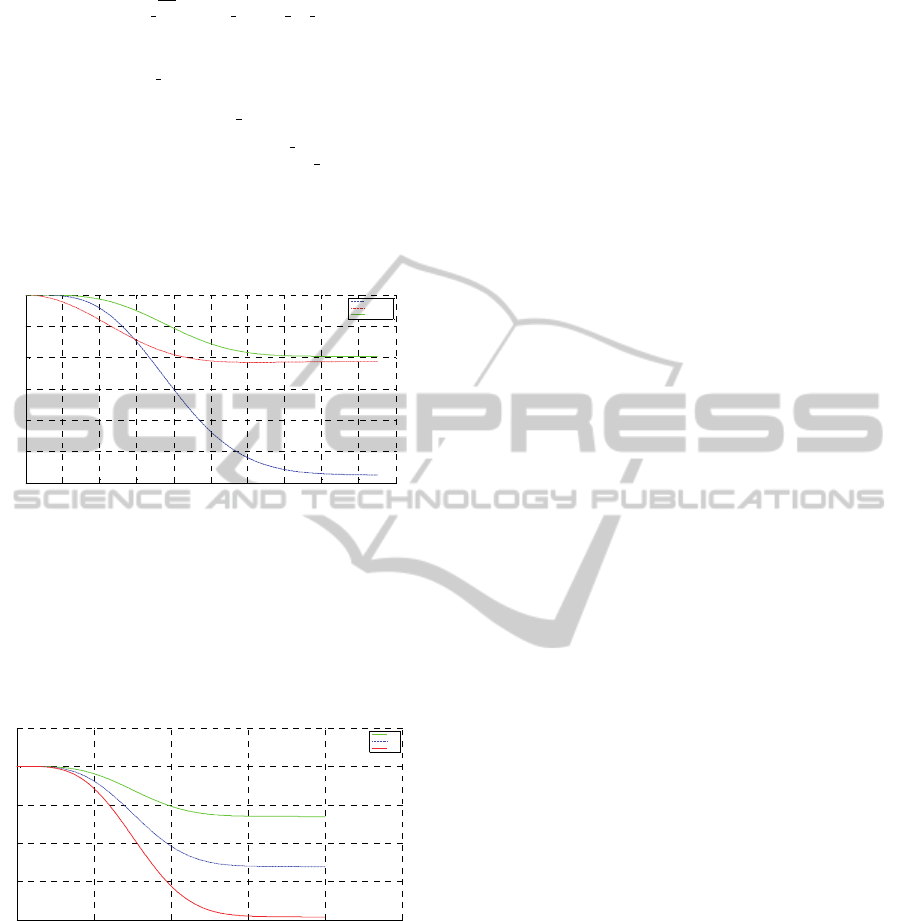
60000
00
0
650000000000
024000000000
020400000000
00040000000
0020
000000
0 0 2 2 4 0 3 0 0 0 0 0
00000020000
00000002
000
00000000300
000000003
0
0000000000
)
(3)
In Figure 9 the comparison among the availability
simulations of the three mentioned configurations
supposing to have a repair rate of 1/48 [1/h] is
sketched.
Figure 9: Availability comparison of the three
configurations considering 48h as the inverse of the repair
rate µ.
Out of the analysis it is evident that the best
configuration representing a reasonable choice
among the three proposed is the 2oo6 + 3
consecutive failures due to the fact that it shows the
best steady state availability behaviour.
Figure 10: Availability behaviour of the 2oo3+3
consecutive failures configuration considering 16, 32 and
48h as the inverses of three different repair rates µ.
Availability modification according to different
repair rates (16, 32 and 48 hours respectively) are
investigated and results are shown in Figure 10.
4 CONCLUSIONS
In this paper the authors propose three different
configurations to evaluate the reliability and
availability of the disposition of six thermoelements
used to monitor the exhaust temperature in a gas
turbine system to enhance system productivity and
efficiency performance over time. The study has
been performed exploiting both RBD and Markov
state flow modelling under the hypothesis of
constant failure and repair rates. Results pointed out
that the best configuration is the 2oo6 + 3
consecutive both in terms of reliability and
availability.
REFERENCES
Hua D., Yang X. H., 2011, Reliability Analysis of Gas
Turbine Based on the Failure Mode and Effect
Analysis Power and Energy Engineering Conference
(APPEEC), Asia-Pacific.
Mugnaini M., Catelani M., Ceschini G., Masi A.,
Nocentini F., 2002, Pseudo Time-Variant parameters
in centrifugal compressor availability studies by means
of Markov models in Microelectronics Reliability, vol.
42, p. 1373-1376, ISSN: 0026-2714.
Chowdhury, A. A., Koval, D. O. 2009, Reliability
Assessment of a Backup Gas Turbine Generation
System for a Critical Industry Load Using a Monte
Carlo Simulation Model Industry Applications, IEEE
Transactions on Volume:45, Issue : 1
10.1109/TIA.2008.2009495, Page(s): 310 – 316.
Ceschini G., Mugnaini M., Masi A., 2002, A reliability
study for a submarine compression application
Microelectronics Reliability, vol. 42, p. 1377-1380,
issn: 0026-2714.
Rao S. S., 2005, Reliability engineering Design McGraw
Hill.
Birolini A., 2010, Reliability Engineering: Theory and
Practice Springer 6th Edition 2010.
Fort A., Bertocci F., Mugnaini M., Vignoli V., Gaggii V.,
Galasso A., Pieralli M., 2013, Availability modeling
of a safe communication system for rolling stock
applications Conference Record - IEEE
Instrumentation and Measurement Technology
Conference , art. no. 6555453 , pp. 427-430.
Catelani M., Mugnaini M., Singuaroli R., 2000, Effects of
test sequences on the degradation analysis in high
speed connectors Microelectronics Reliability, vol. 40,
p. 1461-1465, ISSN:0026-2714.
Catelani M., Ciani L., Mugnaini M., Scarano V.,
Singuaroli R., 2007, Definition of safety levels and
performances of safety: Applications for an electronic
equipment used on rolling stock IEEE Instrumentation
and Measurement Technology Conference, art. no.
4258348, IMTC.
0 200 400 600 800 1000 120 0 1400 1600 18 00 20
0.9994
0.9995
0.9996
0.9997
0.9998
0.9999
1
time (h)
Availability(t)
4006
3006+2cons
2006+3cons
0 500 1000 1500 2000 250
0.9998
0.9998
0.9999
0.9999
1
1
time (h)
Availability(t)
mu1
mu2
mu3
SMARTGREENS2014-3rdInternationalConferenceonSmartGridsandGreenITSystems
100