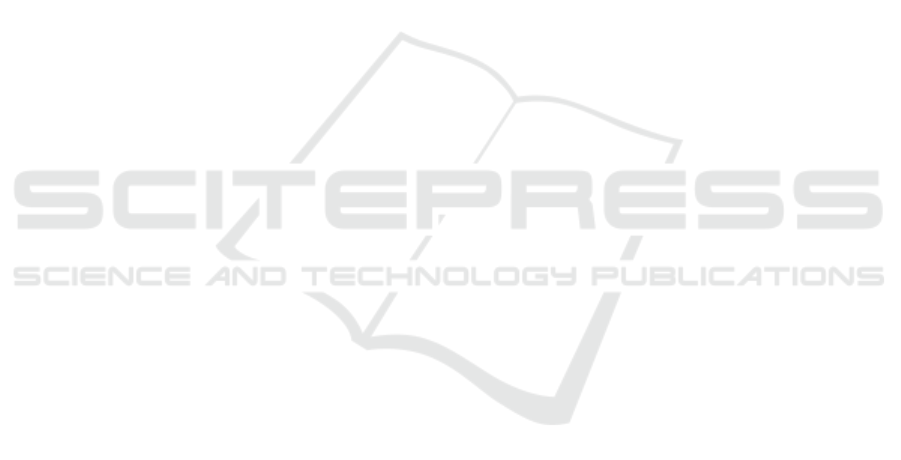
The Design and Analysis of Free Bending Tube Bending
Machine
Y S Li, Z M Yue
*
, F R Liu, J S Qi and J Gao
School of Mechanical, Electrical and Information Engineering, Shandong University
at Weihai, China
Corresponding author and e-mail: Z M Yue, yuezhenming@sdu.edu.cn
Abstract. The existing devices for the 3D tube bending normally are complex on the
mechanism and unmanageable. In this study, a new kind of tube bending machine which can
realize the free bending in space through using the principle of superimposing two main parts,
which provide more degree of freedom for the new developed machine. Screw system is
established based on screw theory, then the analysis about the degree of freedom of each
main part and the overall mechanism has been conducted.
1. Introduction
In addition to good processing and forming properties, the tube material has the characteristics of
high strength stiffness and high material utilization. The demand for high quality and high-precision
tube bender is increasing, and owing to excellent characters like high strength and stiffness and high
efficient utilization, the bent tube have an important application in many fields of national production,
such as the furniture, fluid arrangements, aviation, aerospace, automobile and precision machinery
[1,2]. The bending process of the metal tube is one common forming process. The purpose of this
process is translating the tube into the defined profile with specific bending curvature, angle and
shape. Traditional bending methods of tubes include rotary-draw bending, press bending and roll
bending [3].
Tube bender is the main mechanical equipment for tube bending process. At present, there are
mainly CNC bending machine, press machine, roll bending machine, draw bender and so on.
However, with the demand for complex spatial tube is increasing, there are lots of limitations in
traditional tube benders which can only be fit for the profiles which have simple shapes and bend
radii without continuous changing. The latest technology of 3D free forming can overcome the
shortcomings above, and it can make tube shaped precisely in 3D space.
As the complex spatial tube has been successfully applied in material forming field , lots of design
about the 3D bender for tube has been arising in recent years. This kind of technology makes use of
the principle of the modeless forming and the hydraulic servo control technology, it uses servers to
design radian of tube, and finally realize the control of final forming shape of tube. This kind of
technology has changed traditional process of die forming of tube, and overcome the disadvantages
and limitations of die forming which can make forming process flexible and convenient. It can also
improve greatly the efficiency and precision of the production process.
Li, Y., Yue, Z., Liu, F., Qi, J. and Gao, J.
The Design and Analysis of Free Bending Tube Bending Machine.
In Proceedings of the International Workshop on Materials, Chemistry and Engineering (IWMCE 2018), pages 115-121
ISBN: 978-989-758-346-9
Copyright © 2018 by SCITEPRESS – Science and Technology Publications, Lda. All rights reserved
115