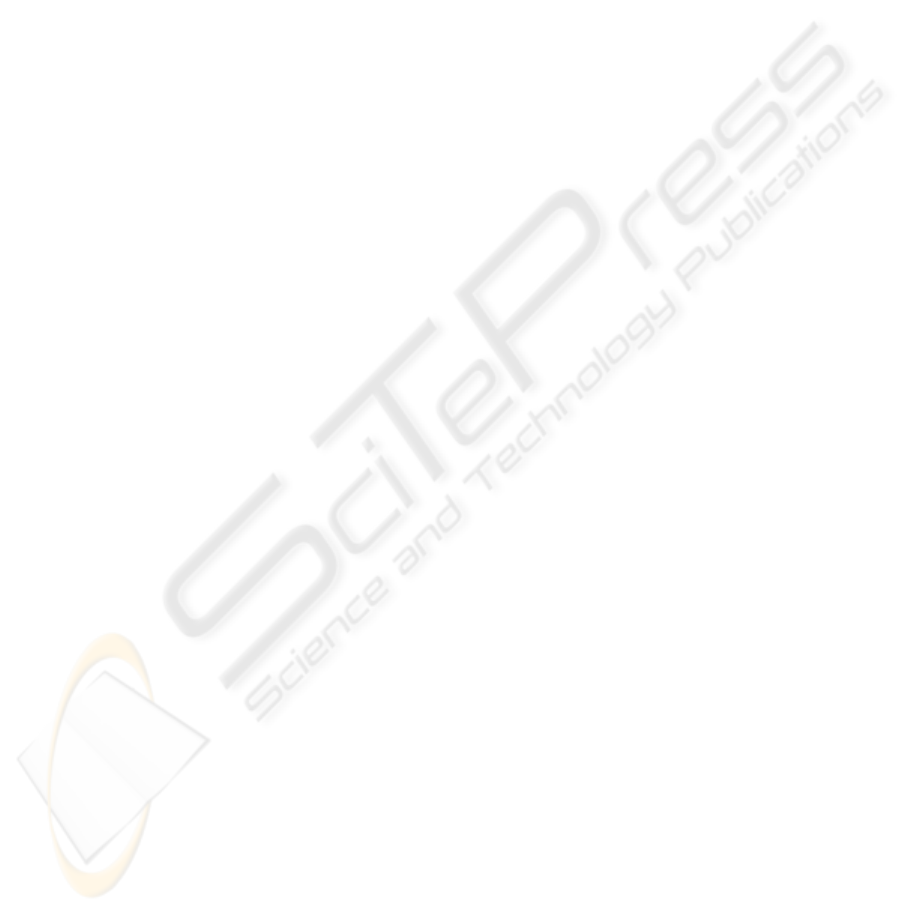
POLYISOPRENE – NANOSTRUCTURED CARBON COMPOSITE
(PNCC) MATERIAL FOR VOLATILE ORGANIC
COMPOUND DETECTION
Gita Sakale, Maris Knite, Valdis Teteris
Institute of Technical Physics, Riga Technical University, Azenes iela 14/24, Riga, Latvia
Velta Tupureina
Institute of Polymer Materials, Riga Technical University, Riga, Latvia
Keywords: Polymer-high structured carbon black composite, Volatile organic compound sensors.
Abstract: Our scientific group has chosen the elaboration of conductive composite material, which could be useful for
volatile organic compound detection, as one of research areas. It was found out that the most sensitive
composite material consists of polyisoprene and 10 mass parts of nanostructured carbon black. The electric
resistance changes of the composite in presence of 10 different saturated organic solvents vapour were
measured. Results obtained form our mass-sorption experiments indicated that electrical resistance of the
composite increases because of volatile organic compound (VOC) molecule absorption in the composite
matrix material. We also evaluated VOC compatibility with PNCC matrix material and estimated how the
PNCC resistance change velocity (
R
v ) versus organic solvent vapour molecule diameter varies.
1 INTRODUCTION
Available statistical data evidence about people
exposed to organic solvent daily at their workplaces,
but there are no monitoring devices used to control
VOC concentration in the room. There is also a
necessity to protect environment and equipment
from exposure to VOC. Above mentioned denotes
that there is an urgent need for VOC sensor
materials.
Devices (sorbent polymer films, metal oxide
semiconductors, quartz microbalance (quartz
resonator), laser gas sensors ect.) in the market can
not still be compared with mammal’s olfactory
system. Scientists are trying to design a prototype of
sensor which in sensing capability of different gases
could be close to mammals olfactory system and
even could be improved for practical applications.
We think that the desirable result of VOC
detection can be achieved by using polymer –
carbon black composites as gas sensor materials
because polymer matrix can be selected for direct
volatile compound detection and identifying.
In our opinion a candidate sensor material for gas
sensing should fulfil the following criteria: not
expensive constituent materials; simple production;
fast and reversible response; in-situ control of VOC;
small dimensions of sensing element and ability to
function for a long period of time.
The mechanism how polymer – carbon black
composite detects VOC is as fallows: i) the sample
of the composite material is exposed to VOC,
molecules of VOC adsorbe on the surface of
composite and diffuse into the matrix material; ii)
intermolecular chains in the polymer matrix weaken
and form intermolecular chains between VOC
molecules and macromolecules of matrix material;
iii) the matrix material swells; iv) electroconducting
pathways break down because distance between
carbon black aggregates increases; v) at the same
time tunnelling currents between carbon aggregates
in thin layers of matrix decreases and the electrical
resistance of the composite increases.
2 EXPERIMENTAL
Polyisoprene – nanostructured carbon composite
material was made by rolling highly structured nano-
size carbon black PRINTEX XE2 (specific surface
117
Sakale G., Knite M., Teteris V. and Tupureina V. (2009).
POLYISOPRENE – NANOSTRUCTURED CARBON COMPOSITE (PNCC) MATERIAL FOR VOLATILE ORGANIC COMPOUND DETECTION.
In Proceedings of the International Conference on Biomedical Electronics and Devices, pages 117-122
DOI: 10.5220/0001557301170122
Copyright
c
SciTePress