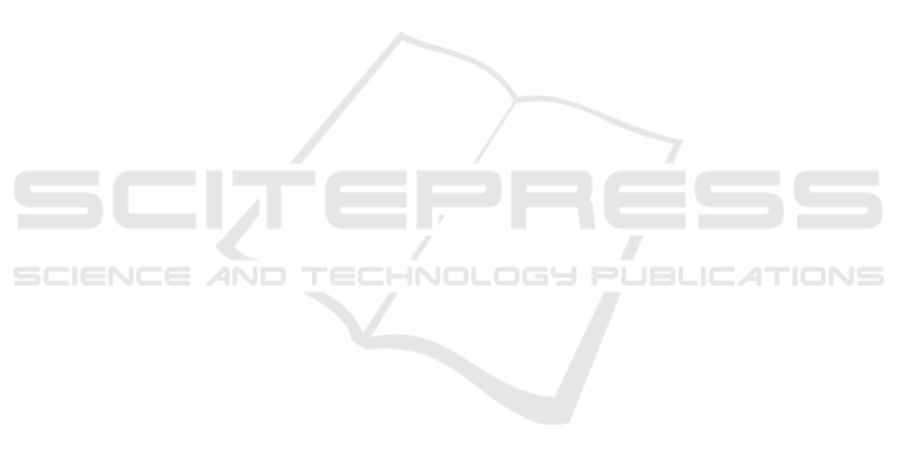
or from mobile terminals. The central level of the
company’s architecture contains the ERP. It orches-
trates the production on corporate level and commu-
nicates the company’s strategies to plants to be trans-
lated by the MES as orders to the Shopfloor.
5 CONCLUSION AND FUTURE
WORK
At the present time, digitization of processes has be-
come a must for companies that feel the need to op-
timize their costs, to keep up with the customers’ de-
mands and to lead over their competitors. This digiti-
zation is done by connecting the virtual world to the
real one using several technologies such us, data sen-
sors, IT Systems and cyber-physical systems. How-
ever, the usage of many systems and technologies in
the same environment can be really challenging, due
to the differences between them and particularities of
each one of them.
For that, we proposed in this paper a reference
architecture for computer integrated manufacturing,
which is able to encompass every system in the CIM
context. This architecture is based on the ISA-95
standard and takes into consideration six major as-
pects: Data integration, Systems integration, Secu-
rity, Monitoring & Data analysis, Mobility and finally
Cloud computing. However, much work remains to
be done in order to identify other aspects that can be
interesting in the CIM context and can also be handled
by our architecture.
REFERENCES
Bousdekis, A., Papageorgiou, N., Magoutas, B., Apostolou,
D., and Mentzas, G. (2015). A real-time architecture
for proactive decision making in manufacturing enter-
prises. In OTM Confederated International Confer-
ences On the Move to Meaningful Internet Systems.
SpringerLink.
Brandl, D. and Consulting, B. (2008). What is isa-95? in-
dustrial best practices of manufacturing information.
Caggiano, A., Segreto, T., and Teti, R. (2016). Cloud manu-
facturing framework for smart monitoring of machin-
ing. In CIRP Global Web Conference Research and
innovation for future Production. ScienceDirect.
Hedberg, T., Feeney, J. A. B., and Helun, M. (2016). To-
ward a lifecycle information framework and technol-
ogy in manufacturing. In Journal of Computing and
Information Science in Engineering.
Leit
˜
ao, P., Barbosa, J., Foehr, M., Cal
`
a, A., Perlo, P.,
Iuzzolino, G., Petrali, P., J.Vallhagen, and Colombo,
A. W. (2017). Instantiating the perform system ar-
chitecture for industrial case studies. In Interna-
tional Workshop on Service Orientation in Holonic
and Multi-Agent Manufacturing. SpringerLink.
Li, Q., Jiang, H., Tang, Q., Chen, Y., Li, J., and Zhou, J.
(2017). Smart manufacturing standardization model
and standards framework. In OTM Confederated In-
ternational Conferences On the Move to Meaningful
Internet Systems. SpringerLink.
Li, Q., Pu, Y., Xu, Z., Wei, H., Tang, Q., Chan, I., Jiang, H.,
Li, J., and Zhou, J. (2019). Architecture of integra-
tion of industrialization and informatization. In OTM
Confederated International Conferences On the Move
to Meaningful Internet Systems. SpringerLink.
Lia, Q., Tanga, Q., Chana, I., Weia, H., Pua, Y., Jiangb,
H., Lib, J., and Zhou, J. (2018). Smart manufactur-
ing standardization: Architectures, reference models
and standards framework. In Computers in Industry.
ScienceDirect.
Menezes, S., Creado, S., and Zhong, R. Y. (2018).
Smart manufacturing execution systems for small and
medium-sized enterprises. In CIRP Conference on
Manufacturing Systems. ScienceDirect.
Meziane, F., Vadera, S., and Proudlove, N. (2000). In-
telligent systems in manufacturing: Current develop-
ments and future, article in integrated manufacturing
systems.
OPC Foundation (2021). What is opc. https://
opcfoundation.org/about/what-is-opc/.
Oxenhandler, D. (2003). Designing a secure local area net-
work. SANS Institute.
Radovilsky, Z. and Bidgoli, H. (2004). The Internet Ency-
clopedia, Volume 1. John wiley & sons, inc edition.
Remli, A., Khtira, A., and Elasri, B. (2020). Computer in-
tegrated manufacturing architecture: A literature re-
view.
Sprock, T. and McGinnis, L. F. (2015). A conceptual model
for operational control in smart manufacturing sys-
tems. In International Federation of Automatic Con-
trol. Sciencedirect.
Tang, H., Li, D., Wang, S., and Dong, Z. (2018). Casoa: An
architecture for agent-based manufacturing system in
the context of industry 4.0. In IEEE Access. IEEE.
Tao, F., Qi, Q., Liu, A., and Kusiak, A. (2018). Data-driven
smart manufacturing. In Journal of Manufacturing
Systems. ScienceDirect.
Thames, L. and Schaefer, D. (2016). Software-defined
cloud manufacturing for industry 4.0. In Procedia
CIRP. ScienceDirect.
Tolio, T., Saccob, M., Terkajb, W., and Urgo, M. (2013).
Virtual factory: an integrated framework for manufac-
turing systems design and analysis.
Weihraucha, D., Schindlera, P. A., and Sihna, W. (2018). A
conceptual model for developing a smart process con-
trol system. In CIRP Conference on Intelligent Com-
putation in Manufacturing Engineering. ScienceDi-
rect.
Xiaodong, D., Quan, W., Pengfei, Y., Haijing, Z., Yuyan,
H., Haitao, W., and Zhongbin, P. (2012). Security sys-
tem for internal network printing. CPS.
Zhao, W., Shi, G., and Cui, Y. (2018). The planning, design
and application of mes. In ICITEE 18: International
Congress of Information Technology & Electrical En-
gineering -2018. ACM digital library.
ICEIS 2021 - 23rd International Conference on Enterprise Information Systems
334