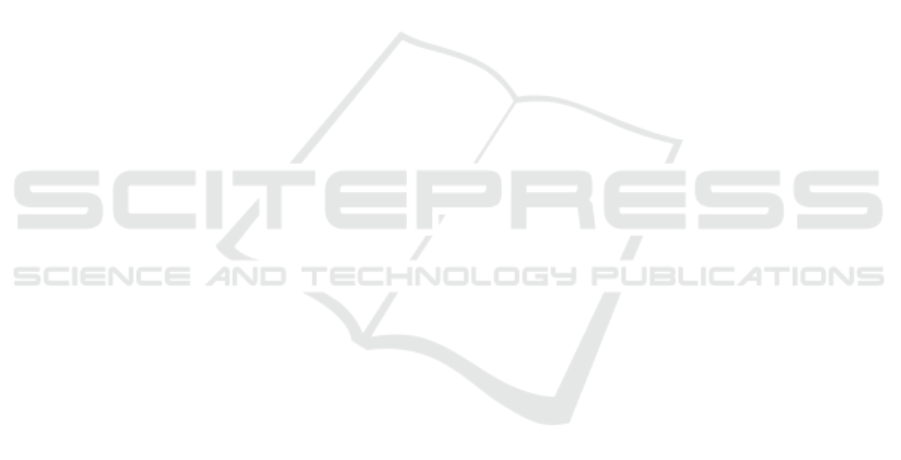
Chemical Flooding Process Integration of Low Viscosity Loss
Points Injection Technology Research and Application
S G Zhu
1
, F S Wang
1
, D K Xu
1
, C J Liu
1
, Q Z Li
1
,X L Song
1
, Q Ma
1
, H C Li
1,*
, L
J Wang
1
, P Li
2
, P F Tang
3
and G L Gao
1
1
Production and Engineering Research Institute Daqing oilfield Limited liability
company, Daqing
2
No.4 Oil Production Plant of Daqing Oilfield Co. Ltd, Daqing
3
No.6 Oil Production Plant of Daqing Oilfield Co. Ltd, Daqing
Corresponding author and e-mail: H C Li, lihaicheng@petrochina.com.cn
Abstract. Injection technology for water flooding points exist at the polymer solution flowing
through the injection allocation generated when mechanical degradation,big viscosity loss
need to inject (over 30%) and low permeable reservoirs with low relative molecular mass of
polymer solution, in order to make sure no problem such as block reservoir.Chemical
flooding process is studied in the integration of hierarchical points injection
technology,designed the low viscosity loss high throttling pressure regulator, wide adjusting
range low molecular weight and regulator of the choke points and the whole process of the
integration of eccentric injection allocation, layered injection and dual regulation of relative
molecular mass.Hydraulic characteristics, laboratory test results show that within the scope of
the flow rate of 70 m
3
/d, viscosity loss rate has dropped from 30% to 10%, and separate
injection technology compatible with water flooding, injection string meet blank water
flooding, separate chemical flooding and subsequent water flooding process need, reduce the
investment and production cost, is the application of more than 3000 Wells.Field test results
show that 2-3 interval cast get success rate of 95.6%, a 95% success rate increase.Statistics a
layered polymer injection blocks, separate injection Wells using layer is 9.8% higher than
general Wells, the thickness of use increased by 10.3%.
1. Introduction
Daqing oilfield is a heterogeneous multi-layer sandstone oilfield with largely different permeability,
tertiary oil recovery technology has become an important means for its stable production. Practice
showed[1,2] that chemical flooding could increase crude oil recovery ratio by more than 20
percentage points compared with water flooding. At present, the oil production of chemical flooding
wells is close to 1/3 of total output. With the development of chemical flooding, the class II and III
reservoirs with big difference in permeability and large interlayer contradictions have gradually
become the main development objects. However, in order to alleviate the contradiction between
layers, the separate injection technology needs to be improved in the process of chemical flooding
medium injection. Because of the mechanical degradation of polymer solution by shearing, the
conventional water flooding injection allocator has serious degradation of polymer and large
Zhu, S., Wang, F., Xu, D., Liu, C., Li, Q., Song, X., Ma, Q., Li, H., Wang, L., Li, P., Tang, P. and Gao, G.
Chemical Flooding Process Integration of Low Viscosity Loss Points Injection Technology Research and Application.
In Proceedings of the International Workshop on Materials, Chemistry and Engineering (IWMCE 2018), pages 167-173
ISBN: 978-989-758-346-9
Copyright © 2018 by SCITEPRESS – Science and Technology Publications, Lda. All rights reserved
167