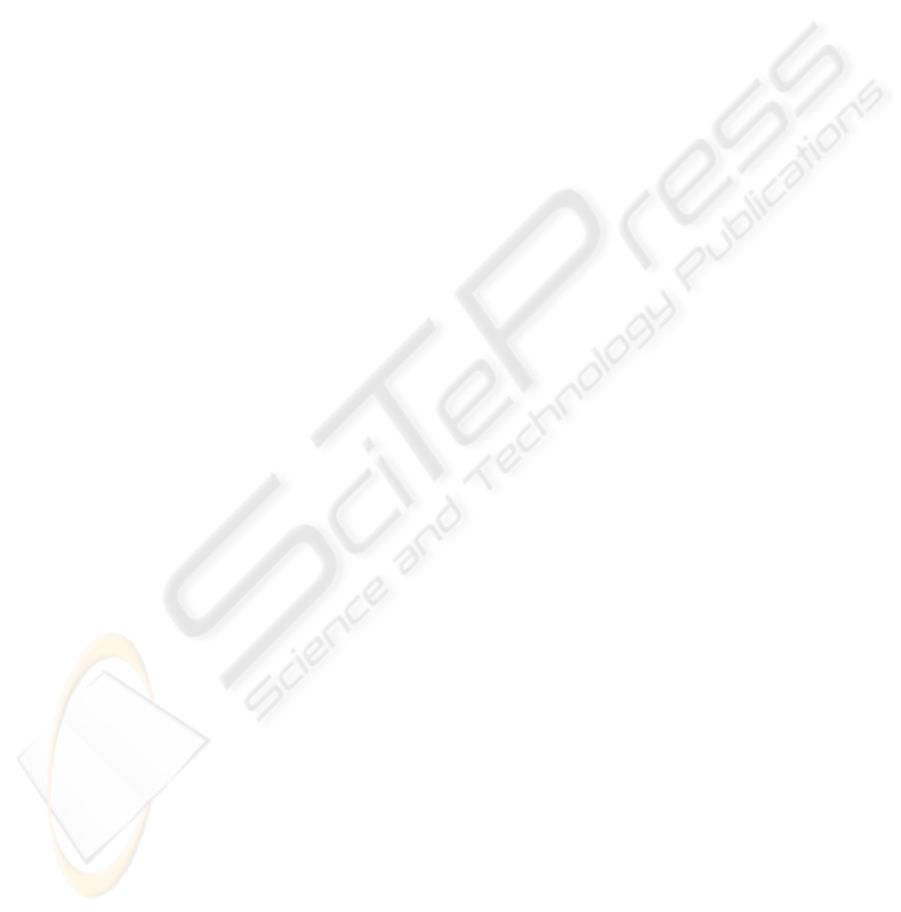
final stage of this task involves the correct
placement of a car lamp. As illustrated on the
bottom screenshot, both collision detection and force
feedback are visually displayed respectively using a
red colour and clear blue line (orientation of the
force).
5.2 Hardware and Software
Architecture
As opposed to most of the existing virtual reality
human-scale platforms that are based on clusters,
our hardware architecture is based on only one
Personal Computer (bi-Xeon 5150, 4Go RAM and
8800 GTX Graphic board).
The frame rate is however, in the described
application (600 000 Faces), maintained to about 30
frames per second. Thus, the use of a physical
Processing Unit is not necessary.
6 CONCLUSIONS AND FUTURE
WORK
We presented and validated a new methodology for
the efficient integration of CAD models in a
physical-based virtual reality simulation. User
interacts with virtual mock-up using a string-based
haptic interface that may provides haptic sensation
two both hands in a large workspace. Visual and
haptic displays provide users with sensory feedback
and improve both user performance and immersion.
Stereoscopic images are displayed on a 2m x 2.5m
retro-projected screen and viewed using polarized
glasses. The proposed methodology has been tested
with an automotive application task. However, the
presented approach is general enough to be
applicable to other tasks and industrial applications.
In the next future we plan to add a virtual hand
with physical properties to allow dexterous
manipulation of 3D objects. We will also replace the
magnetic tracking system by an optical MOCAP
solution. We will also use our methodology for other
CAD applications.
ACKNOWLEDGEMENTS
The authors would like to thanks the representative
of Valeo Lighting System (Angers - france) involved
in the project, especially Sébastien DENIS and
Xavier GALLARD.
REFERENCES
L. Bouguila, M. Ishii and M. Sato, “Multi-Modal Haptic
Device for Large-Scale Virtual Environment”, 8 th
ACM International Conference on Multimedia, 2000.
C. Cruz-Neira, D. Sandin, and T. Defanti, “Surround
Screen Projection Based Virtual Reality”. Proceedings
of SIGGRAPH, 1993.
W. Krueger and B. Froehlich, “The Responsive
Workbench”, IEEE Computer Graphics and
Applications, 1994.
P. Richard, D. Chamaret, F.-.X, Inglese, P. Lucidarme J.-L
Ferrier: Human-Scale Haptic Virtual Environment for
Product Design: Effect of Sensory Substitution.
International Journal of Virtual Reality, 2006, 5(2):
pp. 37-44.
T. H. Massie and J. K. Salisbury, “The PHANTOM Haptic
Interface: A Device for Probing Virtual Objects”,
Proceedings of the ASME Winter Annual Meeting,
Symposium on Haptic Interfaces for Virtual
Environment and Teleoperator Systems , 1994.
J.D. Brederson, M. Ikits, C.R. Johnson, C.D. Hansen, and
J.M. Hollerbach, “The Visual Haptic Workbench”,
Proceedings of the Fifth PHANToM Users Group
Workshop, 2000.
B. Grant and A. Helser, “Adding Force Display to a
Stereoscopic Head-Tracked Projection Display”,
VRAIS, 1998.
P. Garrec, J.P. Friconneau and F. Louveau, “Virtuose 6d:
A New Industrial Master Arm using Innovative Ball-
Screw Actuators”, Proc. of International Symposium
on Robotics, 2004.
N. Tarrin, S. Coquillart, S. Hasegawa, L. Bouguila, and M.
Sato, “The Stringed Haptic Workbench : a New Haptic
Workbench Solution”, EUROGRAPHICS Proceedings,
2003.
M. Ishii and M. Sato. “A 3d Spatial Interface Device using
Tensed Strings”, Presence, 3(1), 1994.
S. Coquillart and G.Wesche, “The Virtual Palette and the
Virtual Remote Control Panel: A Device and an
Interaction Paradigm for the Responsive Workbench.
Proc IEEE VR, 1999.
K. Hinckley, R. Pausch, J. Goble, and N. Kassell, “Passive
Real-World Interface Props for Neurosurgical
Visualization”, CHI, 1994.
ICINCO 2008 - International Conference on Informatics in Control, Automation and Robotics
310