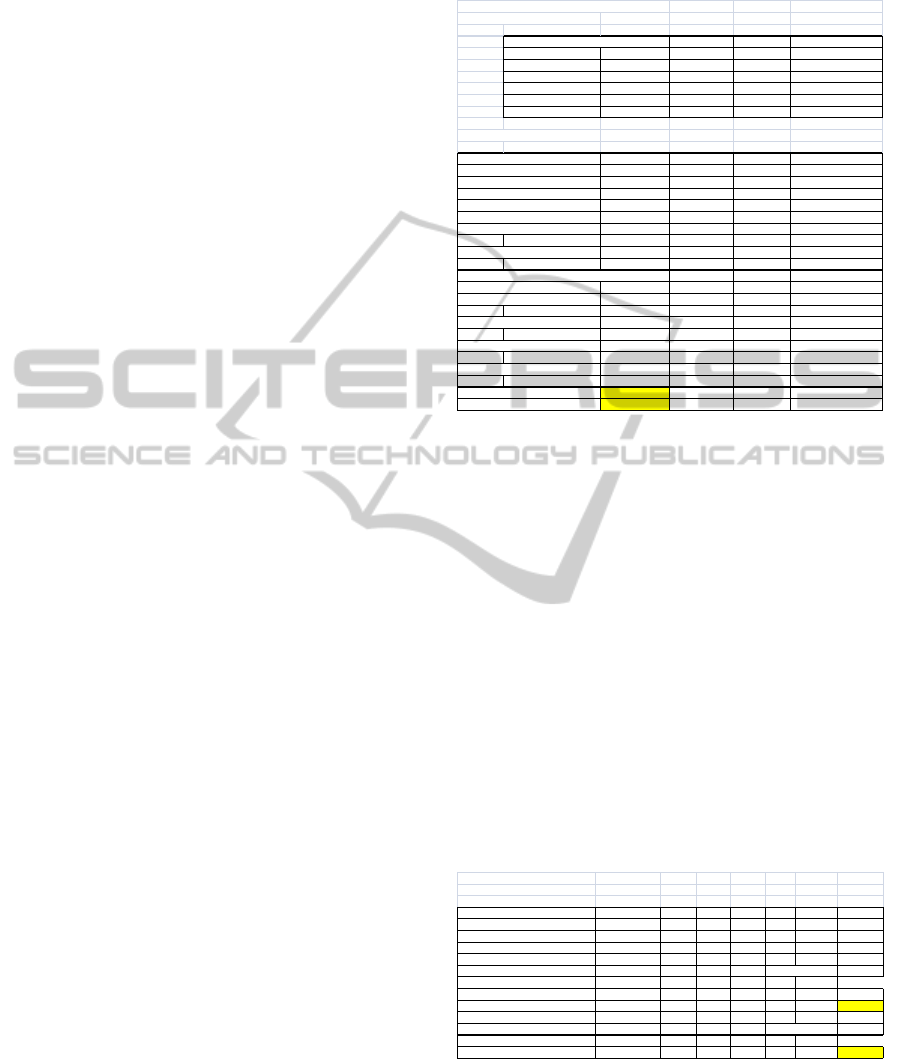
fleet represents a 10% fleet reduction. The proposed
model assumes an hourly labor rate of $20 for the
handlers and $25 for the maintenance crew. The
inflation and discount rates are 1.90% and 7.00%,
respectively. The annual material handlers’ savings
in cost is calculated to be $228,800 while the
maintenance crew, at 50 hours per vehicle per year
will generate a saving of $6,250 per year.
Under this model, with an initial capital
investment of $157,667 over a three year life (from
2014 to 2016), the Net Present Savings would be of
$279,357 with a Return On Investment (ROI) of
121.7%. These encouraging results could be
extrapolated to the particular case of Down Town
Press Inc. and lead to promising savings on
operational cost
6 CONCLUSIONS: EXPECTED
RESULTS AND PROJECTED
IMPROVEMENTS
The total capital investment to install the proposed
three vehicle mount computers (VMCs) on the
forklifts is approximately $15,400. The proposed
equipment will lead to an impressive Return On
Investment of 189%. The reduction of paper usage
will be gradual and departmental. The first area to
be targeted is the envelope presses in which the most
waste is currently occurring. The use of pick lists for
issuing stock will be reduced one stock item at a
time to reduce the risk of complete system failure
and to allow changes to procedures.
