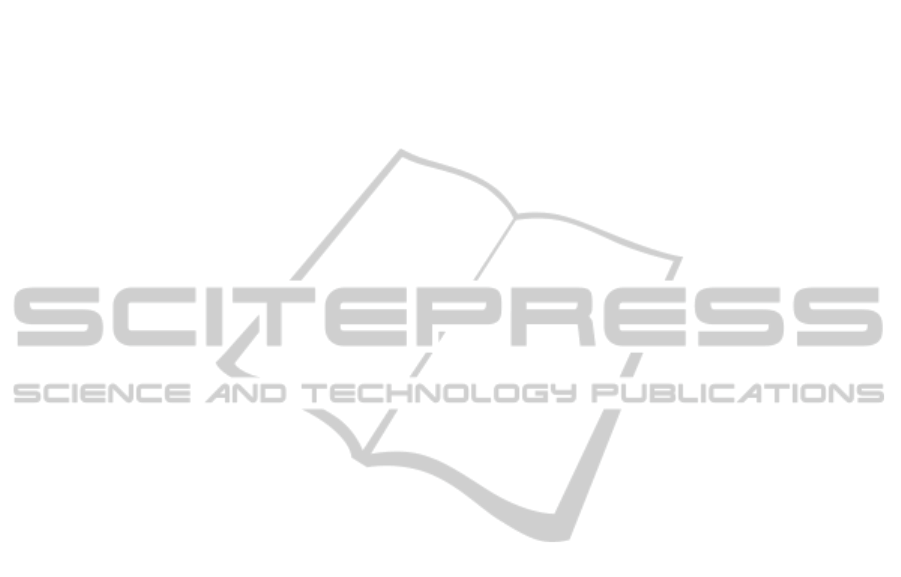
Analysis of different communication
technologies gave in this paper with different
communication requirements like latency, reliability,
frequency and security. Study of wireless sensor
network for smart grid monitoring application gave
in (Gungor and Hancke, 2010). The authors did an
experimental study of WSN at different power grid
scenario and found that it can meet most of the
communication requirements needed for smart grid
communication.
3 MICROGRID ARCHITECTURE
FOR FAULT DETECTION AND
ISOLATION
In this work we considered a three phase micro grid,
which operates in islanded mode. Each smart home
in this system had the capability to generate power
from a renewable energy resource and stored it. In
order to maintained the system self sustaining, the
extra power generated within the system could share
among the load centres according to the power
demand. This sharing of power between the loads
was vital since the micro grid was not connected to
the regular power grid source. The system
architecture of the proposed system is given in
Figure1.
In the figure 1, the micro grid has nine
distribution poles named as Pole 1, Pole 2 …Pole 9
and each distribution pole is connected to each smart
home. In this work we considered only single phase
loads which were equally distributed along three
phases. We assumed that every load had a renewable
energy source and it will act both as a load and
generator. The extra power produced can also be
stored. The smart meter which was present at each
smart home can continuously monitor the
bidirectional power flows into the home as well as
away from the home. Since a three phase
distribution grid was considered in this work, the
distribution pole will have three power lines. In
order to monitor the three phase lines, we needed to
use three intelligent modules at each distribution
pole. If we have only had one intelligent module to
monitor the three phase lines, failure of this
intelligent module could cause the three phase lines
unobservable. Thus, intelligent modules for each
phase line would improve the robustness of the
system. At each distribution pole, the breakers
associated with an intelligent module. A control
station associated with the micro grid to control and
take decision according to data of the system.
4 FAULT DETACTION AND
ISOLATION METHOD
Power sharing is one of the key features of the
proposed micro grid system. Faults which may occur
in this three phase micro grid could cause the system
to unbalance and prevent the power sharing.
Therefore, a fault detection and isolation mechanism
is very essential for the continuous operation of the
system. In this work, only the single line to neutral
fault was considered since 95 % of the fault occurs
within a three phase system was this type of fault.
Each distribution pole was associated with three
intelligent modules for each phase line. Each
intelligent device was connected to a current sensor,
voltage sensor, circuit breaker, communication
module and a micro controller unit. These sensors
along with circuit breakers and communication
modules were connected to the micro controller. The
block diagram of an intelligent device is shown in
Figure 2. Current sensors and voltage sensors
continuously monitored the current and voltage
condition at each phase line. The processor unit at
each intelligent device continuously checked
whether the current values exceeded the allowable
lower and upper threshold limit. If the current sensor
value had exceeded the threshold limits, the circuit
breaker present at that phase line opened the circuit.
5 FAULT LOCALIZATION
METHOD
After the fault detection and isolation the intelligent
device continuously sent the sensed current value to
its neighbouring distribution pole’s intelligent
device. Whenever an intelligent device received a
message from its neighbour, it compared the
received value with its own sensed value. Each
intelligent device took one of the two decisions after
this comparison.
a. If the difference in current values of the
adjacent intelligent module was not a high
value, then no fault occurred between the two
poles and the status of the breaker was closed
condition.
b. If the difference in current values of the
adjacent intelligent module was a high value
then a fault occurred between the two poles and
it opened the breaker associated with that phase
line.
SMARTGREENS2015-4thInternationalConferenceonSmartCitiesandGreenICTSystems
252