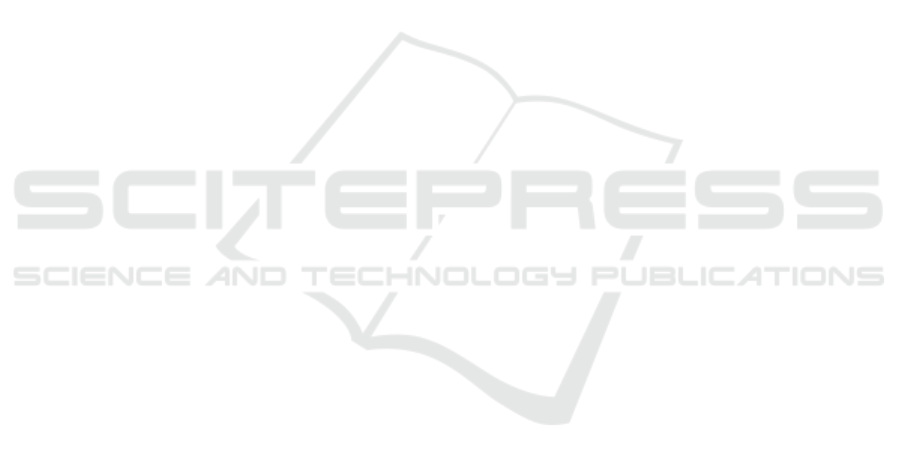
responsible for the enhanced thermal conductivity of the alloy with the aging treatment as shown in
Figure 5.
Usually, the ageing treatment leads to the reduction of solute atoms in the Mg matrix and the
subsequent formation of element particles or intermetallic compounds, which would definitely affect
the thermal conductivity of the alloys. However, no new precipitate except Mg
7
Zn
3
and Mg has
been detected by XRD analysis, which is associated with the limited concentration of alloying
elements, Mn, Zn and Nd. Therefore,the changes of defects and grain boundaries of the Mg alloy
during the aging treatment are mainly responsible for the slight increase of thermal conductivity with
the aging time. If new phase precipitates from the Mg alloy, the variation of thermal conductivity
would be abrupt.
According to Figures 4 and 5, it can be observed that the Mg alloy aged at 200C for 24 h has
good combination of both mechanical and thermal properties. The thermal performance of heat
dissipation materials is an essential thermophysical property. The higher thermal conductivity of
metal fins leads to better cooling effect [22], which can prevent the electric (al) equipment from
overheating and prolong the service life. Huawei Technology Co., Ltd., a globe leading manufacturer
of information and technology, demanded that the cast and wrought Mg alloys at least should possess
the thermal conductivity of 100 and 120 W/(mK), respectively[23]. Therefore the Mg-1Mn-2Zn-1Nd
alloy aged at 200C for 24 and 48 h meets this requirement forthe wrought Mg alloys and is expected
to be a good candidate of heat dissipating alloys.
4. Conclusions
The thermal conductivity of the Mg-1Mn-2Zn-1Nd alloy aged at 200C for the different aging time
was studied at room temperature by laser flash method. The experimental results indicate that the
thermal conductivity of the Mg-1Mn-2Zn-1Nd alloy slowly increases with the aging time and
exceeds the required critical value (120 W/(mK)) of wrought Mg alloys, thus the aged Mg-1Mn-
2Zn-1Nd alloy is expected to be a good candidate for the application of heat dissipation.
Acknowledgment
The work was financially supported by the Science and Technology Innovation Platform of Foshan
City, Guangdong Province, China (Grant No. 2014AG10009 and 2016AG100341). And the special
gratitude was expressed to Professor Lei Wang from Northeastern University, China for his kind help
during the hot-extrusion process.
References
[1] Hu F and Chen Z 2009 Calorimetric technology and determination of thermal properties
(Hefei: China University of Science and Technology Press China)p239241
[2] Yamasaki M and Kawamura Y 2009 Scripta Mater.60 264
[3] Rudajevová A, Staněk M and Lukáč P 2003 Mater. Sci. Eng. A341 152
[4] Chen C J, Wang Q D and Yin D D 2009 J. Alloys Compd.487560
[5] Li Y, Xiao Z, Li Z, Zhou Z, Yang Z and Lei Q 2017 J. Alloys Compd. 7231162
[6] Wang C, Liu Z, Xiao S and Chen Y 2016 Mater. Sci. Techno. 32(6) 581
[7] Su C, Li D, Ying T, Zhou L, Li L and Zeng X 2016 J. Alloys Compd.685114
[8] Pan H, Pan F and Yang R 2014 J. Mater. Sci.493107
[9] Zhong L, Peng J, Sun S, Wang Y, Lu Y and Pan F 2017 J. Mater. Sci. Techno.3392
[10] Yuan J, Zhang K, Li T, Li X, Li Y, Ma M and Luo P 2012 Mater. Des.40 257
[11] Yuan J, Zhang K, Zhang X, Li X, Li T, Li Y, Ma M and Shi G 2013 J. Alloys Compd.57632
[12] Ying T, Zheng M Y, Li Z T and Qiao X G 2014 J. Alloys Comp.608 19
Increased Thermal Conductivity of Mg-1Mn-2Zn-1Nd Alloy with Aging Time
219