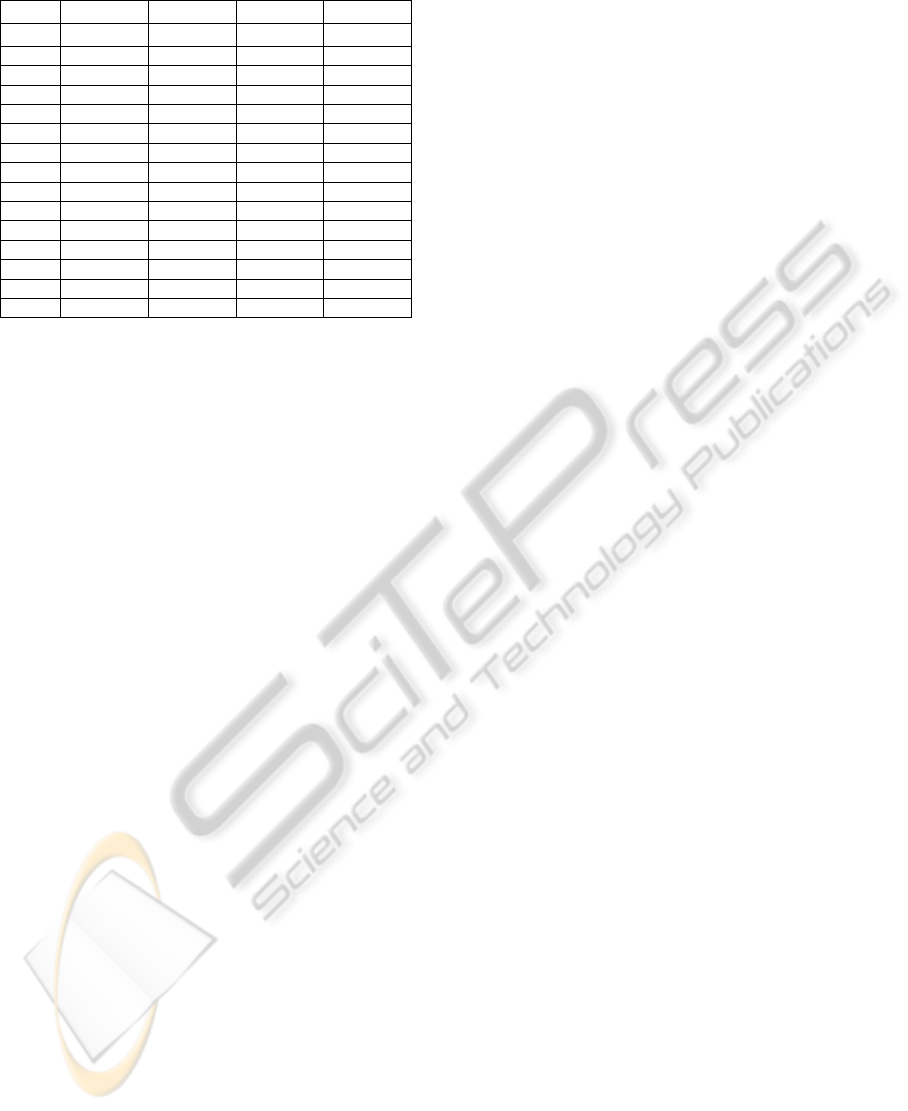
Table 2: Operation time of numerical example.
OP 1 OP2 Cycle Turns
1 Station 1 Station 2 53 2
2 Station 1 Station 3 61 3
3 Station 2 Station 3 53 2
4 Station 1 Station 4 56 3
5 Station 2 Station 4 61 3
6 Station 3 Station 4 53 2
7 Station 1 Station 5 58 3
8 Station 2 Station 5 56 3
9 Station 3 Station 5 61 3
10 Station 4 Station 5 53 2
11 Station 1 Station 6 70 2
12 Station 2 Station 6 58 3
13 Station 3 Station 6 56 3
14 Station 4 Station 6 61 3
15 Station 5 Station 6 53 2
The best average cycle time for assembly rotating
round table is 53 and it occurs always when
Operator 1 and Operator 2 are located next to other.
