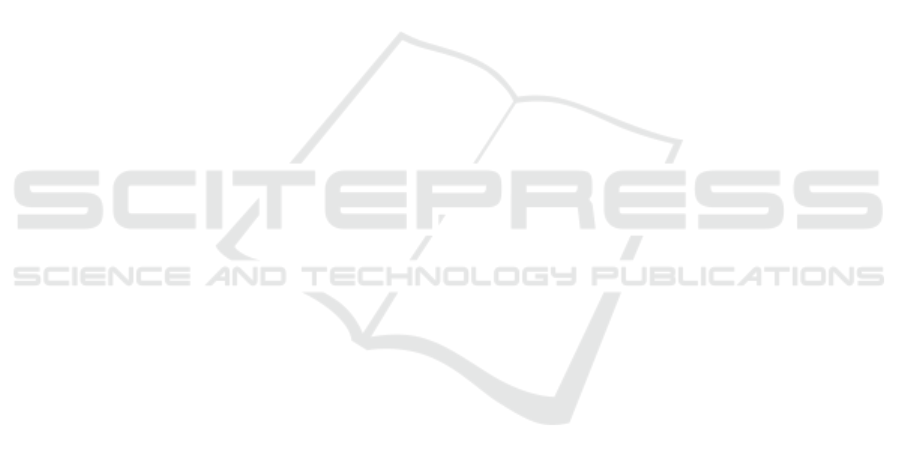
Study on Laminar Flow Field Characteristics in Stirred Tank
with Different Combinations of Dual Impellers
Q X Bu
*
and X Wei
College of Electromechanical Engineering, Qingdao University of Science and
Technology, Qingdao 266061, Shandong, China
Corresponding author and e-mail: Q X Bu, qdbuqiuxiang@163.com
Abstract. The numerical simulation of the flow field generated by dual impellers in glycerol
was carried out by using CFD method and laminar flow model. The flow field structure of
four combinations of impellers under different spacing and constant rotation speed of 200
rpm in the stirred tank is obtained, and axial and radial velocity vectors and velocity
distribution curves are compared and analyzed. The results show that when the distance
between layers is greater than or equal to T / 2, the flow pattern of the flow field is parallel
flow, and the distribution of the two straight blades is the best. When the distance between
layers is less than T / 3, the flow pattern is connected flow,at this time, the combination of the
run-off impeller under the axial propeller is the best.
1. Introduction
With the development of technology and the expansion of production scale, the volume of industrial
agitator reactor tends to be large, and most of the high-diameter ratio is usually greater than 1. The
distribution range of the materials involved is also very wide, which includes the low viscosity fluid
with the fast settlement of solid particles and the non-newtonian fluid with high viscosity and shear
thinning properties. This requires the use of double-layer and multi-layer impellers and effective
combination to ensure the mixing effect of the reactor. At present, the research on the single layer
paddle stirred tank in the flow characteristics
[1-6], mixing time
[7-10], energy dissipation
[11-12],
wake vortex structure
[13-15] and the impact of blade height from the bottom
[16-17] is quite
in-depth and systematic. Lightnin company in USA has developed a new type of axial flow impeller
by using experiment and CFD simulation technology, such as efficient A310, A315 and A340 series
[18-19] that the pitch and width of the blade vary with its radial position, which can effectively
improve the efficiency of mixing, and the D&R work of wing-shaped impeller is gradually being
carrying out in china. The mixing characteristics of two layers and multi-layer impeller [20-29] have
also been studied. Hao Zhigang et al. [30] studied the dispersion of gas in a stirred tank with different
mixing impellers, and considered that the combination of the run-off impeller under the axial
propeller the radial paddle was the most suitable for gas-liquid dispersion. Liang Yingna et al. [31]
used the CFD laminar flow model to simulate the double-layer straight-skewed impeller blade
combination and analyzed the structural characteristics of different forms of flow field.
Up to now, the research on the flow of stirred tanks with two-layer and multi-layer impellers
mainly focuses on turbulent flow conditions. However, the research on the flow field characteristics
of laminar flow in high viscosity system is relatively few, and the effect of layer spacing on flow is
152
Bu, Q. and Wei, X.
Study on Laminar Flow Field Characteristics in Stirred Tank with Different Combinations of Dual Impellers.
In Proceedings of the International Workshop on Materials, Chemistry and Engineering (IWMCE 2018), pages 152-160
ISBN: 978-989-758-346-9
Copyright © 2018 by SCITEPRESS – Science and Technology Publications, Lda. All rights reserved