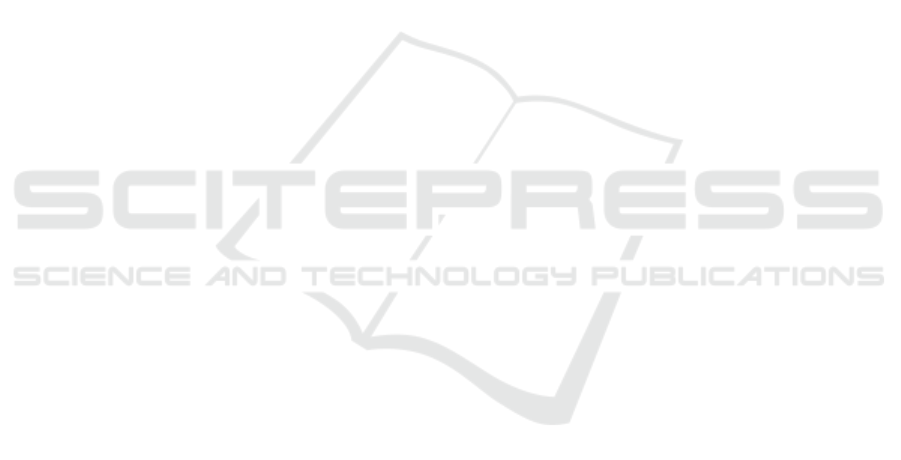
Active Vibration Control of a Super Element Model of a Thin-walled
Structure
Nader Ghareeb
1
and R¨udiger Schmidt
2
1
Department of Mechanical Engineering, Australian College of Kuwait, Kuwait City, Kuwait
2
Institute of General Mechanics, RWTH Aachen University of Technology, Aachen, Germany
Keywords:
Super Element, Lyapunov Stability Function Controller, Positive Position Feedback, Strain Rate Feedback.
Abstract:
Reducing vibration in flexible structures has become a pivotal engineering problem and shifted the focus of
many research endeavors. One technique to achieve this target is to implement an active control system. A
conventional active control system is composed of a vibrating structure, a sensor to perceive the vibration,
an actuator to counteract the influence of disturbances causing vibration, and finally a controller to generate
the appropriate control signals. In this work, different linear controllers are used to attenuate the vibrations
of a cantilevered smart beam excited by its first eigenmode. A finite element (FE) model of the smart beam
is initially created and then modified by using experimental data. The FE model is then reduced to a super
element (SE) model with a finite number of degrees of freedom (DOF). Controllers are applied directly to the
SE and the results are presented and compared.
1 INTRODUCTION
In modern engineering, weight optimization has a pri-
ority during the design of structures. However, opti-
mizing the weight results in lower stiffness and less
internal damping, causing the structure to become ex-
cessively prone to vibration. Vibration can lead to
additional noise, a decrease in stability, and even to
the failure of the structure itself (Ghareeb and Radov-
cic, 2009). To overcome this problem, active or smart
materials are implemented. The coupled electrome-
chanical properties of smart materials, which are il-
lustrated here in the form of piezoelectric ceram-
ics, make these smart materials well-suited for be-
ing used as distributed sensors and actuators for con-
troling structural response. Although the piezoelec-
tric effect was first mentioned by Ha¨uy in 1817 and
demonstratedby Pierre and Jacques Curie in 1880, the
use of piezoelectric materials as actuators and sensors
for noise and vibration control has only been demon-
strated extensively over the past thirty years (Piefort,
2001). Bailey (Bailey, 1984) designed an active vibra-
tion damper for a cantilever beam using a distributed
parameter actuator consisting of a piezoelectric poly-
mer. Bailey and Hubbard (Bailey and Jr., 1985) de-
veloped and implemented three different control algo-
rithms to control the cantilevered beam vibration with
piezoactuators. Further, Crawley and de Luis (Craw-
ley and de Luis, 1987) and Crawley and Anderson
(Crawley and Anderson, 1990) presented a rigorous
study on the stress-strain-voltage behaviour of piezo-
electric elements bonded to beams. They observed
that the effective moments resulting from piezoactu-
ators can be regarded as concentrated at both ends of
the actuator while assuming a very thin bonding layer.
The practical implementation and use of the
piezoelectric actuators has been investigated in stud-
ies such as (Fanson and Chen, 1986) and (Moheimani
and Fleming, 2006). This work emphasizes the ca-
pabilities and applications of piezoelements as dis-
tributed vibration actuators and sensors by simulta-
neously controling a finite number of the infinite set
of modes of the actual system. On the other hand,
the majority of investigations were carried out ei-
ther through experiments on the real model as in
(Waghulde et al., 2010),(Block and Strganan, 1998),
or by using 2D or 3D FE models of the smart struc-
ture as in (Varadan et al., 1996),(Allik and Hughes,
1970). However, in the FE work, the damping coeffi-
cients were not calculated but rather assumed, which
may not reflect the exact performance of the real
model.
The present work comprises the modeling and de-
sign of different active linear controllers to attenu-
ate the vibration of a cantilevered smart beam excited
by its first eigenmode. The piezoactuator is initially
657
Ghareeb N. and Schmidt R..
Active Vibration Control of a Super Element Model of a Thin-walled Structure.
DOI: 10.5220/0005027206570664
In Proceedings of the 11th International Conference on Informatics in Control, Automation and Robotics (ICINCO-2014), pages 657-664
ISBN: 978-989-758-039-0
Copyright
c
2014 SCITEPRESS (Science and Technology Publications, Lda.)