In this case we need to execute only two turns. The
final solution is: Operator 1 executes tasks 1 and 6
and Operator 2 executes tasks 2, 3, 4, 5, 7 and 8.
Additionally we can calculate the time when final
products is ready to unload from assembly system.
In our case the ready product leaves the system in
216 units of time. We should remember that
assembly rotating system is mostly effective in case
when product demand is equal to the total number of
stations.
7 CONCLUSIONS
In the paper two assembly systems were considered.
First assembly lines were presented. Next assembly
rotating round table was shown. The problems
seems interesting for low product demand. Known
procedures of solving balance of line structures
allow to get very easy optimal or near optimal
solution for two stations line. Investigated assembly
rotating round table allows to quick changes of
assembling different product. Heuristic procedure
improves the result of average cycle time from 70 to
53. This kind of assembly table takes benefits from
layout described in section 4 dealing with their
disadvantages such as monotony, boredom,
operators overload and communication. Different
measures of final result (smoothness index, line
efficiency, line time or average cycle time) simplify
the choice of the most appropriate solution. We
should underline that assembly rotating round table
system don’t need additional sequencing procedure.
Mixed product assembly deals with many
precedence relations but we choose only this one
with maximal number of tasks and connection.
Therefore we calculated the balance of whole model
with maximal task time operations. It allows to
choice appropriate cycle time of turn. In serial lines
we need to sequence the mix product model and
sometimes to stop the line (different model cycle
time) or to add additional parallel station.
This research was supported in part by grant of
Ministry of Science and Higher Education BK
209/Rau1/2009 t.5
REFERENCES
Aase, G. R., Olson, J. R., Schniederjans, M. J., 2004, U-
shaped assembly line layouts and their impact on labor
productivity: an experimental study, European
Journal of Operational Research, 156, 698–711
Askin, R. G., Zhou, M., 1997, A parallel station heuristic
for the mixed-model production line balancing
problem, International Journal of Production Research,
35(11), 3096-3106
Beker, C., Scholl, A., 2005, A survey on problems and
methods in generalized assembly line balancing,
European Journal of Operational Research, 168, 694–
715
Bartholdi J. J., 1993. Balancing two-sided assembly lines:
a case study, International Journal of Production
Research, 31(10), 2447-2461
Battini, D., Facio, M., Ferrari, E., Persona, A., Sgarbossa,
F., 2007, Design Configuration for a Mixed Model
Assembly System in Case of Low Product Demand,
The International Journal of Advanced Manufacturing
Technology, 34(1), 188-200.
Bukchin, J, Dar-El, M, Rubinovitz, J., 2002, Mixed model
assembly line design in a make-to-order environment,
Computers & Industrial Engineering, 41, 405-421
Heike, G., Ramulu, M., Sorenson, E., Shanahan, P.,
Moinzadeh., K, 2001, Mixed model assembly
alternatives for low-volume manufacturing: the case of
the aerospace industry, International Journal of
Production Economics, 72, 103-120
McMullen, P. R., 1997, A heuristic for solving mixed-
model line balancing problem with stochastic task
durations and parallel stations, International Journal
of Production Economics, 51(1), 77–190
Salveson, M. E., 1955. The assembly line balancing
problem, Journal of Industrial Engineering, 62-69
Scholl, A., 1998. Balancing and sequencing of assembly
line, Physica- Verlag
Sauer, G. A., 1998, Designing parallel assembly lines.
Computer Industrial Engineering, 35(3–4), 467–470
Sury, R. J., 1971. Aspects of assembly line balancing,
International Journal of Production Research, 9, 8-14
ICINCO 2010 - 7th International Conference on Informatics in Control, Automation and Robotics
264