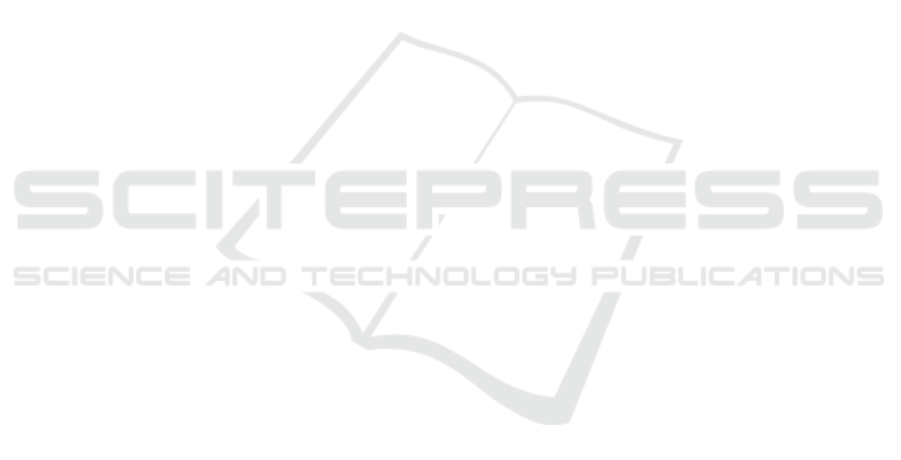
The Design, Performance and CFD Analyses of Regenerative Blower
used for Fuel Cell System
Chan Lee and Hyun Gwon Kil
Department of Mechanical Engineering, University of Suwon, Hwaseong, Korea
Keywords: Regenerative Blower, Design, Performance, CFD.
Abstract: For efficient design of regenerative blower used for fuel cell system, the design and the performance
analysis methods of regenerative blower are developed, and CFD modelling and simulation are carried out
on the designed blower. The design process of regenerative blower is conducted to determine the geometries
of rotating impellers and stationary side channel with several design variables. The performance analysis on
the designed blower is made by incorporating momentum exchange theory between impellers and side
channel with mean line analysis method, and its pressure loss and leakage flow models are constructed from
related fluid mechanics data and correlations which can be expressed in terms of blower design variables.
The internal flow field of blower is analysed by using the CFX code, a CFD code specialized for fluid
machinery. The present performance analysis method is applied to four existing models for verifying its
prediction accuracy, and the comparison between the prediction and the test results are well-agreed with a
few percentage of relative error. Furthermore, the present design and performance analysis methods are also
applied in developing a new blower used for fuel cell application, and the newly designed blower is
manufactured and tested through chamber-type test facility. The performance prediction by the present
method is well-agreed with the test and the CFD simulation results. Therefore, from the comparison results,
the prediction design and performance analysis methods are shown to be suitable for the actual design
practice of regenerative blower.
1 INTRODUCTION
Regenerative blowers are usually operated with high
pressure rise at low flow capacity, so widely used
for air/ hydrogen supply in fuel cell applications.
However, because regenerative blowers are
operating with low efficiency or a lot of pressure
loss (Badami and Mura, 2012), there are growing
industrial needs for high-efficiency regenerative
blower development. Since the pressure loss is
strongly dependent on the internal flow phenomena
of regenerative blower, for developing high-
efficiency blower, reliable design method with
accurate performance analysis model considering the
flow effects should be developed and applied to
actual design practice of blower industries.
The early theoretical researches on regenerative
blower and pump have been conducted to investigate
the flow pattern and the energy transfer mechanism
of fluid inside the machines, and showed that the
energy transfer to fluid is achieved by the
momentum exchange of the helical-torodal fluid
motion between rotating impeller and fixed side
channel of regenerative machine (Wilson et al.,
1955: Hollenberg and Porter, 1979). Recent
researches by Badami and Mura have been devoted
to improving the performance analysis method of
regenerative blower by using momentum exchange
theory, and the prediction results have been
compared and well-agreed with test and 3-D CFD
results. However, since their analysis model requires
model constants which user should specify, it needs
the generalization of the constants in terms of
blower design and operation parameters (Badami
and Mura, 2011: Badami and Mura, 2012). Lee et al.
proposed an analysis method for regenerative blower
performance by using momentum exchange theory,
and tried to generalize their model constants from
relevant regenerative blower and fluid mechanics
experimental results (Lee et al., 2013).
In the present study, a simple but reliable design-
analysis method of regenerative blower is developed
as in-house program called as the FANDAS-Regen
code. Regenerative blower performance is predicted
751
Lee C. and Gwon Kil H..
The Design, Performance and CFD Analyses of Regenerative Blower used for Fuel Cell System.
DOI: 10.5220/0005104007510755
In Proceedings of the 4th International Conference on Simulation and Modeling Methodologies, Technologies and Applications (SIMULTECH-2014),
pages 751-755
ISBN: 978-989-758-038-3
Copyright
c
2014 SCITEPRESS (Science and Technology Publications, Lda.)