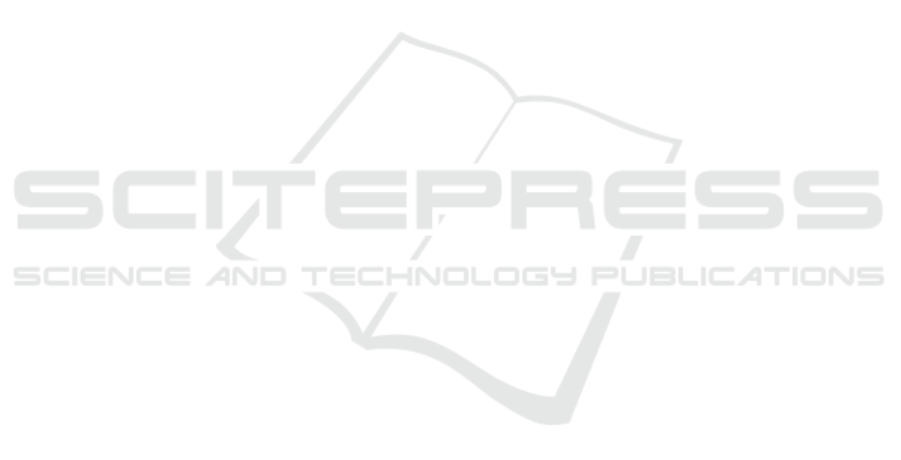
Kinetic Modelling of the Hydrolysis of COS Catalyzed by
Titania Based CT6-8
R H Zhu
1,2,*
, H G Chang
1,2
, C Y Tu
1
, C R Wen
1,2
, J L He
1,2
, Z S Liu
1
, S J Zhang
1
,
X Ma
1
and X Y Li
1
1
Research Institute of Natural Gas Technology, Petro China Southwest Oil and Gas
Field Company, Chengdu, Sichuan, P. R. China
2
National Energy R&D Center of High Sulfur Gas Exploitation, Chengdu, 610213,
China
Corresponding author’s e-mail address: R H Zhu, zhurh@petrochina.com.cn
Abstract. The carbonyl sulfide (COS) hydrolys is kinetic over titania based sulfur recovery
catalyst CT6-8 was studied. Kinetic data were obtained by orthogonal experimental design
under the conditions of 280-350
o
C, contact time 3.5×10
-6
-10
-5
h, COS concentration 0.1-1%,
H
2
O concentration 5-30%, H
2
S concentration 2-5%, SO
2
concentration 1-2.5%, without both
internal and external diffusion limitation. The relationship between the reaction rate and the
experimental conditions was fitted by power function model and the COS hydrolysis reaction
kinetic equation was obtained as
2 2 2
7 65100/ 0.11 0.67 0.96 0.17
1.77 10
RT
COS H S SO COS H O
r e P P P P
.
1. Introduction
The Claus process works well for gas streams containing greater than 20% H
2
S and less than 5%
hydrocarbons in the world. The first stage of the Claus process is the thermal oxidation of 1/3 of the
initial H
2
S concentration at high temperature condition. The formation of COS and CS
2
is inevitable
for the present of hydrocarbon in the combustion step. The efficient hydrolysis of COS and CS
2
is
helpful to achieve the high levels of sulfur recovery rate. In the first reactor, the conversion of COS
and CS
2
is limited to 75% for COS and 50% for CS
2
by alumina catalyst while titania-based catalysts,
such as CRS-31 & CT6-8, are regarded as a more efficient way for COS and CS
2
hydrolysis [1].
CS
2
and COS are two problem compounds that often appear together in the first Claus converter.
The kinetic of CS
2
and COS hydrolysis have been studied in numerous research papers [2-5]. Tong
studied the hydrolysis of CS
2
and COS for a titania catalyst and found that the hydrolysis of CS
2
can
be best described by an Eley-Rideal model over the ranges of temperature from 270 to 330
o
C. In this
study, the feed gas contains only CS
2
or COS, H
2
O and N
2
[6,7]. In the first Claus converter, H
2
S and
SO
2
with high concentration, can strongly influence the hydrolysis of CS
2
or COS. We have reported
the hydrolysis of CS
2
in the presents of H
2
S and SO
2
, and got great different results compared with
the previous reports [8].
In this research, the kinetic measurements for the hydrolysis of COS using titania-based CT6-8
catalyst was obtained under controlled condition using a continuous flow fixed bed reactor. The
466
Zhu, R., Chang, H., Tu, C., Wen, C., He, J., Liu, Z., Zhang, S., Ma, X. and Li, X.
Kinetic Modelling of the Hydrolysis of COS Catalyzed by Titania Based CT6-8.
In Proceedings of the International Workshop on Materials, Chemistry and Engineering (IWMCE 2018), pages 466-470
ISBN: 978-989-758-346-9
Copyright © 2018 by SCITEPRESS – Science and Technology Publications, Lda. All rights reserved