wave was revelled. It shows that the
change trend of the defect reflection and wave type conversion of L (0, 1) mode and F (1, 1)
mode is consistent. The defect reflection of F (1, 1) is higher than the defect reflection of L (0,
1), both the defect reflection of F (1, 1) and L (0, 1) are no higher than 25%. And also it
verified the capability of low-frequency guided wave in detecting the small and medium
defects of bolts’ corrosion.
1. Introduction
Hydropower project transmission tower is an important facility to erect high-voltage transmission
lines. It is important to keep the tower fastness and reliable. The bolt is significant structure of
transmission tower, the safety and stability of bolt is in a very great degree affect the safety, stability
and service life of the transmission tower. Since the 1950s, China started using anchor in the coal
mine. And as support structure the anchor is widely used in the rock. With the development of
hydropower industry and the demand of the long-distance transmission, a large number of bolts have
been used in the cable of power transmission tower. These bolts are main load-bearing members,
which bear a large force and are used in bad environment. During the long term use, the effects of
cutting, fatigue and rainwater corrosion and the potential defects in the construction process easily
cause the failure, resulting in the occurrence of the accident. Not only does it cause enormous
economic losses, but it also results in casualties. Therefore, it is very important to use nondestructive
testing method to evaluate the operation condition and corrosion state of transmission tower. Guided
wave is a kind of ultrasonic wave which can be propagated in plates, rods and tubes, with the
advantages of small attenuation and long propagation distance. It has natural advantages for the
detection of transmission tower bolts defects such as rust.
616
Ding, P., Lu, C., Ma, G., Li, T., Yue, G. and Huang, X.
Analysis of Bolts’ Axial Corrosion Using Guided Waves Based on FEM.
In Proceedings of the International Workshop on Materials, Chemistry and Engineering (IWMCE 2018), pages 616-620
ISBN: 978-989-758-346-9
Copyright © 2018 by SCITEPRESS – Science and Technology Publications, Lda. All r ights reserved