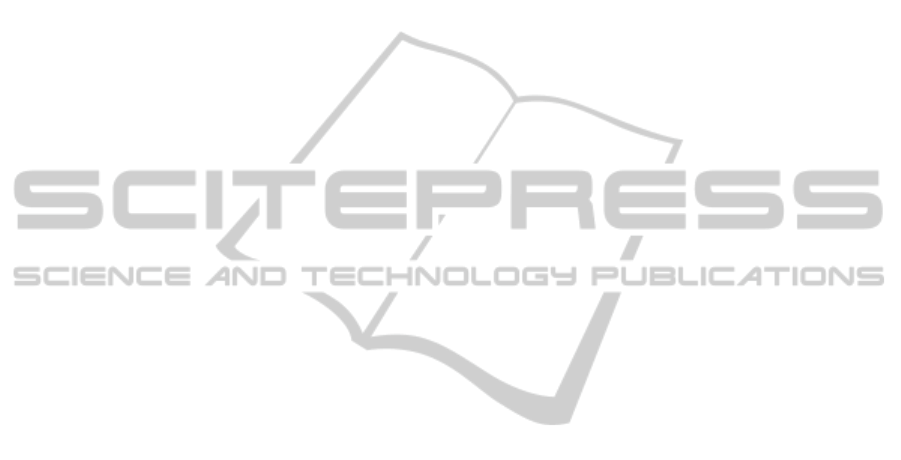
estimation results compared to the current approach
utilizing lumped mass model. This means that this
model offers a major advantage of capturing friction
force at area near zero velocity, i.e. when the system
stops, and guarantees a smooth transition from
presling to sliding regimes. Moreover, at small
displacement, the friction force changes very
rapidly. The proposed model can track quite well in
this case as shown in Figure 6 and 7.
5 CONCLUSIONS
This paper has introduced a new dynamic friction
model to solve the haptic feedback problems for
flexible endoscopic system using tendon sheath
mechanism. The proposed model incorporates
acceleration and velocity information in the sliding
regime and uses a modification of the Dahl dynamic
friction model to capture the hysteresis for both
presliding and sliding regimes. The new model can
give a smooth transition between the two regimes
(sliding and presliding regimes) and is capable of
prediction friction near zero velocity.
Validation experiments have been carried out to
evaluate the proposed model. An efficient
identification method (Genetic Algorithm) has firstly
used to generate a rough initial guess of model
parameters. The obtained results have been refined
using the Nelder-Mead Simplex Method. The
comparisons between the proposed model and the
experiment data have shown a good agreement for
the approach. It can be concluded that the proposed
model promises an efficient approach not only in
accurately predicting the force for haptic feedback
but also in any surgical devices that have similar
friction characteristics as the tendon sheath.
Future activities will be conducted by developing
the experimental setup for a pair of tendon sheath
and the proposed model to adapt to any
configuration of the sheath. A hysteresis
compensation for both position and friction force
feedback will be also developed using suitable
nonlinear control schemes and taking into
consideration for higher degrees of freedom in the
system.
REFERENCES
Agrawal, V., Peine , W. J., et al. (2010). "Modeling of
Transmission Characteristics Across a Cable-Conduit
System." Robotics, IEEE Transactions on 26(5): 914-
924.
Agrawal, V., Peine, W. J. , et al. (2008). "Modeling of a
closed loop cable-conduit transmission system".in
Proc. IEEE Int. Conf. Robot. Autom.,Pasadena, CA,
pp. 3407–3412.
Al-Bender, F., Lampaert, V., et al. (2005). "The
generalized Maxwell-slip model: a novel model for
friction Simulation and compensation." Automatic
Control, IEEE Transactions on 50(11): 1883-1887.
Armstrong-Hélouvry, B., Dupont , P., et al. (1994). "A
survey of models, analysis tools and compensation
methods for the control of machines with friction."
Automatica 30(7): 1083-1138.
Bodner, J., Wykypiel , H., et al. (2004). "First experiences
with the da Vinci™ operating robot in thoracic
surgery." European Journal of Cardio-Thoracic
Surgery 25(5): 844-851.
Canudas de Wit, C., Olsson , H., et al. (1995). "A new
model for control of systems with friction." Automatic
Control, IEEE Transactions on 40(3): 419-425.
Dahl, P. R. (1968). "A solid friction model." Aerospace
Corp. El Segundo CA: 31.
Förster, R., Storck , M., et al. (2002). "Thoracoscopy
versus thoracotomy: a prospective comparison of
trauma and quality of life." Langenbeck's Archives of
Surgery 387(1): 32-36.
Kaneko, M., Wada , M., et al. (1991). "A new
consideration on tendon-tension control system of
robot hands. " in Proc. Int. Conf. Robot. Autom., vol.
2, Kyoto, Japan, pp. 1028–1033.
Kaneko, M., Yamashita , T., et al. (1991). "Basic
considerations on transmission characteristics for
tendon drive robots. " in Proc. Int. Conf. Adv. Robot.,
vol. 1, Pisa, Italy, pp. 827–832.
Mitchell, M. (1996). Introduction to Genetic Algorithms,
MIT Press.
Nagahiro, I., Andou , A., et al. (2001). "Pulmonary
function, postoperative pain, and serum cytokine level
after lobectomy: a comparison of VATS and
conventional procedure." The Annals of Thoracic
Surgery 72(2): 362-365.
Palli, G., Borghesan , G., et al. (2009). "Tendon-based
transmission systems for robotic devices: Models and
control algorithms. " in Proc. Int. Conf. Robot. Autom.,
Kobe, Japan, pp. 4063–4068.
Palli, G., Borghesan , G., et al. (2012). "Modeling,
Identification, and Control of Tendon-Based Actuation
Systems." Robotics, IEEE Transactions on 28(2): 277-
290.
Palli, G. and Melchiorri , C. (2006). "Model and control of
tendon-sheath transmission systems. " in Proc. Int.
Conf. Robot. Autom., Orlando, FL, pp. 988–993.
Phee, S. J., Low , S. C., et al. (2010). "Tendon sheath
analysis for estimation of distal end force and
elongation for sensorless distal end." Robotica 28(07):
1073-1082.
Wojewoda, J., Stefanski , A., et al. (2008). "Hysteretic
effects of dry friction: modelling and experimental
studies." Philosophical Transactions of the Royal
Society London, Series A (Mathematical, Physical and
Engineering Sciences) 366(1866): 747-765.
ICINCO2013-10thInternationalConferenceonInformaticsinControl,AutomationandRobotics
10