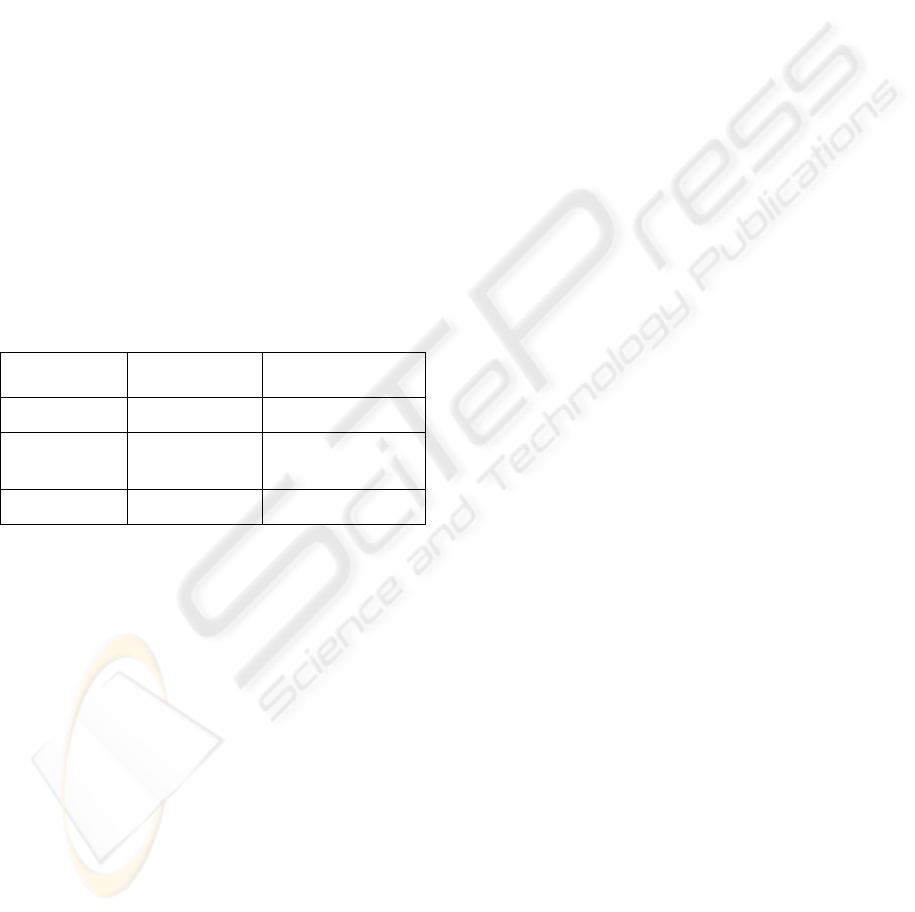
levels (Lee et al, 2004, and Fleisch and Tellkamp,
2005). Based on average turnover ratio of about 5
and gross profit ratio of 70%, inventory shrinkage is
closer to 12% of inventory levels. Inventory
shrinkage cannot go undetected forever. We assume
that once every quarter (at the time of preparation of
quarterly financial statements) the shrinkage will be
detected and the information system is corrected to
reflect actual count. Many use quarterly reset of the
system inventory for the detection of inventory
shrinkage. We simplify this situation by running
simulation for a quarter at a time. To mitigate the
effect of initial conditions, and to obtain steady state
results, we use a warmup period of 10 days (run
length is 120 days). To obtain robust results we
repeated the simulation for 25 quarters.
6 RESULTS
Table 2 compares cycle times with incorrect
inventory records and perfect inventory counts
obtained by deploying RFID technologies.
Table 2: Comparison of Supply Chain Performance.
Accurate
Inventories
Inaccurate
Inventories
Mean 2.002 Hours 2.646 Hours
Standard
Deviation
1.125 Hours 1.165 Hours
Sample Size 25 25
Hypothesis test resulted in a t-value of 1.988 and
a p-value of .026. Based on these statistics we
conclude that accurate inventories result in lower
cycle time and faster fulfilment of purchase orders.
The analysis of the simulation results is not yet
completed. Sensitivity of cycle times to
manufacturing times, capacities and other important
parameters are being established. Other important
supply chain performance criteria are being
examined. The framework and the model we have
established so far will enable us to extend the
analysis of supply chain performance measures with
accurate inventory counts now possible with RFID
tags.
7 CONCLUSIONS
Our research addresses important issues related to
the role of RFID in supply chain management.
Accurate inventory data is especially important in
lean manufacturing environments as large inventory
buffers and excess safety stock are not available to
forgive inventory inaccuracies. Our simulation
model consisting of a pull production environment
concludes that the cycle time (time it takes to fill a
purchase order) is reduced by accurate inventory
counts. The performance of a supply chains using
alternative performance criteria and the sensitivity of
performance to parameters of the production
environment are currently developed.
REFERENCES
Chen, F., Drezner, Z., Ryan, J.K., and Simchi-Levi, D.,
2000. Quantifying the Bullwhip Effect in a Simple
Supply Chain: The Impact of Forecasting Lead Times,
and Information. Management Science, 46, 436-443.
Dabney, D., Hollinger, R., and Dugan, L., 2004. Who
Actually Steals? A Study Of Covertly Observed
Shoplifters, Justice Quarterly, 21, 693-728.
Fleisch, E., and Tellkamp, C., 2005)\. Inventory
Inaccuracy and Supply Chain Performance: A
Simulation Study of Retail Supply Chain. International
Journal of Production Economics, 95, 373-385.
Ganeshan, R., Boone, T., and Stenger, A., 2001. The
Impact of Inventory and Flow Planning Parameters on
Supply Chain Performance: An Exploratory Study.
International Journal of Production Economics, 71,
111-118.
Iglehart, D.L., and Morey, R.C., 1972. Inventory Systems
with Imperfect Asset Information. Management
Science, 18, B388-B394.
Joshi, Y., 2000. Information Visibility and Its Effect on
Supply Chain Dynamics. Masters Degree Thesis, MIT.
Kang, Y., and Gershwin, S.B., 2005. Information
Inaccuracy in Inventory Systems: Stock Loss and
Stockout. IEEE Transactions, 37, 843-859.
Kohn, L., Corrigan, J. and Donaldson, M., (Eds.), 2000.
To Err Is Human: Building a Safer Health System,
National Academies Press, Washington, D.C.
Lee, Y.M., Cheng, F., and Leung, Y.T., 2004. Exploring
the Impact of RFID on Supply Chain Dynamics.
Proceedings of the 2004 Winter Simulation
Conference. December 5-8, 2004. Washington, D.C.
Raman, A., DeHoratius, N. and Ton, Z., 2001. Execution:
The Missing Link in Retail Operations. California
Management Review, 43, 136-152.
Taylor, D., 2004. Supply Chains: A Manager’s Guide,
Addison Wesley, Boston, MA.
Wendel S., 2000. Medical errors: Institute of Medicine
report raises questions about technology. Healthcare
Informatics, 17, 37-38.
THE BENEFITS OF ACCURATE, AND TIMELY DATA IN LEAN PRODUCTION ENVIRONMENTS - RFID in
Supply Chain Management
225