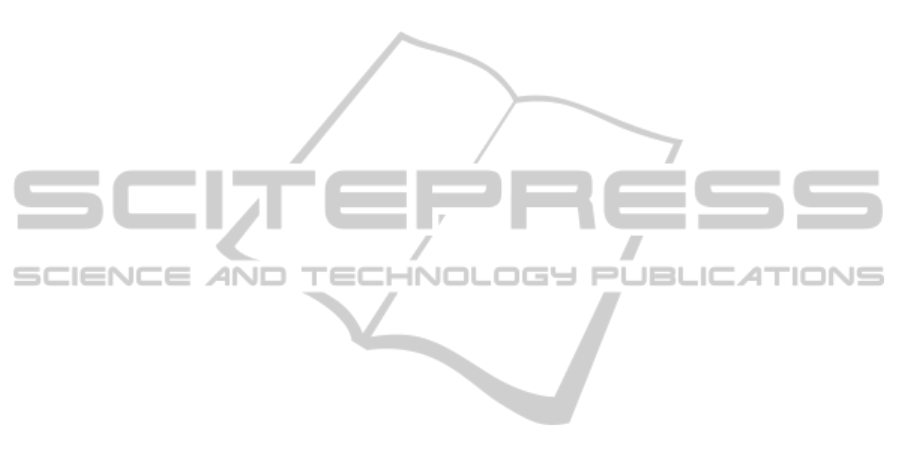
SKUs are vital for companies operations there
should be a separate inventory management policy.
Future research should validate the framework and
include any necessary adjustments. It is also
important to establish the periodicity for revising the
framework. It could also be of interest to apply the
same framework to other types of organizations and
contexts.
REFERENCES
Bacchetti, A., Plebani, F., Saccani, N., & Syntetos, A.
(2013). Empirically-driven hierarchical classification
of stock keeping units. Int. J.Production Economics,
143, 263–274.
Baker, T., & Jayaraman, V. (2012). Managing information
and supplies inventory operations in a manufacturing
environment. Part 1: An action research study.
International Journal of Production Research, 50(6),
1666-1681.
Bošnjaković, M. (2010). Multicriteria inventory model for
spare parts. Tehnički vjesnik, 17 (4), 499-504.
Botter, R., & Fortuin, L. (2000). Stocking strategy for
service parts–a case study. International Journal of
Operations & Production Management, 20(6), 656-
674.
Braglia, M., Grassi, A., & Montanari, R. (2004). Multi-
attribute classification method for spare parts
inventory management. Journal of Quality in
Maintenance Engineering, 10(1), 55-65.
Cavalieri, S., Garetti, M., Macchi, M., & Pinto, R. (2008).
A decision-making framework for managing
maintenance spare parts. Production Planning &
Control, 19(4), 379-396.
Childerhouse, P., Aitken, J., & Towill, D. R. (2002).
Analysis and design of focused demand chains.
Journal of Operations Management, 20(6), 675-689.
D'Alessandro, A. J., & Baveja, A. (2000). Divide and
conquer: Rohm and Haas' response to a changing
specialty chemicals market. Interfaces, 30(6), 1-16.
Duchessi, P., Tayi, G. K., & Levy, J. B. (1988). A
conceptual approach for managing of spare parts.
International Journal of Physical Distribution &
Logistics Management, 18(5), 8-15.
Flores, B. E., & Whybark, D. C. (1986). Multiple criteria
ABC analysis. International Journal of Operations &
Production Management, 6(3), 38-46.
Flores, B. E., & Whybark, D. C. (1987). Implementing
multiple criteria ABC analysis. Journal of Operations
Management, 7(1), 79-85.
Flores, B. E., Olson, D. L., & Dorai, V. K. (1992).
Management of multicriteria inventory classification.
Mathematical and Computer Modelling, 16(12), 71-
82.
Heinecke, G., Syntetos, A. A., & Wang, W. (2013).
Forecasting-based SKU classification. International
Journal of Production Economics, 143(2), 455-462.
Huiskonen, J. (2001). Maintenance spare parts logistics:
special characteristics and strategic choices.
International Journal of Production Economics, 71
(1–3), 125–133.
Jouni, P., Huiskonen, J., & Pirttilä, T. (2011). Improving
global spare parts distribution chain performance
through part categorization: A case study.
International Journal of Production Economics,
133(1), 164-171.
Molenaers, A., Baets, H., Pintelon, L., & Waeyenbergh,
G. (2012). Criticality classification of spare parts: A
case study. Int. J. Production Economics, 140, 570–
578.
Ramanathan, R. (2006). ABC inventory classification with
multiple-criteria using weighted linear optimization.
Computers & Operations Research, 33 (3), 695-700.
Saaty, T. L. (1980). The analytic hierarchy process:
planning, priority setting, resources allocation. New
York: McGraw.
Sexton, M., & Lu, S. L. (2009). The challenges of creating
actionable knowledge: an action research perspective.
Construction Management and Economics, 27(7), 683-
694.
Soylu, B., & Akyol, B. (2014). Multi-criteria inventory
classification with reference items. Computers &
Industrial Engineering, 69, 12–20.
Susman, G. I., & Evered, R. D. (1978). An assessment of
the scientific merits of action research. Administrative
Science Quarterly, 23(4), 582-603.
Syntetos, A. A., & Boylan, J. E. (2005). The accuracy of
intermittent demand estimates. International Journal
of Forecasting, 21(2), 303-314.
van Kampen, T. J., Akkerman, R., & van Donk, D. P.
(2012). SKU classification: A literature review and
conceptual framework. International Journal of
Operations & Production Management, 32(7), 850-
876.
ICORES2015-InternationalConferenceonOperationsResearchandEnterpriseSystems
418