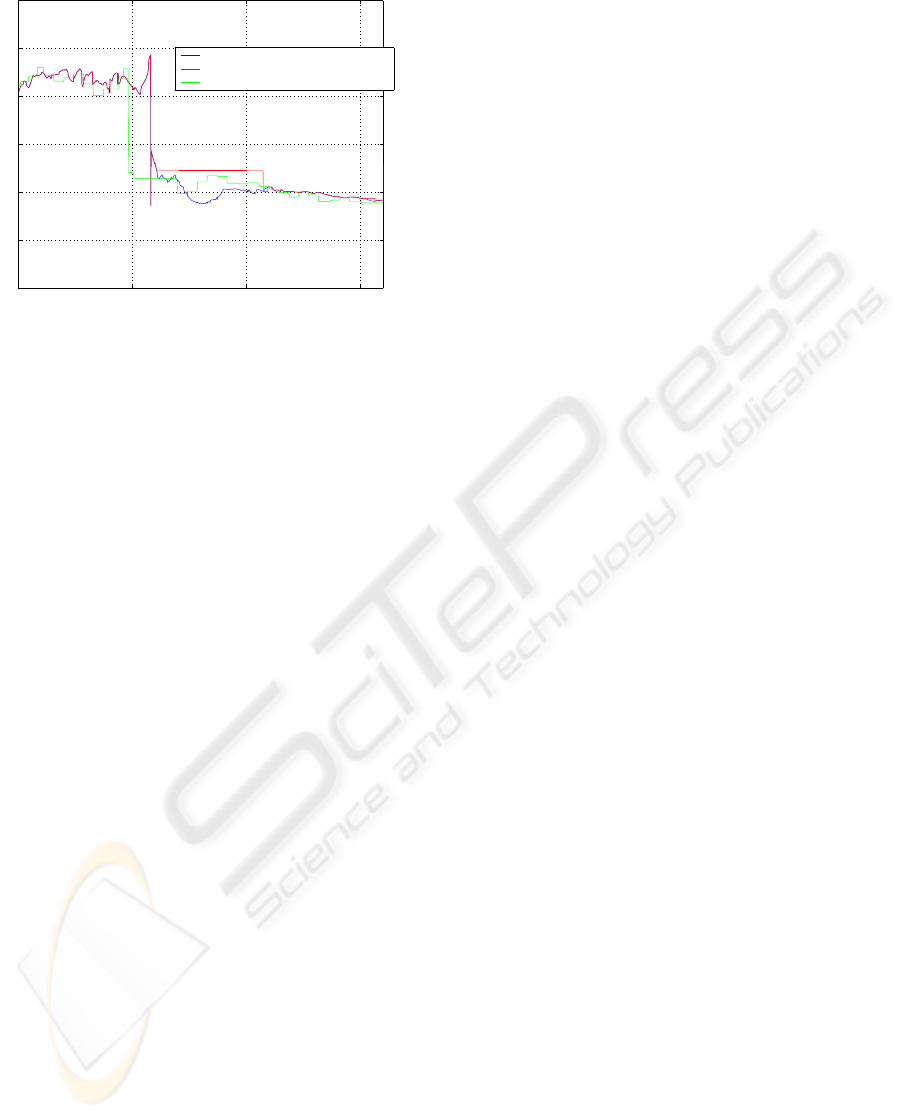
0 500 1000 1500
Validation period 3
Time (min)
Kappa number
Kappa prediction
Kappa prediction with monitoring
on−line Kappa measurement
Figure 6: Validation period 3.
ACKNOWLEDGEMENTS
This research study was funded by The Acedemy of
Finland, Mets
¨
a-Botnia Oy, Andritz Oy, Stora Enso
Oyj, Metso Automation Oy and the Finnish Funding
Agency for Technology and Innovation (Tekes). The
authors would like to thank the partners for the special
knowledge and process data provided.
REFERENCES
Ahvenlampi, T. and Kortela, U. (2005). Clustering algo-
rithms in process monitoring and control application
to continuous digesters. Informatica, 29(1):99–107.
Ahvenlampi, T., Rantanen, R., and Tervaskanto, M. (2006).
Fault tolerant control application for continuous kraft
pulping proces. In 6
th
IFAC Symposium on Fault
Detection, Supervision and Safety of Technical Pro-
cesses, Beijing, PR China.
