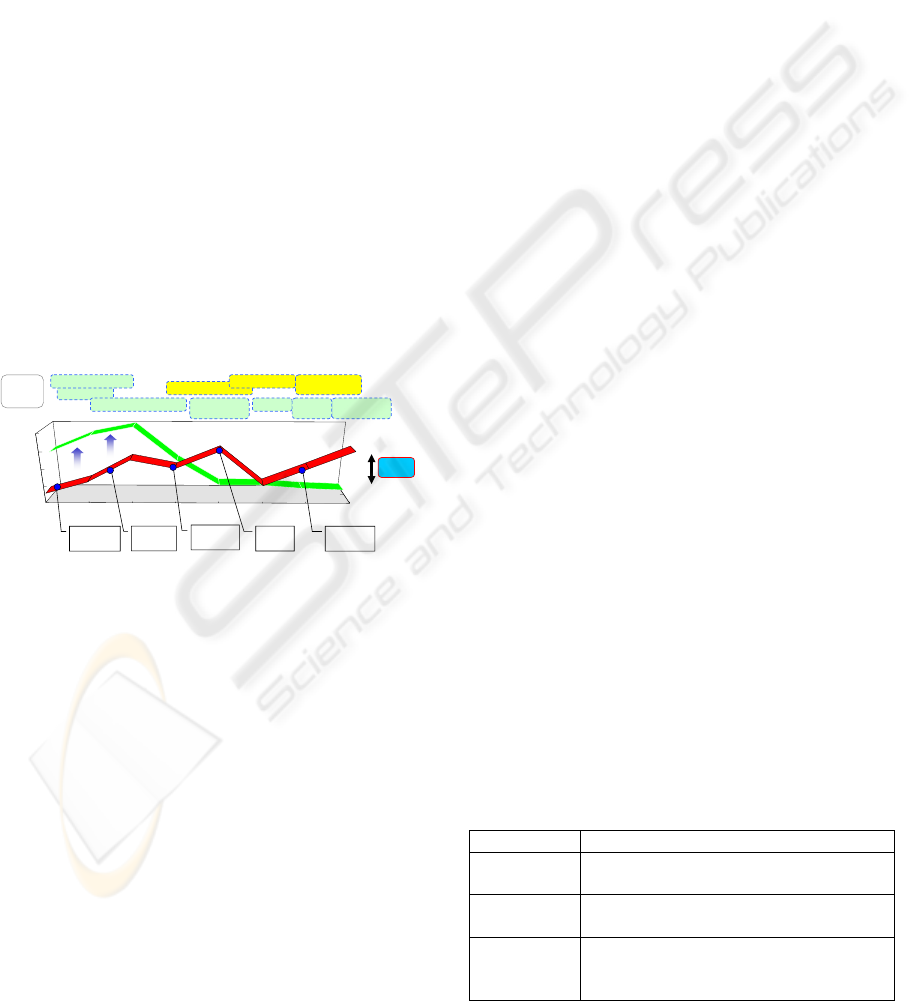
in dealing with inherent quality errors or claims
from customers. Such waste can be prevented by
making collaboration in the early stages as done by
leading companies. Experts in each process gather
and make lots of discussion with each other to
reduce errors possibly occurring during and after
production. By doing so, they do not encounter
many after-sales troubles even though they spent
much time and effort in early stages. In short,
collaboration in the early stages produces a big
difference in quality of final products.
Enterprises must capture, manage, and leverage
their intellectual assets to differentiate themselves.
The best way is to use the right application which
supports collaboration. Collaboration is the most
important factor to increase a company’s flexibility
and agility to respond swiftly to changing market
pressures and competitors. Collaboration is being
viewed as the next big wave after e-Commerce,
digital commerce and several other variants that
have emerged over the last decade [4-5]. According
to the outcomes of the e-Manufacturing project, as
illustrated from the following section, collaboration
systems can function as a good extranet as well as
intranet especially for SMEs who have insufficient
infrastructure or network facilities.
Pr o d u c t
Planning
Design Drawing Making
Molds
Reliabilit y Parts
Approval
Mas s
Production
Deliver
to Market
Korean SME
Leading Company
0
10
20
30
40
Manpower
Design Team
Product Planning Team
Product Development Team
Mold Subc ontractor s
Injection Company
Qualit y/Reliabilit y
Te a m
Purchasing
Qualit y Control
of Final Product s
Mass
Production
Post - produc tion,
Assembly Company
Qu a l i t y
Ga p
Majo r
Ac t o r s
La c k o f
planning skill &
collaborat ion
La c k o f
design skill
La c k o f
Te chnology of
subco ntract o rs
Fr e q u e n t
change s in
design
Inherent e rrors
in quality are
repeat ed
Collaboration
Figure 1: Comparison of product development lifecycle.
2 E-MANUFACTURING
e-Manufacturing can be referred to as a system
methodology enabling integration of manufacturing
operations and functional objectives of an enterprise
by using intelligent IT technologies such as Internet,
tether-free communication methods including
wireless networking or web-based connections(Ryu
et al., 2004). It is a novel concept or paradigm in
manufacturing areas used to meet the requirements
for the complete integration of all business
participants including suppliers, manufacturing
elements, and customers through the effective use of
web-enabled technologies.
e-Manufacturing does more than just connect the
Internet to the shop floor. It provides a fundamental
change in a enterprises’ strategic value proposition.
It is a collection of systems, processes, and
technologies supporting and enabling manufacturers
to collaborate with others. To effectively embody
collaboration, the following tools are developed;
Tools for data mining, transforming, and
transferring to manufacturing facilities via
web-enabled applications,
Intelligent methods and tools for monitoring,
predicting, and resolving undesirable events
such as deterioration, trend of performance
loss, machine faults or failures, etc.,
Tools for optimizing processes and operations
to improve system performance,
Synchronization tools for integrating systems
associated with e-Manufacturing such as MES
(Manufacturing Execution System), PLM
(Product Lifecycle Management), etc.,
Tools for satisfying customers by providing
qualified services including engineering
services, technical assistance, consulting, etc.,
Collaboration methods and applications
enabling companies to cooperate with others
amicably by supporting easy sharing of
data/information/knowledge.
e-Manufacturing project was launched as a pilot
program by both central and regional governments
to build up infrastructure to promote collaboration
and technology development among companies in
2004. The industrial section where the collaboration
system first applied was injection-mold. However, it
will be enlarged to other major industrial sections
including automobile, machinery, electronics, etc.
Furthermore, the application region of the project
will be spread out from the metropolitan area to
local areas as well as overseas countries. Note that
the number of SMEs who participated in the project
was 81 in 2005 and it becomes 210 in 2006. The
goal, model, and main characteristics of the e-
Manufacturing project can be summarized as
illustrated in Table 1.
Table 1: Outline of the e-Manufacturing project.
Description
Goal
To increase industrial competitiveness
and added value via collaboration
Model
Business innovation model including both
on-line and off-line collaboration
Characteristics
The project develops collaboration
systems via cooperation between
government and industrial entities
BUSINESS INNOVATION VIA COLLABORATION - e-Manufacturing: Web-based Collaboration Systems for SMEs
199