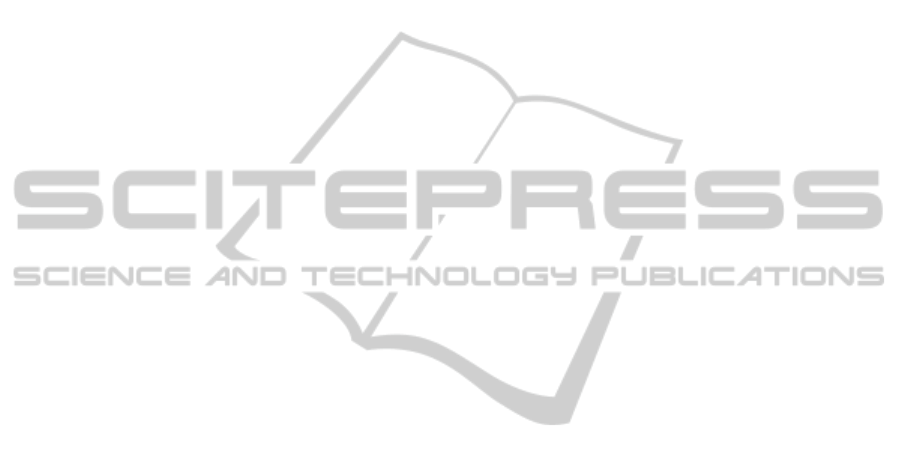
In addition, combining novel advances in micro-
CT and medical imaging software (i.e. Mimics,
Materialise NV) for obtaining precise CAD data of
organs and biostructures (Shi, 2008, Guo, 2010),
with the possibility of incorporating even
nanometric features in a similar way to the presented
study, can be of great help for research linked to
enhanced modelling of biosystems.
4 CONCLUSIONS
A novel method for defining and controlling the
topography of surfaces from the design stage, even
mimicking the characteristics of biological systems,
has been presented. It is based on the combination of
regular surfaces for describing the micrometric
structure and additional fractal components for
providing the final nanometric details. As
application example a biomimetic design of the
surface of the Lotus flower leaves has been
explained.
Manufacture of such complex geometries can be
directly accomplished with help of additive rapid
prototyping technologies, what supposes a focus
change, from a more conventional “top-down”
(micro-machining, chemical etching, laser ablation),
to a more versatile “bottom-up” approach. The
flexibility of additive manufacturing also enables the
application of similar surface microtextures to the
complex geometries of prostheses and biodevices,
thus helping to introduce beneficial contact
properties for enhancing aspects such as wear
endurance or biocompatibility.
REFERENCES
Mandelbrot, B. B. (1982). The Fractal Geometry of
Nature, W. H. Freeman and Company.
Falconer, K. (2003). Fractal Geometry: Mathematical
Foundations and Applications. John Wiley & Sons.
Tsyganov, M. A., Kresteva, I. B., Aslanidi, G. V.,
Aslanidi, K. B., Deev, A. R. and Ivanitsky, G. R.
(2007). The mechanism of fractal-like structure
formation by bacterial populations. Journal of
Biological Physics, 25, 165-176.
Lin, D. W., Johnson S. and Hunt, C. A. (2004). Modeling
liver physiology: Combining fractals, imaging and
animation. Proceedings of the 26th Annual
International Conference of the IEEE EMBS, 3120-
3123.
Longoni, S. and Sartori, M. (2010). Fractal geometry of
nature (bone) may inspire medical devices shape.
Nature Proceedings.
Barthlott, W. and Neinhuis, C. (1997). Purity of the sacred
lotus, or escape from contamination in biological
surfaces. Planta, 202, 1-8.
Groenendijk, M. (2007). Self cleaning Lotus leaf imitated
in plastic by using a femtosecond laser. Univ. Twente,
Source: www.physorg.com
Díaz Lantada, A., Lafont Morgado, P. et al. (2010a).
Substrato cuasibidimensional para crecimiento de
células y tejidos y método de obtención del mismo.
Spanish Patent and Trademark Office, Patent
application number P201030957.
Díaz Lantada, A., Mosquera, A. A., Endrino, J. L. and
Lafont, P. (2010b). Design and rapid prototyping of
DLC coated surfaces for tissue engineering
applications. Journal of Physics, Conference Series,
252, 012003.
Infür, R., Pucher, N., Heller, C., Lichtenegger, H., Liska,
R., Schmidt, V., Kuna, L., Haase, A. and Stampfl, J.
(2007). Functional polymers by two-photon 3D
lithography. Applied Surface Science, 254, 836-840.
Choi, J., Wicker, R., Lee, S. H., Choi, K. H., Ha, C. S. and
Chung, I. (2009). Fabrication of 3D biocompatible /
biodegradable micro-scaffolds using dynamic mask
projection microstereolithography. Journal of
Materials Processing Technology, 209, 5494-5503.
Stampfl, J., Schuster, M., Baudis, S., Lichtenegger, H., Liska,
R., Turecek, C. and Varga, F. (2007). Biodegradable
stereolithography resins with defined mechanical
properties. Proceedings VRAP 2007, 283-288.
Gad-el-Hak, M. (2002). The MEMS Handbook, CRC
Press.
Shi, H., Farag, A. A., Fahmi, R. and Chen, D. (2008).
Validation of finite element models of liver tissue
using micro-CT. IEEE Transactions on Biomedical
Engineering, 55, 978-985.
Guo, X., Liu, X., Wang, X., Tian, F., Liu, F., Zhang, B.,
Hu, G., and Bai, J. (2010). A combined fluorescence
and microcomputed tomography system for small
animal imaging. IEEE Transactions on Biomedical
Engineering, 58, 2876-2883.
BIODEVICES 2012 - International Conference on Biomedical Electronics and Devices
290