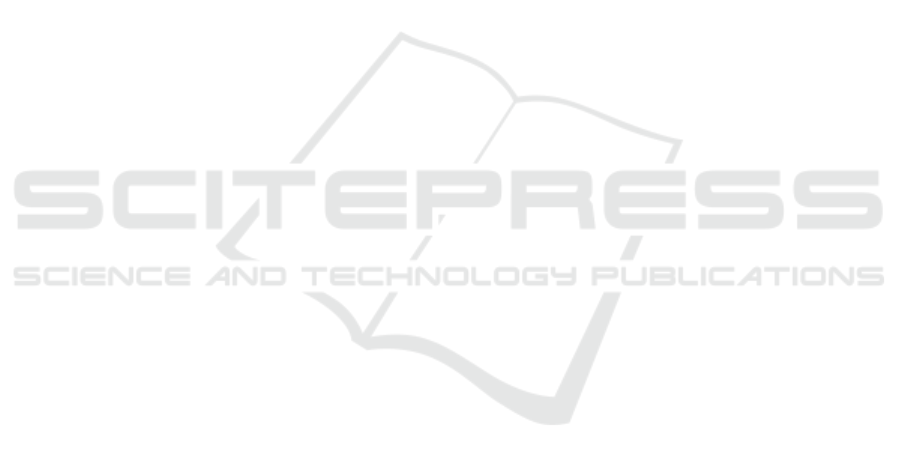
Low Noise Design of Regenerative Blower by Combining the
FANDAS-Regen Code, Optimization Technique and
Phase-Shift Cancellation Concept
Chan Lee, Hyun Gwon Kil and Jun Kon Kim
Department of Mechanical Engineering, University of Suwon, Hwaseong, Korea
Keywords: Regenerative Blower, FANDAS-Regen Code, Optimization Algorithm, Low Noise.
Abstract: Low noise regenerative blower is designed by combining the FANDAS-Regen code and optimization
technique. The FANDAS-Regen code used in the present study defines blower design variables on rotating
impellers and fixed side channels, and then constructs the 3-D blower design geometry. Based on the
designed blower geometry, the FANDAS-Regen code also analyzes the blower performance as well as noise
characteristics by using momentum exchange theory coupled with pressure loss and leakage models and by
incorporating the performance prediction results into discrete and broadband noise models. With the
FANDAS-Regen code as a simulation engine, design optimization is conducted for impeller and side
channel design variables to minimize overall sound pressure level of blower under the constraints of
aerodynamic design requirements on pressure rise, efficiency and power consumption. Furthermore, for
more noise reduction of blower, a staggered impeller blade arrangement as a phase-shift cancellation design
concept is also applied to the optimized impeller design. The optimized blower model is manufactured and
tested by a chamber-type performance tester and narrow-band noise measurement apparatus. The
performance measurement results agree well with the FANDAS-Regen prediction, and the noise
measurement results show a remarkable noise reduction of 26 dBA through the present design optimization.
1 INTRODUCTION
Regenerative blowers are usually operated with high
pressure rise at low flow capacity and are widely
used as the gas supply equipment of fuel cell
automotive vehicles and distributed fuel cell power
systems (Badami and Mura, 2011; 2012). However,
because the most of these fuel cell systems are
located very close to human users, when
regenerative blower is used in the fuel cell
applications, its high noise characteristics would be
main shortcoming and hurdle to be applied in the
fuel cell applications. For this reason, there are
growing industrial needs of low noise regenerative
blower design.
Through the previous research by authors(Lee et
al., 2013), the FANDAS-Regen code as design-
analysis program for regenerative blower has been
developed and showed its good prediction
accuracies on performances and noise levels of
designed regenerative blower. In the FANDAS-
Regen code, 3-D blower geometry on impeller
blades and side channel is designed, and then blower
performances are predicted by the momentum
exchange theory between the rotating impeller
blades and the fixed side channel. After the predicted
performance results are obtained and then
incorporated with the noise models of the FANDAS-
Regen code, discrete frequency noise at blade
passing frequency and its harmonics are predicted by
acoustic mode analysis, and broadband noise is also
predicted by the combination of several correlation
models for inflow turbulence, impeller turbulence
and exhaust jet mixing. The performance and noise
prediction accuracies of the FANDAS-Regen code
are verified by comparing the prediction with the
measurement results of actual regenerative blowers.
Furthermore, with the use of the present analysis
method of the FANDAS-Regen code as simulation
engine, design optimization is conducted for two
impeller and side channel design variables to
minimize overall noise level of blower, and then a
phase-shift cancellation concept of staggered
impeller blade arrangement is also applied for more
noise reduction of optimized blower. The optimized
469
Lee C., Kil H. and Kim J..
Low Noise Design of Regenerative Blower by Combining the FANDAS-Regen Code, Optimization Technique and Phase-Shift Cancellation Concept.
DOI: 10.5220/0005514304690475
In Proceedings of the 5th International Conference on Simulation and Modeling Methodologies, Technologies and Applications (SIMULTECH-2015),
pages 469-475
ISBN: 978-989-758-120-5
Copyright
c
2015 SCITEPRESS (Science and Technology Publications, Lda.)