Additional savings would be generated by
integrating a fleet management system that would
subsequently reduce the fleet size as increased
productivity will be generated through the other
proposed changes. It has been proposed a gradual
addition of the electronic transducers to the material
handling equipment through FFMS as savings are
generated from other areas. Initial investment could
be in the range of $157,667 for a fleet size of 50
vehicles including support and training.
At the time of completion of this paper, only a
partial implementation of the proposed solutions was
underway at slow pace, justified in part by
temporary economical and financial issues at Down
Town Press Inc. coupled with a level of uncertainty
in the chaotic market exchange and a certain dose of
fear and skepticism from the management.
However, the company management has
recognized the merit and benefits of the study
including i) an actual realization of an accurate real-
Table 1: Cash Flow Analysis of Hypothetical
Implementation of Fleet Management.
FleetManagementSystem CashFlowAnalysis
HypotheticalCase
Inflation/DiscountFactors:
Inflationrate ‐ Labor 1.9%
Inflationrate ‐ other 1.4%
Discountrate 7.00%
012Total
EndofYear 2014 2015 2016
Inve stm e nt
1.Hardware‐ Site ($100,000) ($100,000)
2.InstallationManagement $0 $0
3.Hardware‐ Spares ($33,333) ($33,333)
4.Contractedsitepreparations $0 $0
5.SharedProgramCosts ($10,000) ($10,000)
Contingency(10% ) ($14,333) ($14,333)
TotalCapitalInve stm ent ($157,667) ($157,667)
OperatingVariances
EndofYear 2014 2015 2016
4.ManualHandlerLabor
savings $233,147 $237,577 $470,724
5.Maintenancelaborsavings $6,369 $6,490 $12,859
TotalOperatingVariances $239,516 $244,067 $483,583
NetCashFlow(Undiscounted) ($157,667) $239,516 $244,067 $325,916
DiscountFactor(@8.6% ) 1.0000 0.9346 0.8734
DiscountedCashFlow ($157,667) $223,847 $213,177 $279,357
Netpresentvalue@ 8.6%: $279,357
Returnoninvestment: 121.7%
time stock information through the use of VMCs, ii)
a more organized work floor as the result of 5S
implementation, iii) an appropriate and accurate
inventory tracking of stock levels due to the
combination of forecasting models and kanban
signals, iv) and a higher personnel productivity as a
consequence of manpower utilization improvement
and enhanced skills and motivation from training.
This study shows a possible reduction of
$300,000 in the yearly operating capital and the
perspective of an extremely high and appealing cost
saving from material handling, due to a proposed
10% reduction of the current fleet size as the result
of the integration of a comprehensive fleet
management system as depicted in the scenarios in
Tables 1 and 2.
Table 2: Potential Savings Under Fleet Proposed 10%
Fleet Reduction 50 Vehicles vs. 45.
ExampleofProductivityEnhancementUsing
ForkliftFleetManagementSystem(FFMS)
Inventory Current Proposed Change
Forklifts 22 20 ‐2
Ridi ngJacks 28 25 ‐3
TOTALS 50 45 ‐5
Days/Year:
Mat eri al aHandler 286
Mai l HandlerStaffing Current Proposed Change Hours FY14Rate DailySavings AnnualSaving
8hourShift 0 0 0 8 $20.00 $160 $45, 760
Total 50 45 ‐5 ‐40 ‐$800 ‐$228,800
MaintenanceOperator
MaintenanceSavings CurrentMHECount Proposed Change Hours FY14Rate AnnualSaving
At50hrsperunitperyear 50 45 ‐5 ‐250 $25.00 ‐$6,250
It worth it to note that this improvement and the
subsequently derived monetary savings were
achieved by solely considering four items and by
maintaining them at the right stock level in a factory
that contains thousands of such items. If, in addition,
ICINCO2014-11thInternationalConferenceonInformaticsinControl,AutomationandRobotics
706