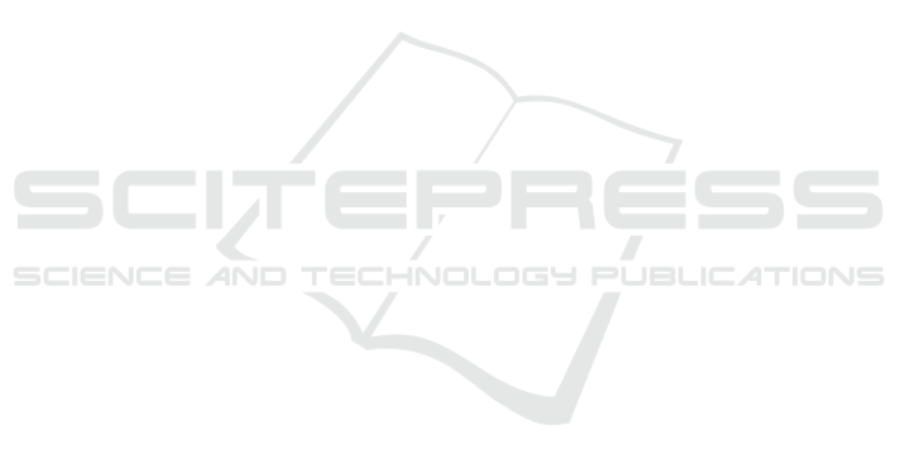
Study on Dynamic Constitutive Model and Parameter
Analysis of Ti/Ni Shape Memory Alloy Based on Irreversible
Thermodynamics
Y S Yang
1
, X G Zeng
1, *
, J Chen
2
, Y Guo
1
and Y Sheng
3
1
College of Architecture and Environment, Sichuan University, Chengdu, Sichuan,
610065, P.R. China
2
Institute of Applied Physics snd Computational Mathematics, Beijing100094, P.R.
China
3
Southwest University of Science and Technology, Mianyang, Sichuan621000, P.R.
China
Corresponding author and E-mail: X G Zeng, xiangguozeng@scu.edu.cn
Abstract. The dynamic constitutive model of Ti/Ni shape memory alloy based on irreversible
thermodynamics theory was established by introducing two internal variables to characterize
phase transformation and plastic deformation process. The evolution laws of phase
transformation and plastic deformation were deduced respectively by assuming two
generalized force associated with the corresponding internal variables.Latin Hypercube
Sampling method is applied to sample among the whole parameter space for constitutive
parameter of Ti/Ni alloy dynamic constitutive model based on irreversible thermodynamics
theory, and Spearman rank correlation analysis of non-parameter statistics method is
employed to conduct correlation analysis for random-input sample set of constitutive
parameter and the output set of its corresponding objective function. A model is built to solve
parameter sensitivity based on Spearman rank correlation coefficient, in order to achieve
overall analysis of parameter sensitivity. According to results, numerical results, obtained
with this method, are well consistent with experimental data. Furthermore, the optimal
solution to the dynamic constitutive parameters can be realized with high efficiency, accuracy
and reliability via the research method on parameter sensitivity analysis and identification put
forward in this paper.
1. Introduction
Ti/Ni alloy is not only widely used in Aviation & Aerospace, Mechanics, Electronics, Energy, and
Medical field [1-2], but also the Ti/Ni alloy high strain dynamic responding behavior is closely
related to a great many of applications [3]. Meanwhile, the unique Shape Memory Effect and
excellent Super-elasticity of the Ti/Ni alloy draws wide attention to researchers at home and abroad,
and it is currently one of the Shape Memory Alloys that studied and applied most [4]. The Super
elasticity of Ti/Ni alloy refers to the phenomenon that the strain, which produced under effect of
external force, is far greater than its elastic limit, but self recovers when unloaded. The Shape
Memory Effect refers to the phenomenon when material going through plastic deform, and being
100
Yang, Y., Zeng, X., Chen, J., Guo, Y. and Sheng, Y.
Study on Dynamic Constitutive Model and Parameter Analysis of Ti/Ni Shape Memory Alloy Based on Irreversible Thermodynamics.
In Proceedings of the International Workshop on Materials, Chemistry and Engineering (IWMCE 2018), pages 100-106
ISBN: 978-989-758-346-9
Copyright © 2018 by SCITEPRESS – Science and Technology Publications, Lda. All rights reserved