Ahvenlampi, T., Tervaskanto, M., and Kortela, U. (2005).
Diagnosis system for continuous cooking process. In
16
th
IFAC World Congress, Prague, Czech Republic.
Blanke, M., Kinneart, M., Lunge, J., and Staroswiecki,
M. (2003). Diagnosis and Fault-Tolerant Control.
Springer-Verlag, Berlin.
Dash, S., Rengaswamy, R., and Venkatasubramanian, V.
(2003). Fuzzy-logic based trend classification for fault
diagnosis of chemical processes. Computers & Chem-
ical Engineering, 27:347–362.
Gullichsen, J. (2000). Chemical engineering principles of
fiber line operations. In Gullichsen, J. and Fogelholm,
C.-J., editors, Chemical Pulping. Papermaking Sci-
ence and Technology, Book 6A. Fapet Oy, Jyv
¨
askyl
¨
a,
Finland.
Gustafson, R. G., Sleicher, C. A., McKean, W. T., and Fin-
layson, B. A. (1983). Theoretical model of the kraft
pulping process. Ind. and Eng. Chem., Process Design
and Development, 22(1):87–96.
Hatton, J. V. (1973). Development of yield prediction equa-
tions in kraft pulping. Tappi J., 56(7):97–100.
Isermann, R. (1997). Supervision, fault-detection and fault-
diagnosis methods - an introduction. Control Engi-
neering Practice, 5(5):639–652.
Kohonen, T. (1997). Self-Organizing Maps. Springer-
Verlag, Berlin, Germany, second edition.
Leivisk
¨
a, K. (2000). Process Control. Papermaking Sci-
ence and Technology, Book 14. Fapet Oy, Helsinki,
Finland.
Mahmoud, M., Jiang, J., and Zhang, Y. (2003). Active
Fault Tolerant Control Systems. Lecture Notes in
Control and Information Sciences. Springer-Verlag,
Berlin, Germany.
Puranen, T. (1999). Jatkuvatoimisen sellukeittimen
h
¨
airi
¨
ontunnistus sumealla logiikalla (in finnish). In
Automation’99 -Seminar, pages 406–411, Helsinki,
Finland.
Qian, Y., Li, X., Jiang, Y., and Wen, Y. (2003). An ex-
pert system for real-time fault diagnosis of complex
chemical processes. Expert Systems with Applica-
tions, 24:425–432.
Rantanen, R. (2006). Modelling and control of cooking de-
gree in conventional and modified continuous pulping
processes. PhD thesis, University of Oulu, Oulu.
Rantanen, R., Ahvenlampi, T., and Kortela, U. (2003).
Kappa number profile in continuous cooking - ap-
plying Gustafson’s model to softwood and hardwood
pulping process. In 4
th
Biennial Johan Gullichsen
Colloquium, pages 83–92, Espoo, Finland.
Rantanen, R., Simil
¨
a, E., and Ahvenlampi, T. (2005). Mod-
eling of kappa number in Downflow Lo-Solids
T M
cooking using Gustafson’s model. Pulp & Paper
Canada, 106(5).
Simani, S. and Patton, R. J. (2002). Model-based data-
driven approach to robust fault diagnosis in chem-
ical processes. In 15th Triennial World Congress,
Barcelona, Spain. IFAC.
Tervaskanto, M., Ahvenlampi, T., Rantanen, R., and Ko-
rtela, U. (2005). Fault diagnosis of continuous cook-
ing process using intelligent sensors. In NeCST Work-
shop, pages 187–192, Ajaccio, France.
Venkatasubramanian, V., Rengaswamy, R., and Kavuri,
S. N. (2003a). A review of process fault detection and
diagnosis part II: Qulitative models and search strate-
gies. Computers & Chemical Engineering, 27:313–
326.
Venkatasubramanian, V., Rengaswamy, R., Yin, K., and
Kavuri, S. N. (2003b). A review of process fault
detection and diagnosis part I: Quantitative model-
based methods. Computers & Chemical Engineering,
27:293–311.
Vroom, K. E. (1957). The h-factor, a means of expressing
cooking times and temperatures as a single variable.
Pulp. Pap. Mag. Can., 58(3):228–231.
ICINCO 2007 - International Conference on Informatics in Control, Automation and Robotics
166