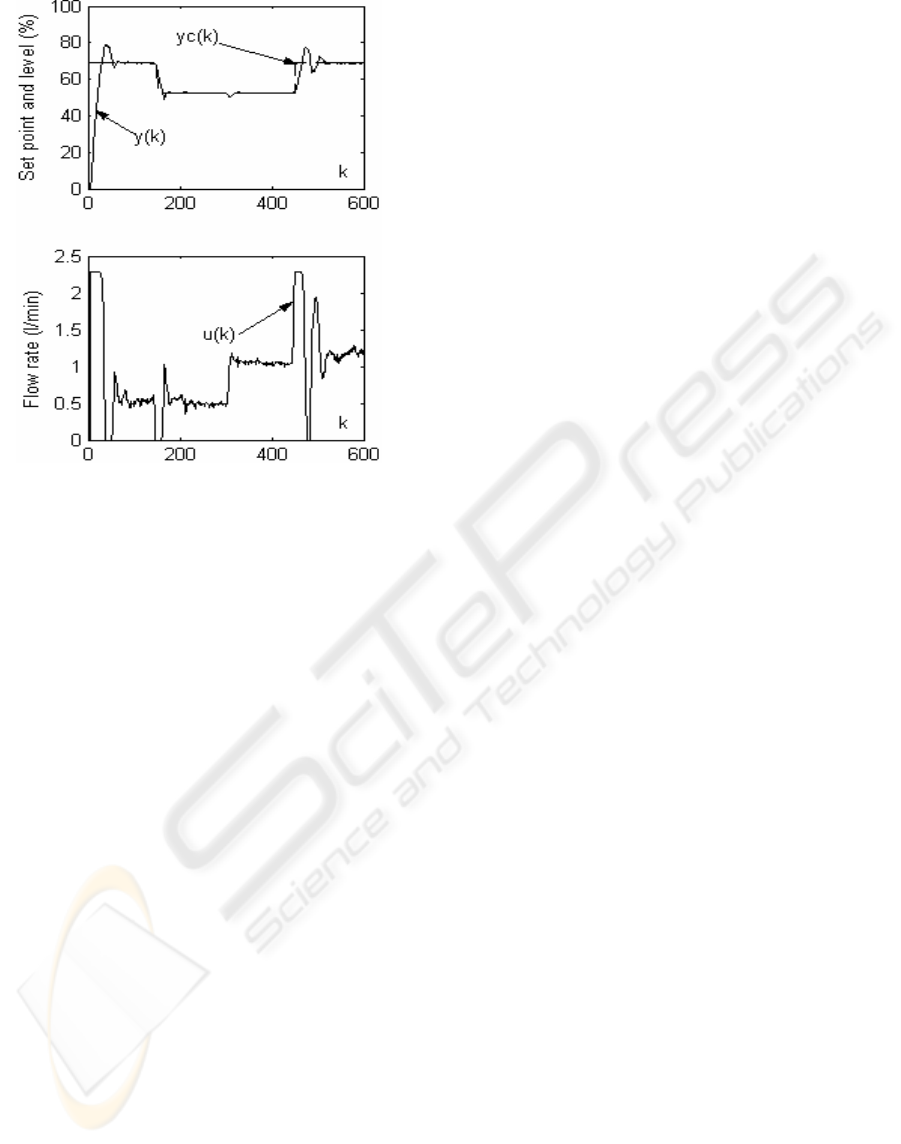
Figure 7: MOGPC (multi objective strategy)
(N
2
= 7; N
u
= 1; 1=
)
5 CONCLUSIONS
This paper has presented the multi objective
predictive control. The process is characterized by a
set of CARIMA model. Since considered models are
linear, performance criteria are convex.
Consequently, the weighted sum approach is used to
compute the Pareto optimal set. An application of
the studied strategy to a nonlinear model plant has
been also presented.
REFERENCES
Andrès-Toro B., E. Besada-Portas, P. Fernandez-Blanco,
J. A. Lopez-Orozco, and J. M. Giron-Sierra, 2002,
“Multiobjective optimization of dynamic processes by
evolutionary methods”. Proc. 15
th
IFAC World
Congress, Barcelona, Spain.
Ben Abdennour R., P. Borne, M. Ksouri, F. M’sahli, 2001,
“Commande numérique et identification des procédés
industriels”. Editions TECHNIP, Paris.
Boucher P., and D. Dumur, 1996 “La commande
prédictive”. Editions TECHNIP, Paris.
Borne P., G. Dauphin Tangay, J. P. Richard, F. Rotella, I.
Zambe Hakis, 1993, "Analyse et régulation des
processus industriels", Tome 2. Régulation
numérique. Editions TECHNIP, Paris.
Brdys M. A. and T. Chang, 2002, “Robust model
predictive control under output constraints”. Proc. 15
th
IFAC Triennial World Congress, Barcelona/Spain.
Brian A., Vinay P., and B. W. Bequette, 2001, “A
comparison of fundamental Model based and Multiple
Model Predictive Control”. Proc. 40
th
IEEE
conference on Decision and Control, Orlando, Florida
USA, 4863-4868.
Clarke D. W., C. Mohtadi and P. S. Tuffs, 1987,
“Generalized predictive control”. Part I and Part II,
Automatica, 23, 2, 137- 160.
Colette. Y., Siarry. P., 2002, “Optimisation multiobjectif”.
Editions EYROLLES.
Gutierrez A. J. and E. F. Camacho, 1995, “Robust
adaptive control for processes with bounded
uncertainties”. Third European control conference.
Rome/Italy, 1295-1300.
Oliveira G. H. C., W. C. Amaral, G. Favier and G. A
Dumont, 2000, “Contrained robust predictive
controller for uncertain processes modelled by
orthonormal series function”. Automotica, 36, 563-
571.
Ramirez D. R., T. Alamo and E. F. Camacho, 2002,
“Efficient Implementation of constrained Min-Max
model Predictive Control with Bounded
Uncertainties”. Proc. IEEE Conference on Decision
and Control.
Silva V.V.R. and P.J. Fleming, 2002, “Control
configuration design using evolutionary computing”.
Proc. 15
th
IFAC World Congress, Barcelona, Spain.
William Y. S., P. M.Donald and R.Y. Brent, 2000, “A real
time approach to process control”. John Wiley &
Sons, Ltd.
Xin Q., Murti V. S., Petros G. V., and Mustafa K., 2004,
“Structured optimal and robust control with multiple
criteria: a convex solution”. IEEE Trans. on Automatic
Control, 49, 10, 1623-1640.
ICINCO 2005 - SIGNAL PROCESSING, SYSTEMS MODELING AND CONTROL
238